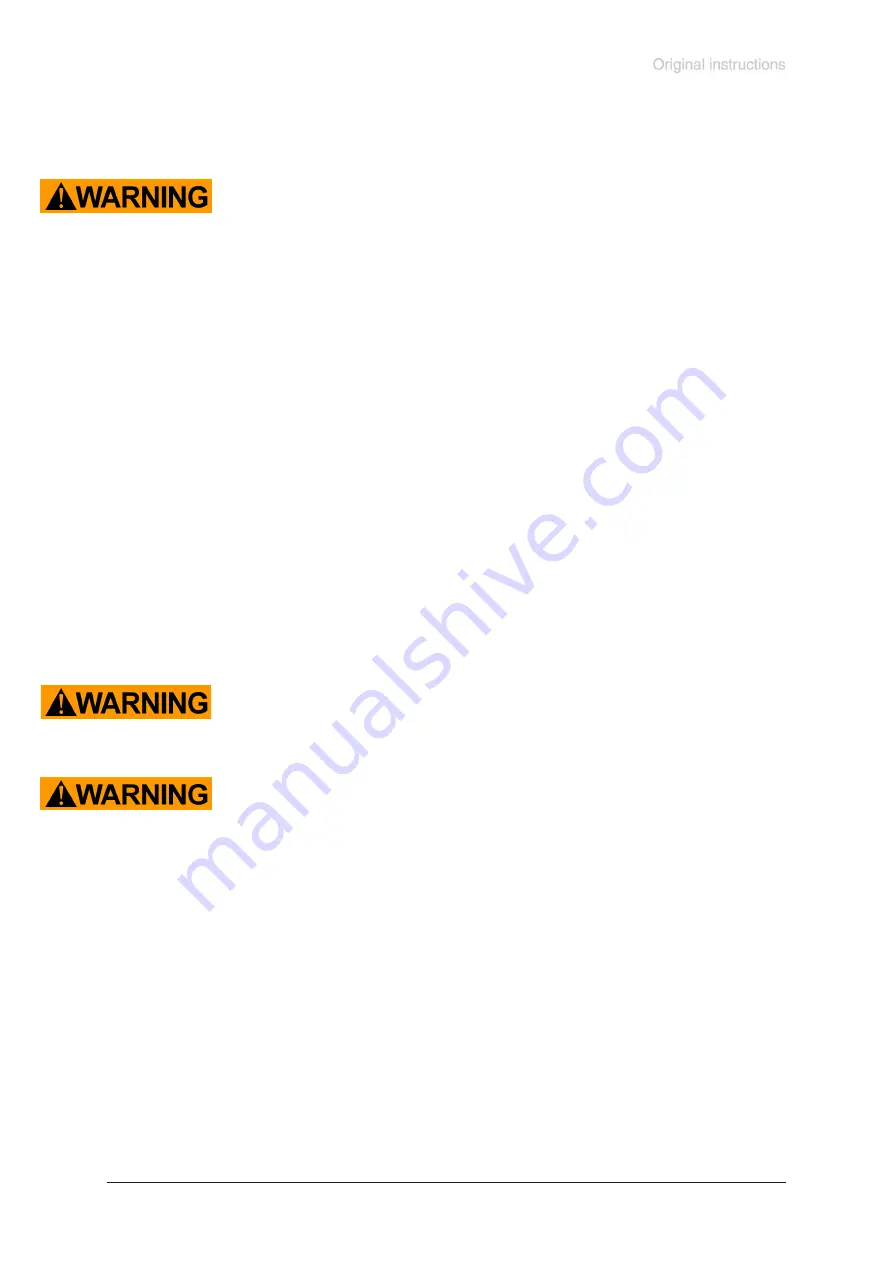
page 17 of 68
Documents are only to be used and distributed completely and unchanged. It is strictly the users´ responsibility to check carefully
the validity of this document with respect to his product. manual-no.: 999290 / 12/12/2016
The specification for category 2 for the outer part of the pump is only val
-
id when purging the crankcase with inert gas. Without inert gas purging the
pump has the specification II 3G IIB T4 X for the outer part.
☞
Adopt suitable measures to prevent the release of dangerous, explosive, corro-
sive or polluting fluids.
☞
If pumping
different substances
, it is recommended to purge the pump with air
or inert gas prior to changing the pumped media in order to pump out residues
and to avoid reactions of the pumped substances with each other and with the
pump materials.
Take into consideration interactions and chemical reactions of the pumped
media.
☞
Ensure that the materials of the wetted parts are compatible with the pumped
substances, see section ”Technical data”.
☞
The v
alves and the diaphragms
are wear parts.
Replace the diaphragms and
valves at the latest at 90% of the typical lifetime or immediately at higher
noise level.
The typical lifetime of a diaphragm is 15000 operation hours when
pumping non-corrosive or non-condensable gases, if necessary provide an op-
eration time counter.
☞
Check the
overpressure safety valve between the pump stages
(only pumps
with four cylinders) regularly and replace a
t the latest at 90% of the typical life-
time
(typical lifetime: 15000 operation hours).
☞
Take adequate precautions to protect people from the effects of dangerous sub-
stances (chemicals, thermal decomposition products of fluoroelastomers), wear
appropriate safety-clothing and safety glasses.
☞
Obey applicable regulations when disposing of chemicals. Take into considera-
tion that chemicals may be polluted.
☞
Adopt suitable measures to prevent contamination of the pumped substances or
the environment.
Electronic equipment is never 100% fail-safe. This may lead to an indefinite status of
the equipment. Provide protective measures against malfunction and failure.
☞
Operating the pump, stand still of the pump or operating the air admittance valve
must not lead to a critical dangerous situation under any circumstances.
Ensure that in case of failure the pump and the vacuum system always will turn into
a safe status.
☞
In case of leaks in the manifold or diaphragm cracks pumped substances might
be released into the environment or into the pump housing. To reduce the risk of
leaks, ask for a diaphragm pump with additional safety diaphragm.
☞
Obey especially notes on operation and use and maintenance.
☞
Failure of the pump (e. g. by power failure) or connected components, parts of
the supply (e. g. coolant) or change of parameters (e. g. increase of pressure
in the coolant system) must not lead to a critical dangerous situation under any
circumstances.