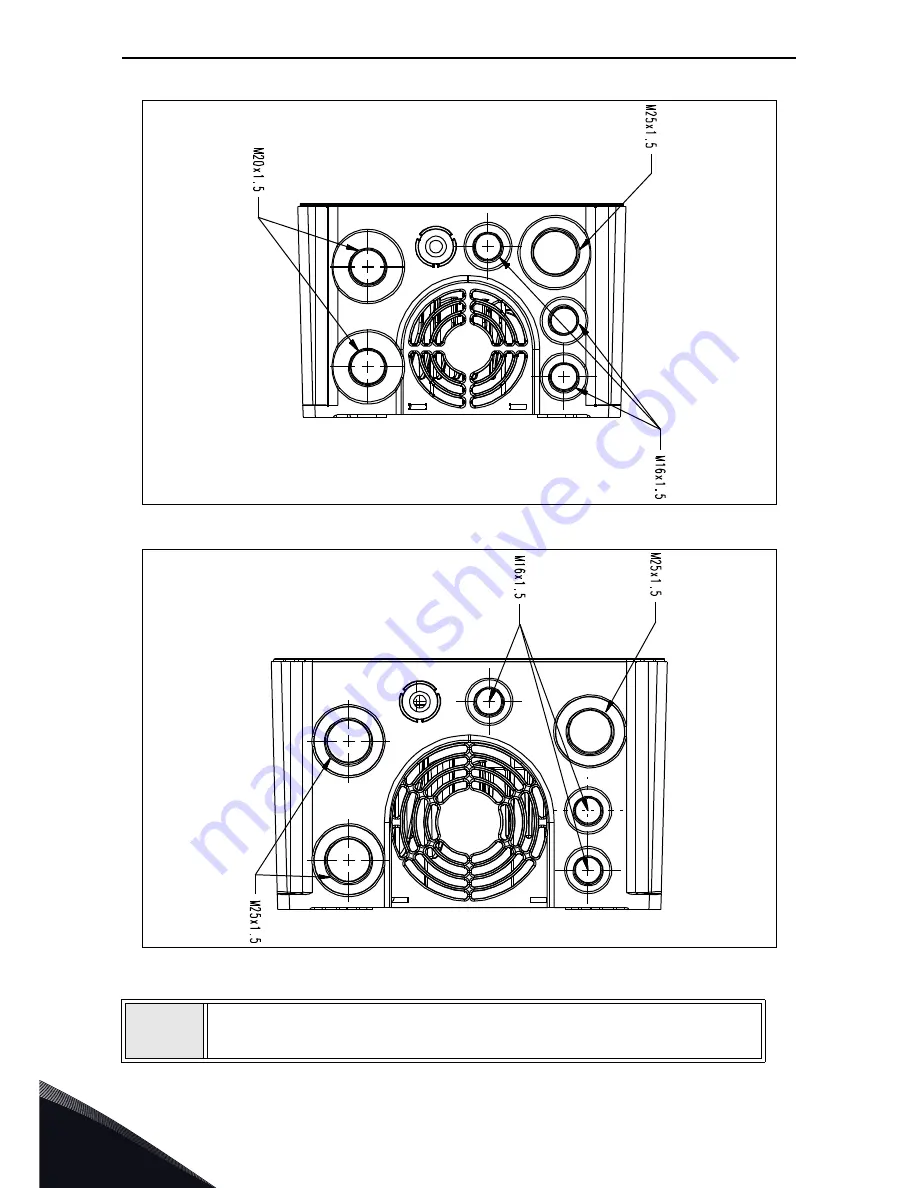
4
vacon • 36
Power cabling
Local contacts: http://drives.danfoss.com/danfoss-drives/local-contacts/
Figure 23.Cable entries, MU2.
Figure 24. Cable entries, MU3.
5
•
Cable glands must be made of plastic materials. They are used for sealing
cables passing through cable entries to ensure the characteristics of the
enclosure.