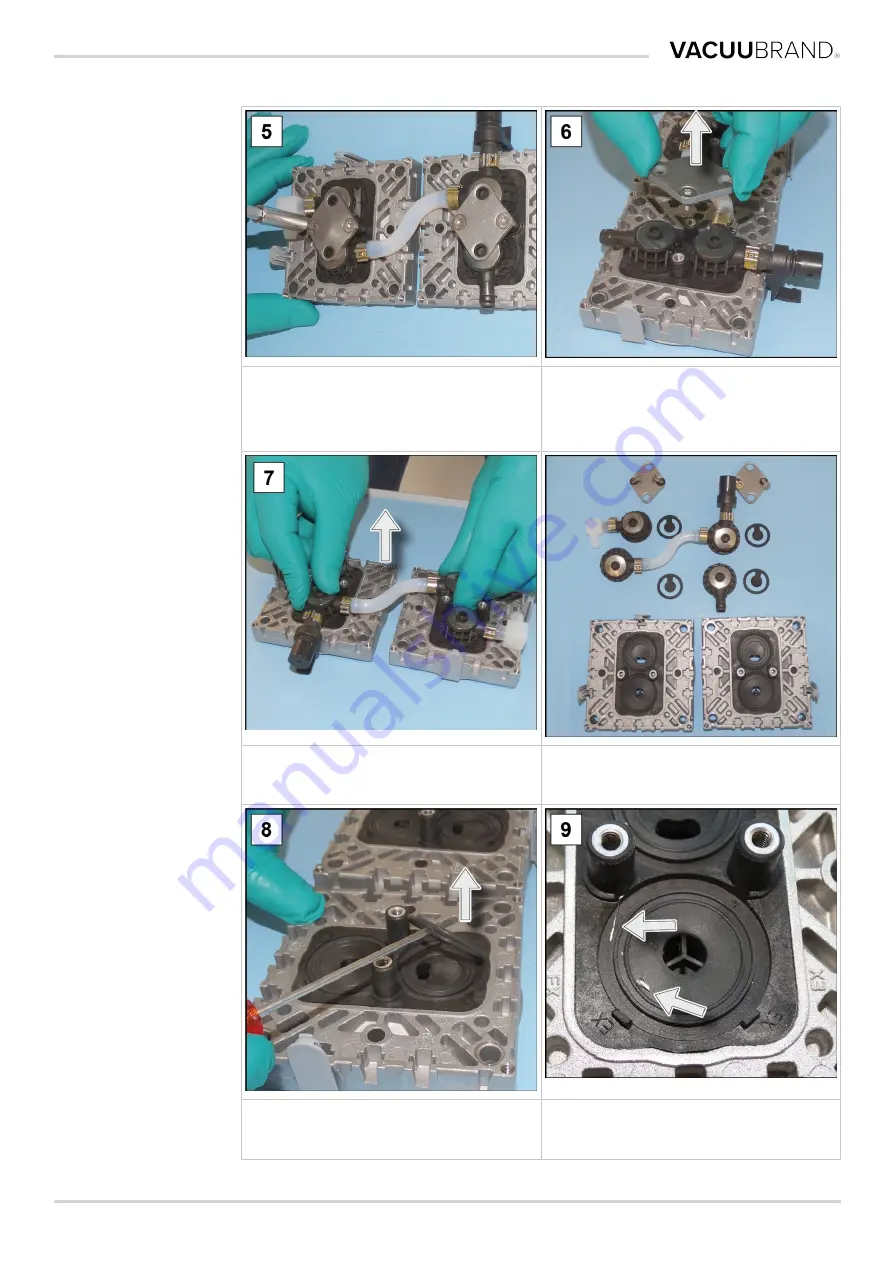
Cleaning and maintenance
68
20901334_EN-US_PC3000 VARIO select Serie_V1.4_061022
5. Undo the Torx screws on the
clamping brackets; Torx
screwdriver TX20.
6. Remove the clamping
brackets from the valve
clusters.
7. Remove the valve clusters
with the cup springs.
Top view: Components valve clusters,
valves and pump head pair.
8. Carefully remove the used
O-rings and valves.
9. Check the surfaces for soil-
ing.
Содержание PC 3002 VARIO select
Страница 82: ...Annex 82 20901334_EN US_PC3000 VARIO select Serie_V1 4_061022 8 6 EU declaration of conformity ...
Страница 83: ...Annex 20901334_EN US_PC3000 VARIO select Serie_V1 4_061022 83 8 7 UKCA conformity declaration ...
Страница 86: ...86 20901334_EN US_PC3000 VARIO select Serie_V1 4_061022 ...
Страница 87: ...20901334_EN US_PC3000 VARIO select Serie_V1 4_061022 87 ...