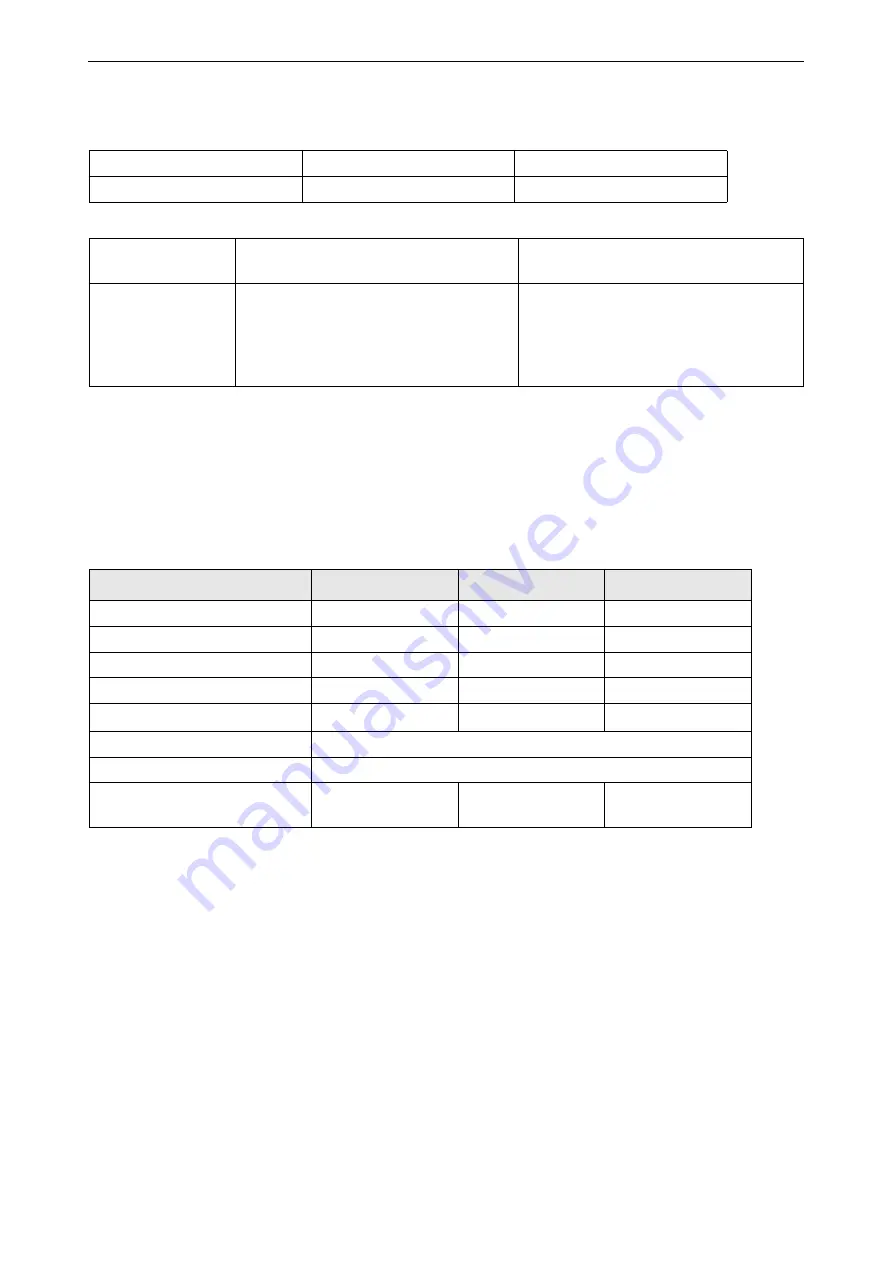
STO AND SS1 SAFETY FUNCTIONS
vacon • 19
Local contacts: https://www.danfoss.com/en/contact-us/contacts-list/
3.3
Technical details
3.3.1
Response times
3.3.2
Input voltage levels
Reversed polarity applied on STO input terminals does not cause disabling of STO function. The op-
eration of OPTAF is not interfered by test pulses that are generated to the STO lines by the connect-
ed safety actuator as long as the test pulses fulfill certain requirements. See chapters 3.3.3 and
3.3.4 for details.
3.3.3
External dark test pulse filtering capability
To recognize the short circuits from STO lines to power supplies or ground, some safety PLCs test
their outputs by pulsing the output from high to low level for short periods of time when STO is dis-
abled. The pulses are known as 'dark test pulses'. To prevent these test pulses from causing false
fault indications, these dark test pulses are filtered out by STO inputs on OPTBJ. If the input voltage-
specific values for dark test pulse durations are exceeded, the drive may indicate STO diagnostics
fault or STO may be activated. The used dark test pulse duration should always be shorter than the
specified minimum pulse withstanding duration. Limits for the test pulse duration, frequency and
period are given in Table 3. The filtering time is hardware-based and cannot be adjusted. External
dark test pulse filtering is included on VB00761 boards from revision J onwards. See Chapter 2.2
for identifying the board revision.
Safety function
Activation time
De-activation time
Safe Torque Off
< 20 ms
1000 ms
Safety Function
Delay from stop signal at safety relay
input until activation of ramp stop
Time delay for Safe Torque Off (STO)
activation
Safe Stop 1 (SS1)
Safety relay delay + typ. 20 ms
(drive)
NOTE!
Drive application software
dependent. Refer to the user manual
of the application in use.
System process dependent. User set-
table through the safety relay timer.
Table 2. Safe input data
Technical item or function
Minimum
Typical
Maximum
Input Voltage (logic 1)
11 V
24 V
30 V
Input Voltage (logic 0)
-3 V
0 V
3 V
Input Current (logic 1)
4 mA
10 mA
14 mA
Input Current (logic 0)
-1 mA
1 mA
Input Resistance
2.5 k
Ω
Galvanic Isolation
Yes
Short-circuit Protected
Yes
Allowed discrepancy time of
physical inputs
5 s
Содержание OPTAF
Страница 1: ...vacon nx ac drives optaf sto and atex option board user manual ...
Страница 2: ......
Страница 8: ...vacon 6 GENERAL Local contacts https www danfoss com en contact us contacts list ...
Страница 9: ...GENERAL vacon 7 Local contacts https www danfoss com en contact us contacts list ...
Страница 10: ...vacon 8 GENERAL Local contacts https www danfoss com en contact us contacts list ...
Страница 11: ...GENERAL vacon 9 Local contacts https www danfoss com en contact us contacts list ...
Страница 12: ...vacon 10 GENERAL Local contacts https www danfoss com en contact us contacts list ...