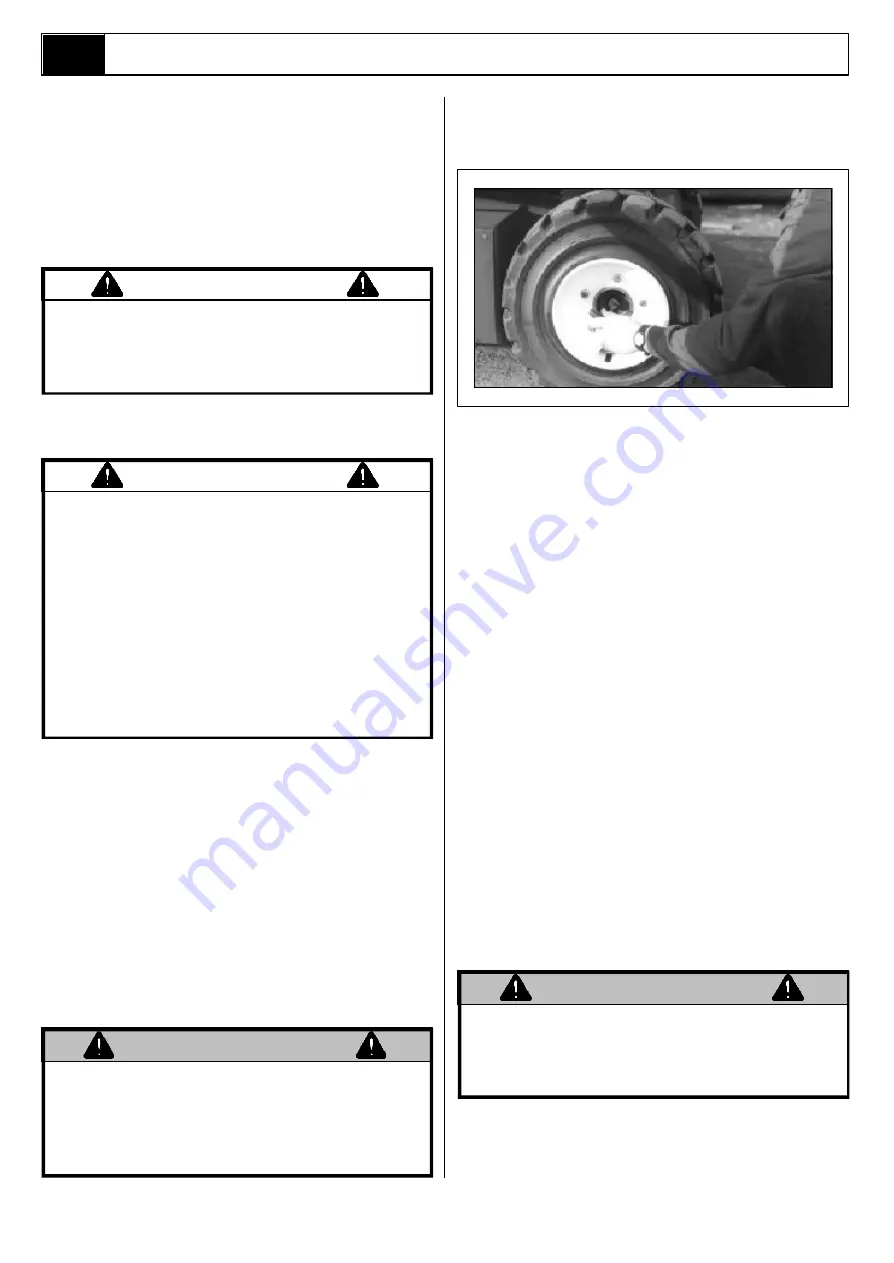
Machine Preparation
Section
2-2
AB38 Work Platform
WARNING
2.7 Storage
No preparation is required for storage when the Work
Platform is in regular use. Regular maintenance per
Table 4-1
should be performed.
If the work platform is to be placed in long term
storage (dead storage) use the following preservation
procedure.
PRESERVATION
1.
Clean painted surfaces. If the painted surface is
damaged, repaint.
2.
Fill the hydraulic tank to operating level
with the
platform fully lowered.
Fluid should be visible
on the Dip Stick. It is not recommended that the
hydraulic fluid be drained.
3.
Coat exposed portions of cylinder rods with a
preservative such as multipurpose grease and
wrap with barrier material.
4.
Coat all exposed unpainted metal surfaces with
preservative.
BATTERIES
1.
Disconnect the batteries.
2.
Disconnect the battery leads and secure to the
chassis.
Care should be taken, while disconnecting the
battery leads, that a short circuit does not occur.
i.e. grounding to the chassis with a spanner.
3.
Remove the batteries and place in alternate
service. Battery efficiencies are best realised
when used consistently.
2.6
When the AB38 is on the Truck it should then be
made secure.
1.
Chock the wheels of the AB38.
2.
Secure the work platform to the transport
vehicle with chains or straps of adequate load
capacity attached to the lifting lugs on the
chassis.
Overtightening of the chains or straps through
tie down lugs may result in damage to the
Work Platform.
CAUTION
2.6 Manual Brake Release
Preform this operation only when the machine
will not operate under its own power and it is
necessary to move the machine, or for
winching onto a trailer for transportation.
Ensure the machine is on level ground before
commencing this operation and use wheel
chocks as appropriate to prevent the machine
from rolling inadvertently.
Do not exceed 3 mph. Faster speeds will
damage drive components and void warranty.
1.
Ensure that the Platform is fully lowered and
that the Elevating Assembly is slewed (rotated)
such that the platform is stowed above the drive
wheels. Turn the Upper Control Box to the
OFF
position and remove the key.
2.
Attach a chain/cable of sufficient capacity for
towing the machine to the front or rear lifting/tie
down lugs. Take up the slack in the chain/cable.
3.
Locate the Allen head socket screws located in
the centre of the two drive (rear) wheels and
using a 6 mm Allen key, turn each one
clockwise to its full extent. The machine is now
in freewheel mode.
DO NOT leave the machine unattended or
attempt to operate the AB38 Work Platform
until the Brake Release Screws have been
re-engaged.
CAUTION
4.
When towing is completed, turn both Allen head
socket screws in a counter clockwise direction
until they rest firmly against the locking circlip.
Figure 2-2 : Manual Brake Release
WARNING
Содержание AB38
Страница 2: ...ii AB38 Work Platform NOTES...
Страница 4: ...ii AB38 Work Platform NOTES...
Страница 6: ...iv AB38 Work Platform NOTES Foreword...
Страница 10: ...Contents Section IV AB38 Work Platform i NOTES...
Страница 14: ...Introduction Specifications Section 1 4 AB38 Work Platform NOTES 1 3...
Страница 17: ...Machine Preparation Section 2 3 AB38 Work Platform NOTES 2 7...
Страница 18: ...Machine Preparation Section 2 4 AB38 Work Platform 2 7 NOTES...
Страница 29: ...Operation Section 3 11 AB38 Work Platform NOTES 3 5...
Страница 30: ...Operation Section 3 12 AB38 Work Platform NOTES 3 5...
Страница 59: ...Maintenance Section 4 29 AB38 Work Platform NOTES 4 21...
Страница 60: ...Maintenance Section 4 30 AB38 Work Platform NOTES 4 21...
Страница 66: ...Troubleshooting Section 5 6 AB38 Work Platform 5 7 NOTES...
Страница 68: ...Schematics Section 6 2 AB38 Work Platform NOTES 6 0...
Страница 71: ...Schematics Section 6 5 AB38 Work Platform 6 1 6 1 Electrical Schematics J1 Harness Connections TOP VIEW...
Страница 72: ...Schematics Section 6 6 AB38 Work Platform 6 1 NOTES...
Страница 73: ...Electrical Schematic Schematics 6 7 AB38 Work Platform Section 6 1...
Страница 74: ...Electrical Schematic Schematics 6 8 AB38 Work Platform Section 6 1 TOP VIEW...
Страница 76: ...Schematics Section 6 10 AB38 Work Platform NOTES 6 2...
Страница 78: ...Section 6 2 6 12 AB38 Work Platform Schematics NOTES...
Страница 81: ...Illustrated Parts Breakdown Section 7 3 AB38 Work Platform 7 2...
Страница 83: ...Illustrated Parts Breakdown Section 7 5 AB38 Work Platform 7 2...
Страница 85: ...Illustrated Parts Breakdown Section 7 7 AB38 Work Platform 7 2...
Страница 87: ...Illustrated Parts Breakdown Section 7 9 AB38 Work Platform 7 2...
Страница 89: ...Illustrated Parts Breakdown Section 7 11 AB38 Work Platform 7 2 22...
Страница 91: ...Illustrated Parts Breakdown Section 7 13 AB38 Work Platform 7 2...
Страница 93: ...Illustrated Parts Breakdown Section 7 15 AB38 Work Platform 7 2...
Страница 95: ...Illustrated Parts Breakdown Section 7 17 AB38 Work Platform 7 2...
Страница 97: ...Illustrated Parts Breakdown Section 7 19 AB38 Work Platform 7 2...
Страница 99: ...Illustrated Parts Breakdown Section 7 21 AB38 Work Platform 7 2...
Страница 101: ...Illustrated Parts Breakdown Section 7 23 AB38 Work Platform 7 2...
Страница 103: ...Illustrated Parts Breakdown Section 7 25 AB38 Work Platform 7 2...
Страница 105: ...Illustrated Parts Breakdown Section 7 27 AB38 Work Platform 7 2...
Страница 107: ...Illustrated Parts Breakdown Section 7 29 AB38 Work Platform 7 2...
Страница 109: ...Illustrated Parts Breakdown Section 7 31 AB38 Work Platform 7 2...
Страница 111: ...Illustrated Parts Breakdown Section 7 33 AB38 Work Platform 7 2...
Страница 113: ...Illustrated Parts Breakdown Section 7 35 AB38 Work Platform 7 2...
Страница 115: ...Illustrated Parts Breakdown Section 7 37 AB38 Work Platform 7 2...
Страница 117: ...Illustrated Parts Breakdown Section 7 39 AB38 Work Platform 7 2...
Страница 119: ...Illustrated Parts Breakdown Section 7 41 AB38 Work Platform 7 2 8 9...
Страница 121: ...Illustrated Parts Breakdown Section 7 43 AB38 Work Platform 7 2...
Страница 123: ...Illustrated Parts Breakdown Section 7 45 AB38 Work Platform 7 2...
Страница 125: ...Illustrated Parts Breakdown Section 7 47 AB38 Work Platform 7 2...
Страница 127: ...Illustrated Parts Breakdown Section 7 49 AB38 Work Platform 7 2...
Страница 131: ...Illustrated Parts Breakdown Section 7 53 AB38 Work Platform 7 2 NOTES...
Страница 133: ...Technician s Print AB38 Work Platform Electrical Schematic...