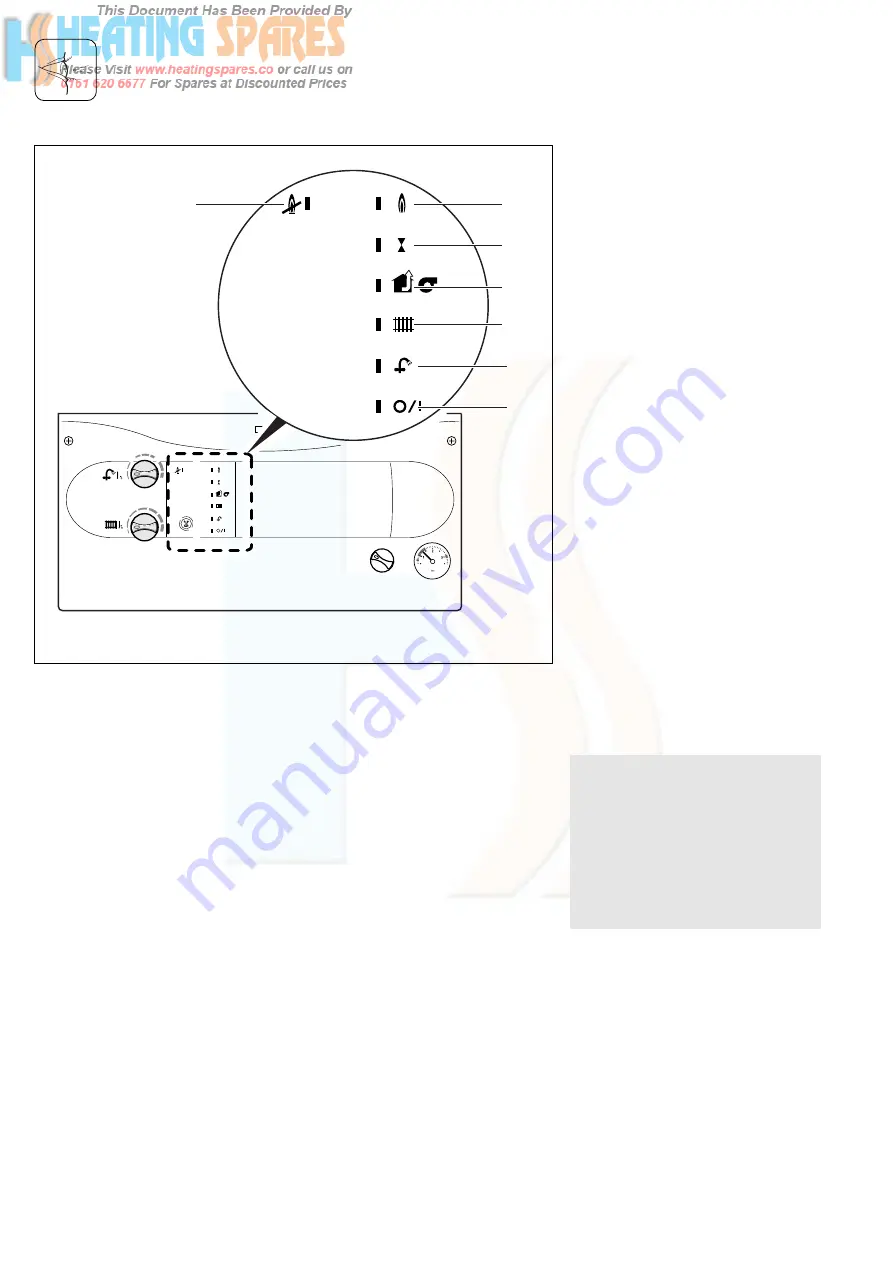
Supplied By www.heating spares.co Tel. 0161 620 6677
40
FUNCTIONAL CHECKS
(COMMISSIONING PART III)
Heating system
●
Ensure that the power on indicator
is illuminated (
1
).
●
Ensure that the maximum radiator
temperature control is turned to the
high position.
●
Ensure external controls are calling
for heat.
●
The central heating demand
indicator will illuminate (
3
).
●
Providing the boiler has not
achieved its set temperature, and
the anti-cycling control is not
activated, the boiler will start its
lighting sequence. Once the fan
and flue system have proved their
satisfactory operation the fan
operation indicator (
4
) will light.
●
The gas valve will open and
sparking will commence at the
burner. The ignition indicator (
5
)
will illuminate.
●
As soon as the burner has ignited
and the flame has been sensed the
flame indicator (
6
) will illuminate.
●
By illuminating in this sequence the
indicator lights have demonstrated
correct operation of the boiler for
CH.
Note:
Should the boiler fail to light it
will attempt 2 re-ignition sequences,
if the boiler still fails to light the
burner lock out indicator will
illuminate (
7
). This usually means
that the gas supply is turned off or
has not been purged of air. Check
the gas supply, push the reset button
and repeat the lightning procedure.
I
0
1
2
3
4
5
6
7
Fig. F.3: Functional check
Euro B/S 015/1