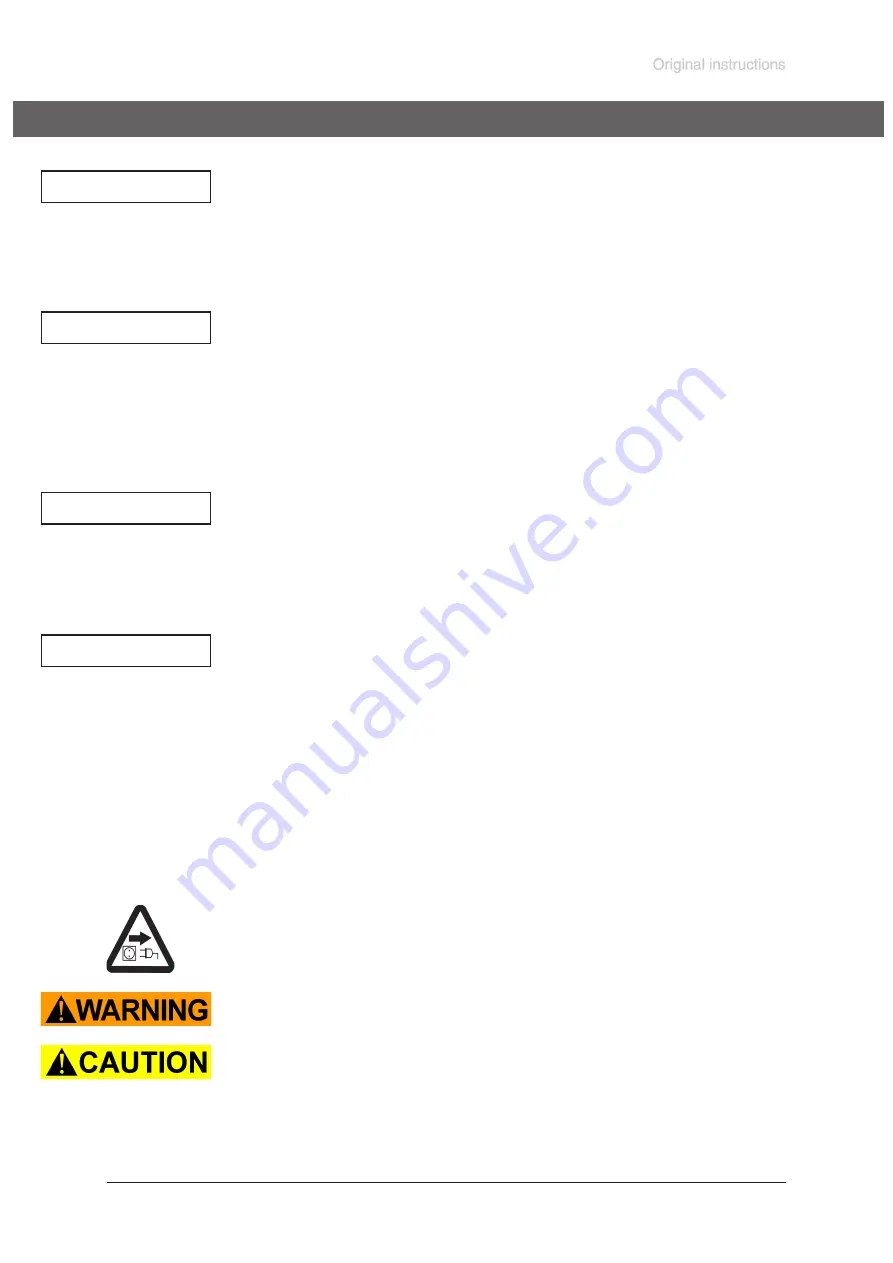
page 39 of 68
Documents are only to be used and distributed completely and unchanged. It is strictly the users´ responsibility to check carefully
the validity of this document with respect to his product. manual-no.: 999290 / 12/12/2016
Maintenance of the pump must be performed only by a suitable trained and
supervised personnel.
All bearings are encapsulated and are filled with long-life lubricant and run under
normal operating conditions maintenance free. Replacement of the bearing must be
performed at the latest at 90% of the nominal lifetime of the bearing (nominal life-
time of the bearing: 40000 operation hours, if necessary provide an operation time
counter). If the noise level is enhanced switch off the pump immediately and inspect.
Replacement of the bearing must only performed at the factory. Never operate a
defective pump.
The valves and the diaphragms are wear parts. Replace the diaphragms at the lat-
est at 90% of the typical lifetime or immediately at higher noise level. The typical
lifetime of a diaphragm is 15000 operation hours when pumping non-corrosive or
non-condensable gases, if necessary provide an operation time counter.
Pumping condensable media, operation at high temperature, great gas flow or
deposits reduce the lifetime of a diaphragm significantly. Therefore check the dia
-
phragm regularly for faultless condition.
☞
Prevent internal condensation, transfer of liquids or dust. The diaphragm and
valves will be damaged, if liquids are pumped in significant amount.
To control the faultless function of the diaphragm install a gas specific detector at the
outlet of the inert gas flush. A signal from the detector indicates a diaphragm crack.
Switch off the pump immediately and check diaphragms.
If the rated ultimate vacuum is no longer achieved, the pump interior, the hose con-
nections, the diaphragms and the valves must be cleaned and the diaphragms and
valves must be checked for cracks or other damage. Replace defective parts im-
mediately.
Inspect the fittings of the pump regularly, the maximum permitted leak rate is 0.1
mbar l / s.
When replacing diaphragms and valves check the overpressure safety valve at the
outlet of the pump.
Remove possible deposits in the crank chamber of the pump when replacing dia-
phragms and valves.
If the pump is exposed to corrosive gases or gases and vapours which may form de-
posits (e. g. crystallisation) or deposits due to pumped particles, maintenance should
be carried out frequently (according to the experience of the user).
☞
Regular maintenance will improve the lifetime of the pump and also protect both
man and environment.
Before starting maintenance vent the system, isolate the pump and other compo-
nents from the vacuum system and the electrical supply. Drain condensate if ap-
plicable, avoid the release of pollutants. Allow sufficient cooling of the pump. Before
starting maintenance, wait two minutes after isolating the equipment from mains to
allow the capacitors to discharge.
Never operate the pump if covers or other parts of the pump are disassembled. En-
sure that the pump cannot be operated accidentally. Never operate a defective or
damaged pump.
Ensure that the maintenance technician is familiar with the safety procedures which
relate to the products processed by the pumping system.
Replacing diaphragms and valves
NOTICE
NOTICE
NOTICE
NOTICE