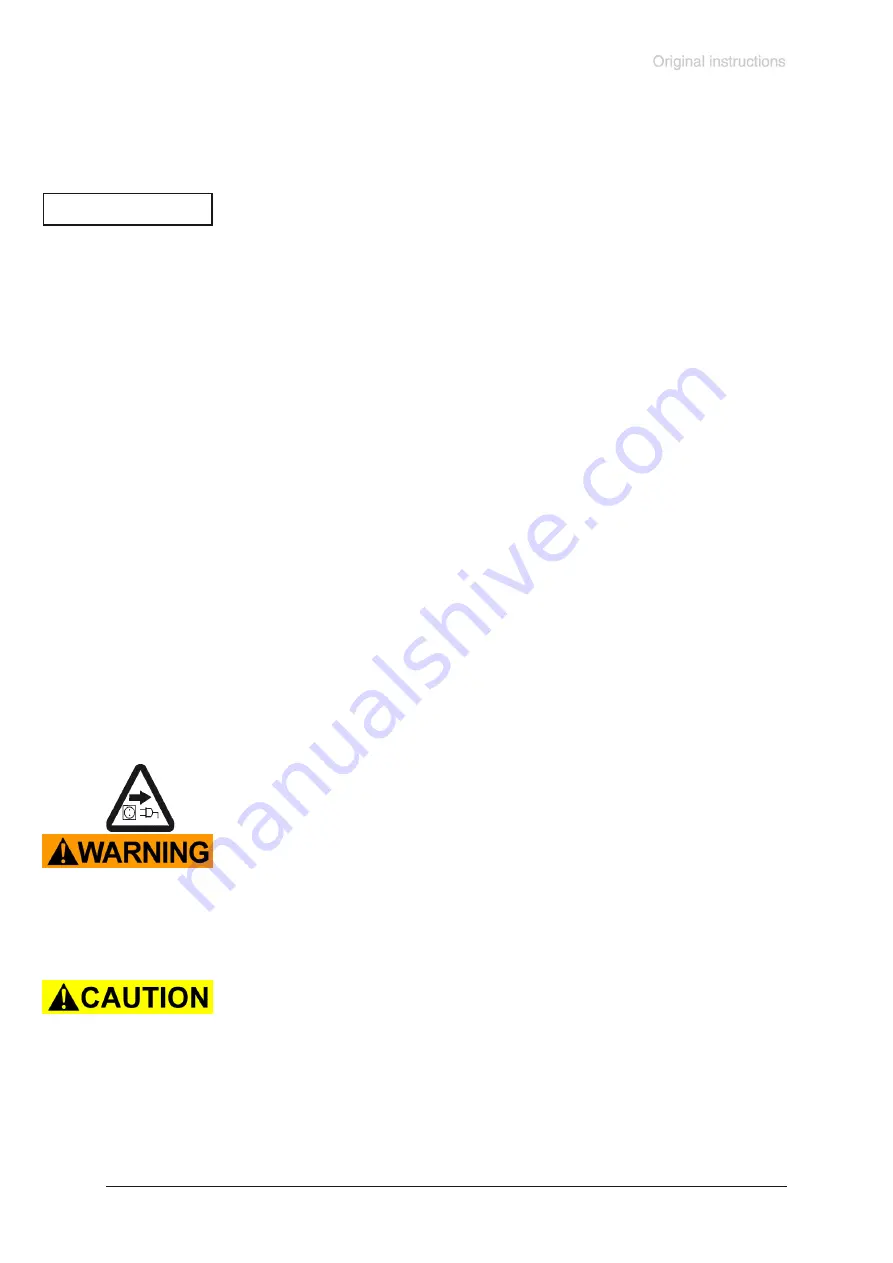
page 7 of 27
Documents are only to be used and distributed completely and unchanged. It is strictly the users´ responsibility to check carefully
the validity of this document with respect to his product. Manual-no.: 999198 / 29/09/2009
• Due to the residual
leak rate of the equipment
, there might be an exchange of
gas, albeit extremely slight, between the environment and the vacuum system.
Adopt suitable measures to prevent contamination of the pumped substances or
the environment.
Provide appropriate protective measures (i.e precautions which allow for the require-
ments of the respective application) even for the case of failure and
malfunction
.
Failure of the pump (e.g. due to power failure) or of connected components, of parts
of the supply or change of parameters must not lead to a critical dangerous situa-
tion under any circumstances. In case of diaphragm cracks or leaks in the manifold
pumped substances might be released into the environment or into the pump hous-
ing or motor. Comply especially with notes on operation and use and maintenance.
The motor is protected by a
temperature sensor at the circuit board:
Current
limitation if the temperature at the circuit board is higher than 70°C, switching off the
pump if the temperature is higher than 85°C. In case of blockade of the motor (after
10 attempts to start-up) the pump is switched off.
If the pump is switched off due to safety measures, manual reset is necessary. Isolate
the pump from mains. Eliminate the cause of failure before restarting the pump.
Do not start the pump if the pressure difference between inlet and outlet port ex-
ceeds 1.1 bar at maximum.
Prevent any backpressure of gases and the backflow of condensates.
Never suck liquids or dust into the pump.
The A-weighed emission sound pressure level of the pump does not exceed 70
dB(A). Measurement according to EN ISO 2151:2004 and EN ISO 3744:1995 with
standard silencer or exhaust tube at outlet.
Maintenance and repair
Wear parts have to be replaced regularly.
In case of normal wear the lifetime of
the diaphragms and valves is > 10000 operating hours. Bearings have a typical du-
rability of 40000 h.
➨
Isolate equipment from mains
and
wait two minutes
before starting mainte-
nance to allow the capacitors to discharge.
☞
Ensure that the pump cannot be operated accidentally. Never operate the pump
if covers or other parts of the pump are disassembled. Never operate a defective
or damaged pump.
☞
Attention
: The pump might be contaminated with process chemicals which have
been pumped during operation. Ensure that the pump is decontaminated before
maintenance and take adequate precautions to protect people from the effects of
dangerous substances if contamination has occurred.
• Before starting maintenance vent the pump, isolate the pump and other compo
-
nents from the vacuum system. Allow sufficient cooling of the pump. Drain con
-
densate, if applicable.
Ensure that
maintenance
is done only by suitably trained and supervised techni-
cians. Ensure that the maintenance technician is familiar with the safety procedures
which relate to the products processed by the pumping system.
In order to comply with law (occupational, health and safety regulations, safety at
work law and regulations for environmental protection) vacuum pumps, components
and measuring instruments returned to the manufacturer can be repaired only when
certain procedures (see section
”Notes on return to the factory”
) are followed.
NOTICE