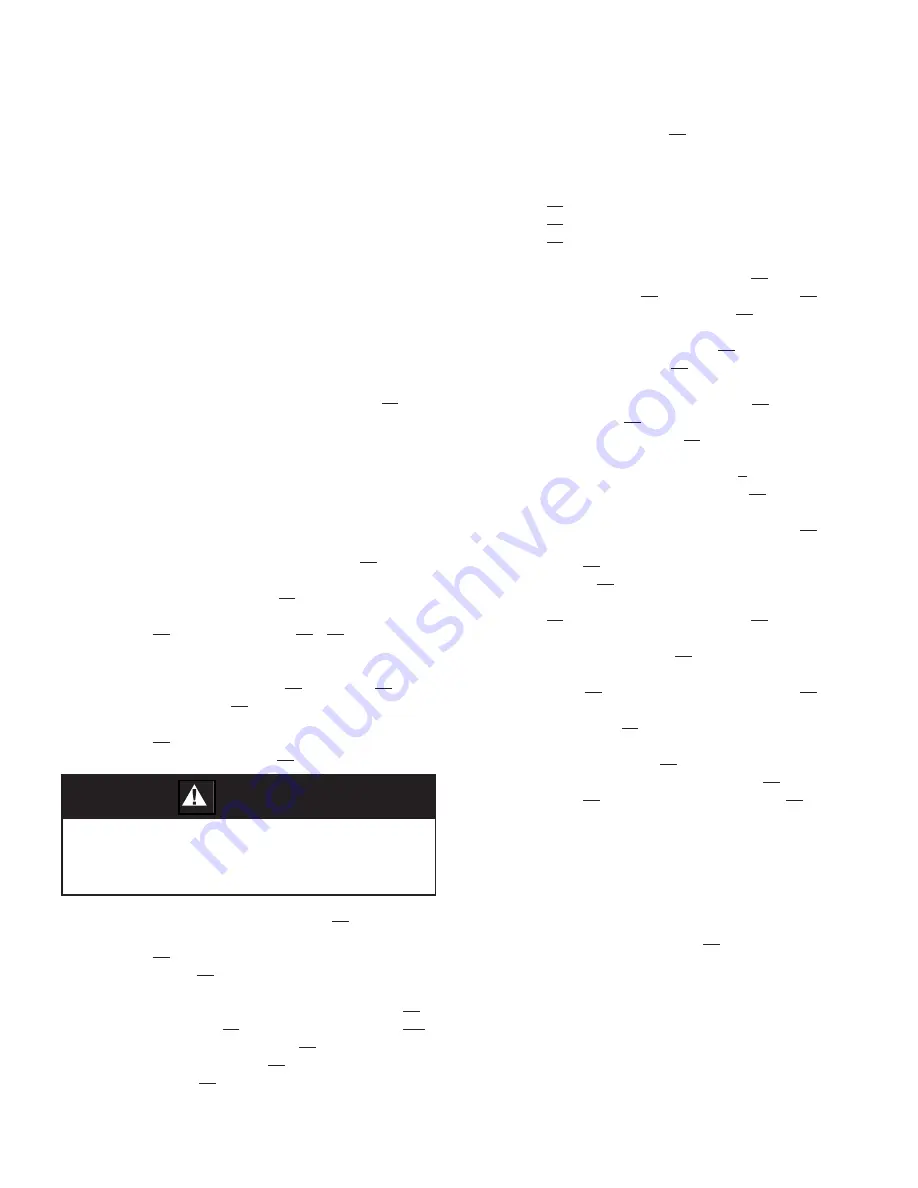
4
IOM-5400
SECTION VI
VI. PILOT MAINTENANCE
A. General:
1. Maintenance procedures herein after are
based upon removal of the pilot/vent valve
unit from the vessel/piping where installed.
2. Owner should refer to owner’s procedures for
re mov al, handling and cleaning of non re us-
able parts; i.e. gaskets, suitable solvents,
etc.
3. All indicated Item Numbers that are with
respect to the Pilot Assembly will be in
pa ren the sis and un der scored; i.e. (29). All
Item Numbers that are with respect to the
MainValve are not un der scored; i.e. (107).
B. Separation from Main Valve and Disassembly:
1. Disconnect sense tube (127) from sense
tube connectors (125) and (126). Remove
the pilot valve assembly from the nipple
(124) by rotating the pilot body (01) CCW.
2. Secure pilot body (01) in vise with ‘sens-
ing” port facing front. Disconnect tubing
(34) from connectors (32),(33).
3. Paint or embed a set of match marks be-
tween upper case (22), spacer (13) and
lower case (03) along flanged area.
Note
the location of 1/8” NPT tap from elbow
(33) in relation to body sensing port and
straight connector (32).
6. Lift range spring (20) and spring button
(21) up and set aside.
7. Insert a tool in the slot in the top of stud
(18) to prevent stud rotation. Rotate nut
(19) CCW to remove nut and spring guides
(17).
8. Remove sense pressure ring (15), sense
support plate (16), sense diaphragm (14)
and diaphragm case spacer (13).
9. Remove top bolt gasket (07), and sense
diaphragm spacer (12).
10. Remove boost support plate (11), boost
diaphragm (10), boost diaphragm spacer
(09) and bolt gasket (07).
FOR Pilot with Pressure > 3.2 psig:
remove boost pressure ring (36).
11. Rotate 7/16” hex head cap screws (04)
CCW to remove. Lift up on lower diaphragm
case (03) to remove lower case and body
gasket (02).
NOTE
the alignment of the
four bolt holes and the sense hole in case
(03) with the holes in the body (01).
12. Grasp spindle stud (18) and lift upwards to
extract the spindle assembly (06) from the
body (01). Remove seal diaphragm (08)
from spindle. With a pick type tool lift out
seat o-ring (05).
13. Rotate jam nut (27) CCW two rotations
and remove blowdown needle (28) from
body (01). Replace with new O-ring (30).
14. Inspect parts and replace if parts show
signs of wear. Clean parts with suitable
cleaner.
C. Re-assembly:
1. Insert new seat o-ring (05) in the bottom
of the spindle assembly. Place spindle
assembly inside the body cavity, threaded
end up. Slide a new seal diaphragm over
threaded end of spindle and position it
on top of the body. Align holes in seal
diaphragm with holes in body.
WARNING
SPRING UNDER COMPRESSION. Prior to re mov ing
flange bolts, relieve spring com pres sion by backing
out the adjusting screw. Failure to do so may result
in flying parts that could cause personal injury.
4. Rotate the closing cap (29) CCW for
removal. Loosen the adjusting screw nut
(27) two revolutions. Rotate Adjusting
screw (28) CCW and remove.
5. Remove diaphragm case nuts (19),
washers (25), and cap screws (26).
Grasp spring bonnet (23) and lift up until
diaphragm case (22) clears top of spring
button (21). Set assembly aside.