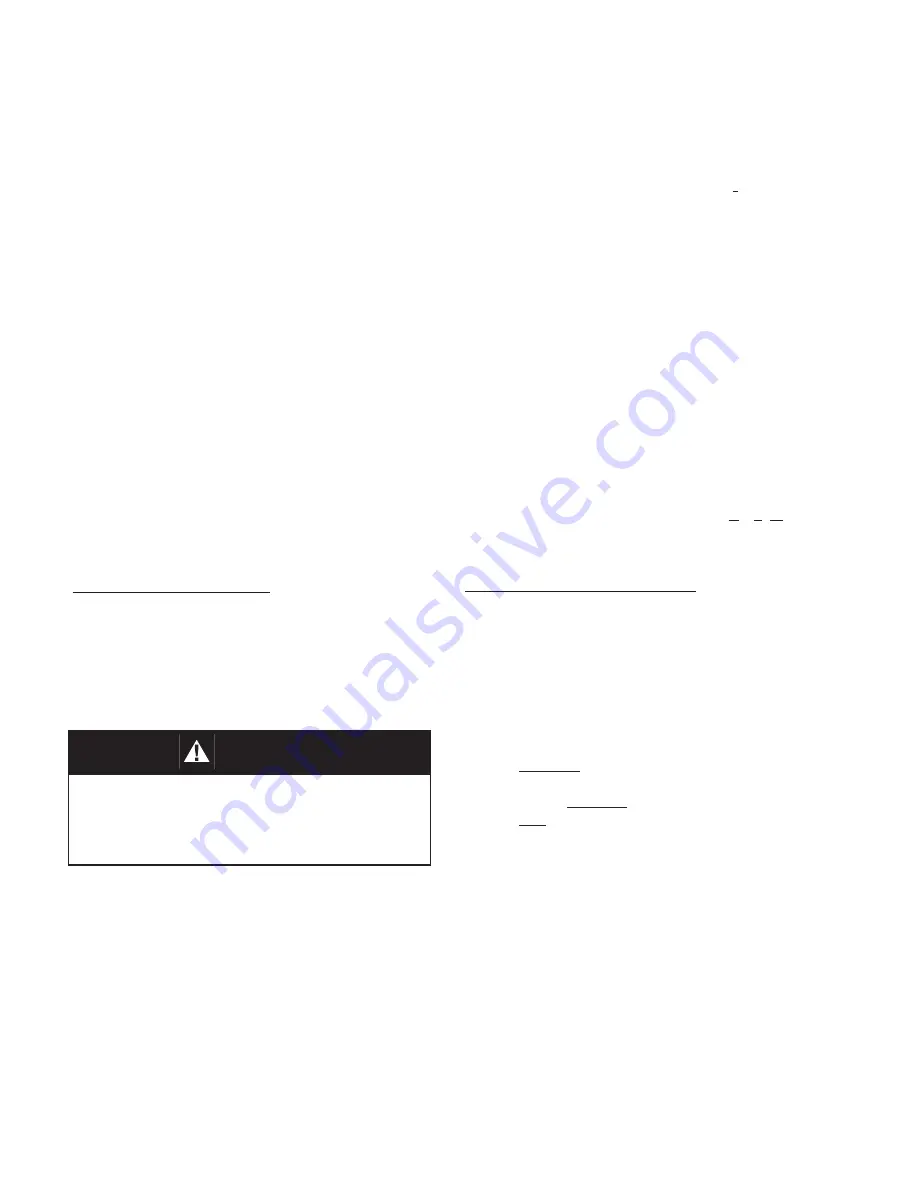
8
IOM-5400
v. Install jack screw (121) on threaded
end of pallet guides and tighten securely.
Rotate jack nut (123) CW in equal
increments until they rest tight against
lower case (114). Rotate jam nut (122) CW
to secure tight to jack nut (123).
w. Install new piece of joint tape and
diaphragm (129 and 117). Position and
align bolt holes in the circumference of the
diaphragm with the holes in the lower case
(114).
x. Reposition upper case assy (118) on
diaphragm (117). Align match marks made
in step B. 1. a. previous. Install cap screws
(119) and nuts (120) and tighten.
y. Install pilot body assembly on nipple
(124) tight with CW rotation. Ensure
the straight connector (126) of the pilot
valve assembly is directly above sensing
tube connector (125) of the main valve
assembly.
z. Reconnect tubing (127) to fittings
(125),(126).
SECTION VIII
NEW REPLACEMENT UNIT:
Contact your local Cashco, Inc., Sales Rep re sen ta-
tive with the Serial Number and Product code. With
this information they can provide a quotation for a
new unit including a complete description, price
and availability.
VIII. ORDERING
INFORMATION
NEW REPLACEMENT UNIT vs PARTS "KIT" FOR FIELD REPAIR
To obtain a quotation or place an order, please retrieve the Serial Number and Product Code that was stamped
on the metal name plate and attached to the unit. This information can also be found on the Bill of Material
(“BOM”), a parts list that was provided when unit was originally shipped. (Serial Number typically 6 digits).
PARTS "KIT" for FIELD REPAIR:
Contact your local Cashco, Inc., Sales Rep re-
sen ta tive with the Serial Number and Product
code. Identify the parts and the quantity required
to repair the unit from the “BOM” sheet that
was provided when unit was originally shipped.
NOTE:
Those part numbers that have a quantity indi-
cated under "Spare Parts" in column "A” reflect
minimum parts required for inspection and
rebuild, - "Soft Goods Kit". Those in column “B”
include minimum trim replacement parts needed
plus those "Soft Goods" parts from column "A".
If the "BOM" is not available, refer to the cross-
sectional drawings included in this manual for
part identification and selection.
A Local Sales Representative will provide
quotation for appropriate Kit Number, Price
and Availability.
CAUTION
Do not attempt to alter the original construction of any
unit without assistance and approval from the factory.
All purposed changes will require a new name plate with
appropriate ratings and new product code to accom-
modate the recommended part(s) changes.
The contents of this publication are presented for informational purposes only, and while every effort has been made to ensure their accuracy, they are not to be
construed as warranties or guarantees, express or implied, regarding the products or services described herein or their use or applicability. We reserve the right to
modify or improve the designs or specifications of such product at any time without notice.
Cashco, Inc. does not assume responsibility for the selection, use or maintenance of any product. Responsibility for proper selection, use and maintenance of any
Cashco, Inc. product remains solely with the purchaser.