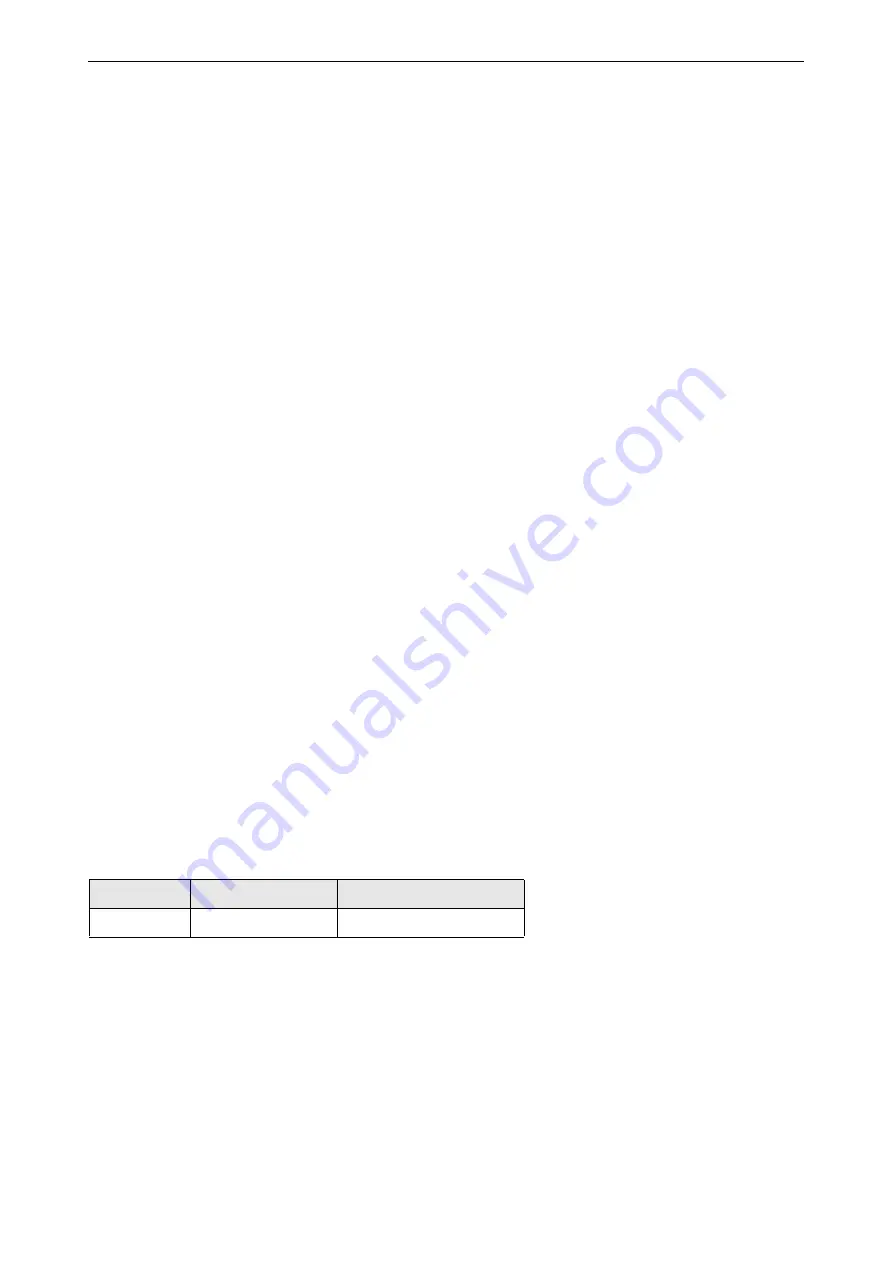
STO AND SS1 SAFETY FUNCTIONS
vacon • 33
Local contacts: https://www.danfoss.com/en/contact-us/contacts-list/
NOTE!
See manufacturer user manual for more information regarding the setting of the time delay.
Safe Stop 1 safety function requires that the drive is configured according to the following guide-
lines:
•
Deceleration time must be set according to the machine or process requirement
•
The drive stop function must be programmed to "stop by ramp"
•
A dedicated digital stop input must be used (not combined with start command) for the drive
stop command
See the previous chapter for parametrizing the drive for Safe Torque Off (STO) safety function.
NOTE!
The drive will indicate Safe Torque Off (STO) state when Safe Stop 1 time delay has expired
NOTE!
If the time delay (of the external safety relay component) is NOT set correctly (time delay set
shorter than the required deceleration time of the process/machine), the motor will stop by coas-
ting when the time delay expires.
3.5.6
Testing the Safe Torque Off (STO) or Safe Stop 1 (SS1) safety func-
tions
NOTE!
After connecting the board ALWAYS make sure that the STO or SS1 safety functions are
working properly by testing them before operating the system.
NOTE!
Before testing the STO or SS1 safety functions, make sure that the checklist (Table 7) is in-
spected and completed.
NOTE!
Concerning the SS1 safety function,
make sure by testing
that the drive's
stop by ramp func-
tion
is working
in accordance with the process requirements
.
When the STO safety function is activated, a code: A30 "SafeTorqueOff " appears on the control key-
pad display. This indicates that the STO safety function is active. After STO has been deactivated, the
warning remains active for 10 seconds.
3.5.7
Determining the drive STO level
Depending on the drive configuration, the STO implementation can be either SIL 2 or SIL 3. The
safety level can be seen on drive panel, see Table 8.
Another way to determine the safety levels is the revision of the used PCBs. Small drives (up to FR8)
are dependent on the control board, VB00761, revision: the configuration is SIL 3 starting from re-
vision G. See chapter 2.2 for details on determining the board revision.
Larger drives (FR9 and above) also depend on the power unit. For these configurations see the mon-
itor value that is described above.
Table 8. Safety level
Code
Monitor value
Possible values
V7.2.2.2
Safety Levels
SIL2 + PLd, SIL3 + PLe
Содержание OPTAF
Страница 1: ...vacon nx ac drives optaf sto and atex option board user manual ...
Страница 2: ......
Страница 8: ...vacon 6 GENERAL Local contacts https www danfoss com en contact us contacts list ...
Страница 9: ...GENERAL vacon 7 Local contacts https www danfoss com en contact us contacts list ...
Страница 10: ...vacon 8 GENERAL Local contacts https www danfoss com en contact us contacts list ...
Страница 11: ...GENERAL vacon 9 Local contacts https www danfoss com en contact us contacts list ...
Страница 12: ...vacon 10 GENERAL Local contacts https www danfoss com en contact us contacts list ...