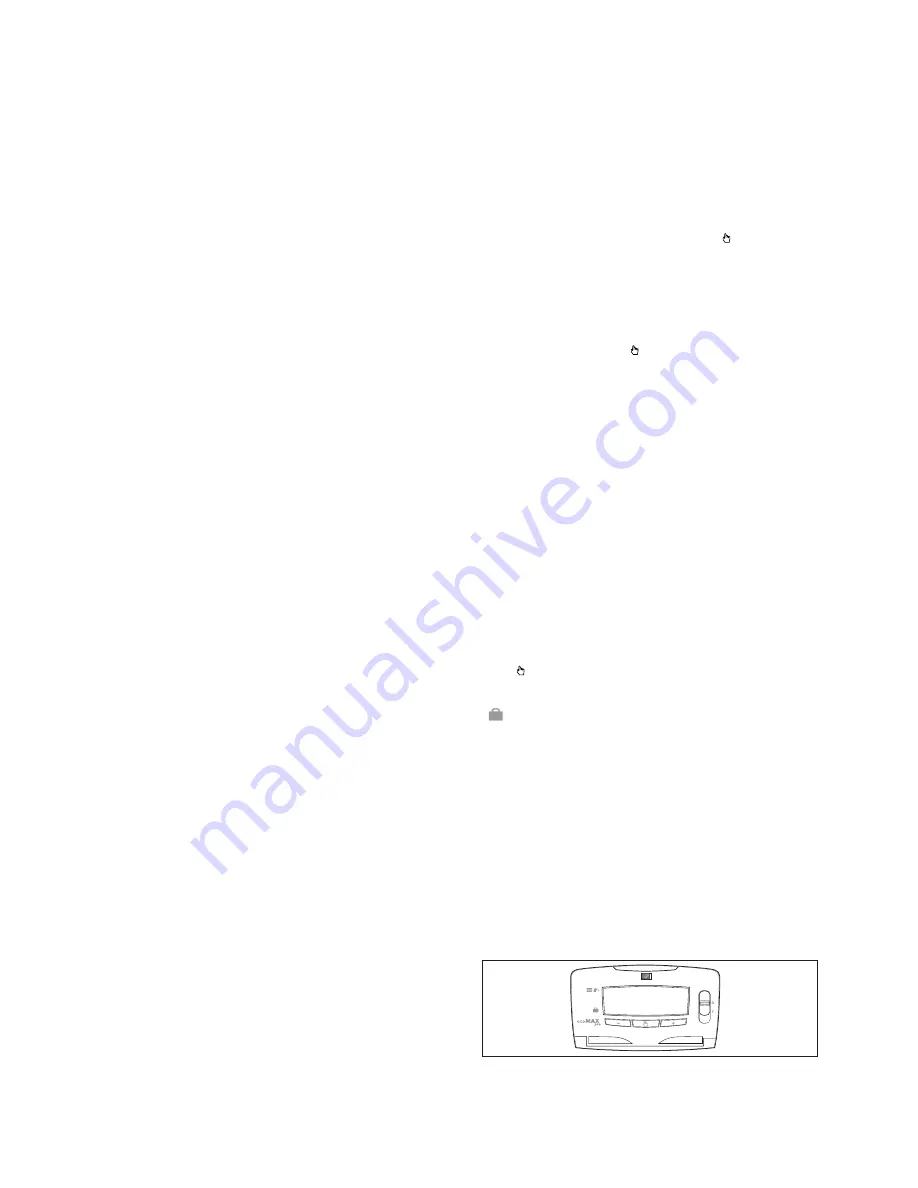
2 Important information
Operating the boiler 3
Instructions for Use, Installation and Servicing ecoMAX pro
7
3.3 User Controls
Slide the On / Off control down to the I position to turn
on the boiler. The operating indicator will illuminate
(green) to show that the boiler is on.
The temperature of the central heating water can be
adjusted by pushing the mode button (
) until the
radiator symbol is displayed. Pushing the + or - buttons
will then set the water temperature as desired. (Typical
setting temperatures for a normal radiator heating
sytem will be in the range of 60 °C to 80 °C. Note that
set temperatures below 60 °C will not sufficiently heat
any hot water cylinder). To return to the normal mode
push the mode button (
) until the display shows the
current temperature of water in the boiler.
When the boiler is operating the flame symbol will be
shown in the display. The bar symbol is also shown and
this indicates the modulating output of the boiler. The
boiler will automatically modulate to the output needed
by the heating system - the more bars that are display-
ed, the higher the output.
The ecoMAX pro is a fan flue appliance and the operati-
on of the fan may be heard when the boiler is running
and for a short period after the boiler has stopped.
Should a fault condition occur the operating indicator
will flash red and will be accompanied by an "F" symbol
in the display. To reset the boiler slide the On / Off con-
trol to the Off (O) position and after 5 seconds back to
the On (I) position. The boiler should now operate. If the
fault persists contact your installer / service provider.
The ecoMAX pro has a Holiday / frost mode. If you are
going on holiday and do not want the boiler to be opera-
ted by the external heating controls press the mode but-
ton (
) until the MODE indicator flashes in the left
hand edge of the display. Then press the + or - button
until the arrow indicator points to the holiday symbol
(
). The boiler will now only operate if necessary for
frost protection of the boiler itself as well as running a
daily pump exercise programme to prevent sticking. It
will not be turned on and off by the external heating
controls. If a system frost protection thermostat has
been fitted this will remain active.
3.4 To Turn the Boiler Off
Normally the boiler will be turned off by the heating
system controls. The mains On / Off control may be used
to switch off the boiler, however it is preferable to leave
the electrical supply on whenever possible to permit
operation of the built-in frost protection and daily pump
exercise programme.
Fig. 3.1
2.17 Guarantee
Our confidence in the quality of craftmanship and
performance of our products is demonstrated by the
Vaillant two year guarantee.
During the first year from installation the guarantee
covers your boiler against manufacturing defects for
both parts and labour. In order to extend this guarantee
to the second year from installation all you have to do is
ensure that your boiler receives a service when it is a
year old. (Please note that the cost of the service is not
included in the guarantee).
Should your boiler develop a fault please contact your
original installer or alternatively contact Vaillant Service
Solutions on 0870 6060 777.
IMPORTANT...
to qualify for your two year guarantee:
Please complete the registration details on the
guarantee card and return in the pre-paid envelope to:
Vaillant Registration Department
Freepost CV 2560
BEDWORTH
Warwickshire
CV12 8BR
The registration card must be returned within 30 days of
the boiler being installed.
The boiler must be serviced either by Vaillant Ltd. or
another competent servicing company (CORGI
registered) within one year of the installation date and
the details recorded in the "Installation, Commissioning
and Service Record Log Book" (this log book should
have been completed and left with you by your installer).
Please note that the cost of the service is not included
in the guarantee.
Vaillant is a member of the Benchmark initiative and
fully supports the aims of the programme. Benchmark
has been introduced to improve the standards of instal-
lation and commissioning of central heating systems in
the UK and to encourage the regular servicing of all cen-
tral heating systems to ensure safety and efficiency.
3 Operating the Boiler
3.1 Sealed Central Heating Systems only
CAUTION. A sealed water system must be filled and
pressurised by a competent person.
Only light the boiler when you are sure that the system
and boiler have been filled and pressurised.
The pressure should read at least 0.7 bar, when the
system is cold. If the needle displays a value below this,
follow the instructions left by your installer to refill the
system. Alternatively your installer should be called to
refill the system.
3.2 All Systems
Check that the electrical supply to the boiler is ON at
the external isolator.
Set any remote heating system controls as required.