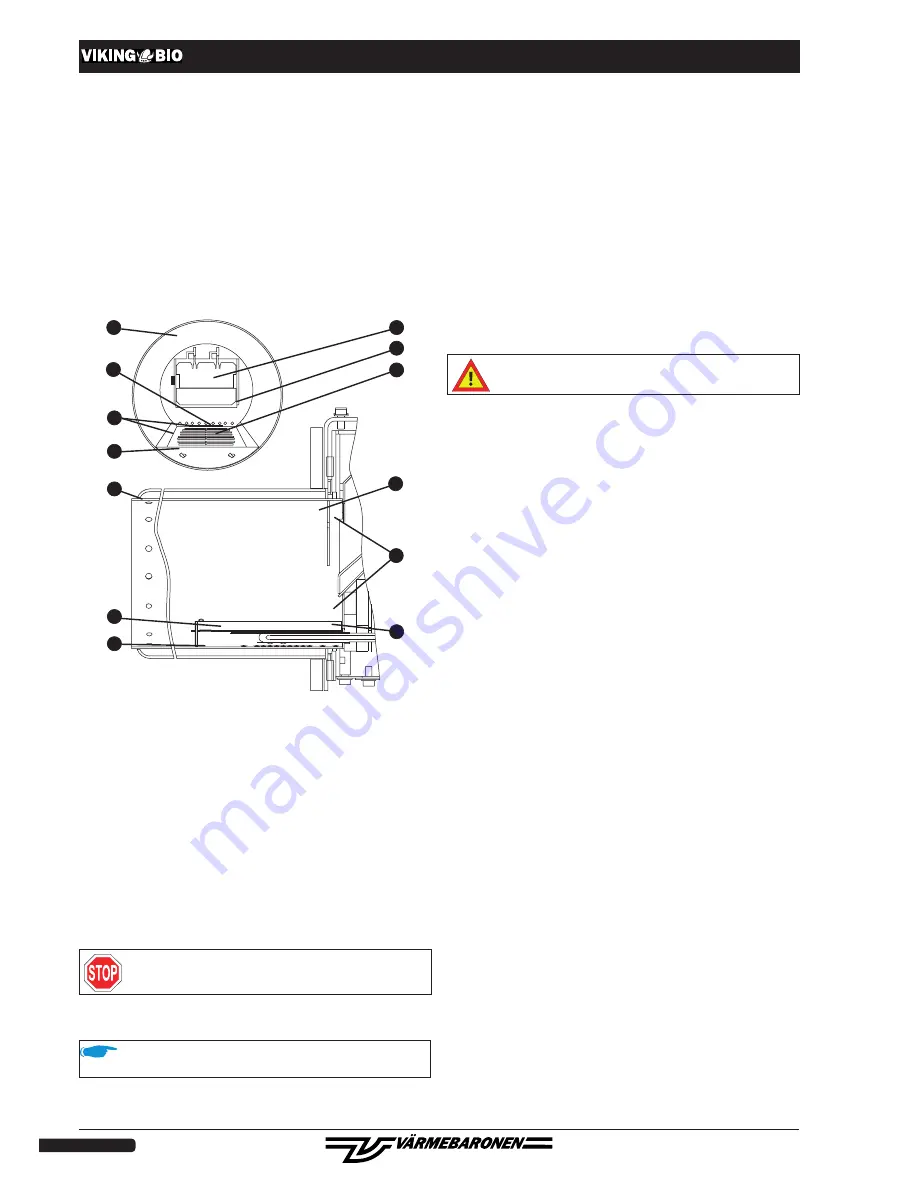
1101
Illustrations may differ from actual product
Subject to printing/proofreading errors
1 2
Startup
Before starting the burner for the first time, check that:
• it has been installed according to the instructions.
• the feed auger's inclination is 40 ±5°.
• there is a draught damper and it is adjusted to -5 Pa.
• all control units are correctly set.
• the burner has sufficient combustion air.
• there are pellets up to the burner.
• the grate is in the correct position and the lip is in place.
Position of grate
The grate must be positioned as shown in the figures below. If the grate is
in the wrong position, the ignition time is extended or ignition may fail. The
ignition element may also be damaged.
a
b
c
d
c
d
e
e
f
f
g
g
h
a. Cross-section, inner burner
pipe at front edge of grate.
b. Cross-section, burner
pipes in their longitudinal
direction.
c. End wall.
d. Grate.
e. Lip. Prevents pellets from bouncing out
into the combustion chamber/reduces
heat radiation.
f. The grate must be in contact with the
end wall. There must be a small gap at
its rear edge.
g. The grate must be in contact with the
burner pipe.
h. Gap.
Feed auger
The feed auger must be filled before the burner is started. This is done by
connecting the feed auger to an earthed wall outlet. Place a collection re-
ceptacle below the hose and operate the feed auger so that 25-30 litres of
pellets pass through.
Risk of crushing!
Do not insert hands or objects in the feed auger.
Draught requirements
The chimney must be fitted with a draught damper that is ap-
propriate for the chimney.
For good operating economy and reliable ignition, the chimney draught
should be
≤
5 Pa. Under certain circumstances, the draught may be difficult
to adjust. The chimney draught affects the time it takes for the burner to
establish a flame. Switch SW2/2 is used to set the draught.
Flue gas temperature
Condensation damage can be avoided if the flue gas temperature is mini-
mum 70 °C one metre below the top of the chimney. A low flue gas tem-
perature results in higher efficiency but this must be weighed up against
the risk of condensation. The temperature is measured when the boiler is
at its normal operating temperature no earlier than five minutes after the
burner was started and with the draught damper closed.
Measures to increase the flue gas temperature:
• remove any turbulators or baffle plates in the boiler.
• insulate the boiler's flue pipe and the chimney in cold rooms.
• increase the capacity of the burner
• install flue lining tubes
To avoid damage to the chimney, the flue gas temperature
must be checked.
Turbulators
Certain boiler types have or can be fitted with flue gas turbulators. Their
task is to make the flue gases turbulate to extract more heat and thus in-
crease efficiency.
At low burner power, the flue gas temperature is low and there is a risk of
condensation forming in the chimney. Try to shorten the turbulators until a
suitable flue gas temperature is obtained.
Smoke in boiler room
If the system's hatches and dampers are not airtight, there is a risk of
smoke entering the boiler room, in particular if excess pressure is formed
in the combustion chamber. A smoke detector is a good way of discovering
whether flue gases are leaking out into the boiler room.
The boiler hatches must be closed when the burner is in operation.
Combustion values
Correct adjustment is important for good heating economy, high efficiency,
low emissions of environmentally hazardous substances and the service
life of the parts of the burner in contact with the flame. Optimum adjust-
ment is possible only using flue gas analysis instruments. The boiler room
door must be closed during measurement.
The values indicate how combustion should be. Please note that the values
vary somewhat during the firing phase:
Flue gas temperature:
160 °C (depending on chimney type)
Efficiency:
>90%
CO content:
<300 ppm
CO2 content, average:
12.5% ( ±2.5%)
Boiler temperature:
60-80 °C
Soot number:
1-3.