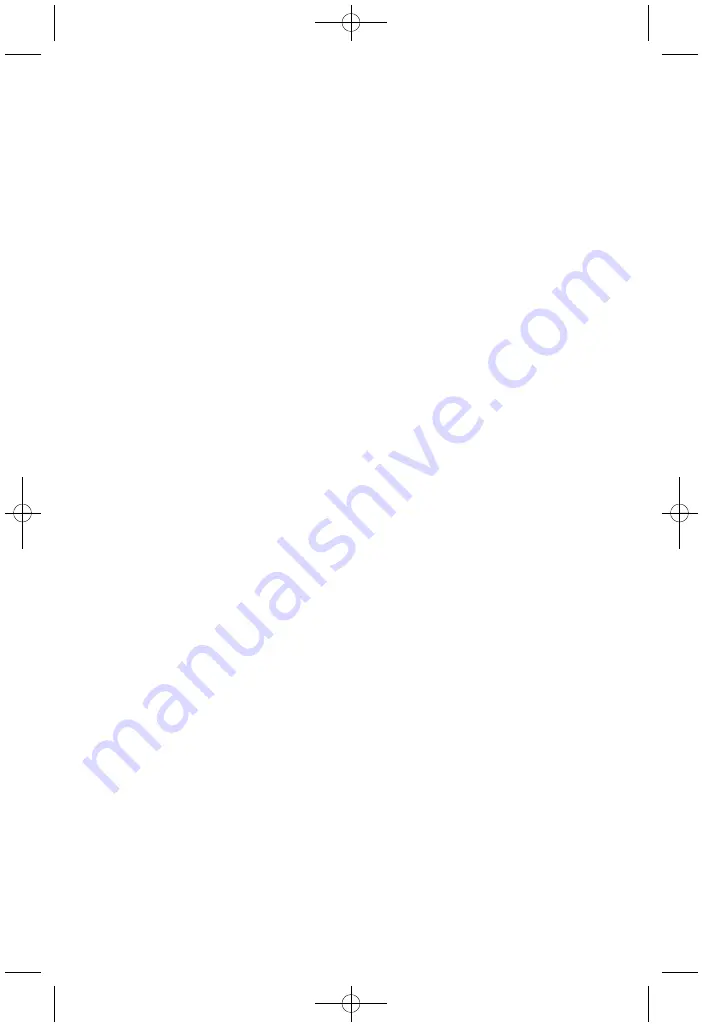
Fluid Level
Level the gage by adjusting the two front lev-
eling screws (Item 8 on drawing) until the bub-
ble in the spirit level is centered in the small
circle. After leveling the gage, open both rapid
shut-off valve tube connectors (Items 2 and
5). Back off the micrometer (Item 4), if neces-
sary, to make sure that the point is not
immersed in the gage fluid. The fluid level in
the gage should now coincide with the mark
on the right hand bore (Item 6) plus or minus
approximately 1/32 inch. If the level of fluid is
too high, fluid can be removed with an eye
dropper pipette or carefully poured out of the
right connection (Item 5).
If the level is too low, remove the top left rapid
shut-off valve tube connector (Item 2) and
add distilled water pre-mixed with the proper
amount of green concentrate. (See mainte-
nance instructions for proportions. After cor-
recting the fluid level, re-install the rapid shut-
off connectors and, with these in the open
position, re-level the Microtector
®
Gage. The
gage is now ready to be zeroed.
Zeroing
Turn the Micrometer barrel (Item 4) until its
lower end just coincides with the zero mark
on the scale and the zero on the barrel scale
coincides with the vertical line on the internal
scale. Note that the internal scale is graduat-
ed every .025˝ from 0 to 1.00 inch and the
barrel scale is graduated in one thousandths
from 0 to .025˝. Turn the meter circuit switch
at the top of gage to the “on” position. While
holding the barrel at the zero position (and
with gage level), raise or lower the point by
turning the knurled knob (Item 3) until the
point is above, but near, the fluid.
Check to be sure that the meter registers
zero. Watch the meter, hold the barrel, and
lower the point slowly by turning the top
knurled knob. As the knob is turned, the point
will contact the fluid and the meter pointer will
move from zero to some upscale position.
After making contact, turn the point out of the
fluid by turning the micrometer barrel counter-
clockwise to a reading of .010 or more. Again,
watch the meter and, this time, lower the
point by turning the micrometer barrel. The
point position where the meter pointer begins
to move up scale is the zero position. This
position should correspond to the zero read-
ing on the micrometer. Adjust the point in rela-
tion to the micrometer barrel by turning the
top knob while holding the barrel steady.
Repeat lowering the point, watching the
meter for contact, and adjusting the point
until the zero position and zero reading exact-
ly coincide. The gage is now zeroed and
should not be moved.
An alternative method of zeroing and reading
can be used wherein, instead of zeroing the
gage completely, a zero correction reading is
taken and recorded, then subtracted from the
final reading. Comparable results can be
obtained with either method.
Positive Pressure Measurement
With the fluid at its proper level, a pressure of
2.0˝ water column maximum can be meas-
ured. Positive pressure should be applied to
the top left connection (Item 2) with the
micrometer zeroed as described above. This
will permit a simple direct reading to be taken.
After an unknown pressure has been applied
at the top left connection, the fluid level will
drop in the left bore and rise over the point in
the right bore. Note that the indicating meter
point has moved upscale because the point is
immersed in the fluid. Turn the micrometer
counter-clockwise until the point leaves the
fluid as indicated by the meter pointer drop-
ping to zero on its scale. Then slowly turn the
micrometer down until its point just touches
the fluid surface, causing movement of the
meter pointer. Withdraw the point and repeat
several times, noting each time the microme-
ter reading where the meter pointer begins.
The average of these readings multiplied by
two is the pressure applied to the gage. (Avg.
reading x 2 = pressure applied in inches w.c.
The degree of uncertainty for the operator is
indicated by the difference in these readings.
3
D-57:D-57 7/10/09 10:39 AM Page 3
Содержание KP5522-P
Страница 11: ...Project 22 753 Model KP5522 Page 10 Appliance Front Appliance Left...
Страница 12: ...Project 22 753 Model KP5522 Page 11 Appliance Right Appliance Rear...
Страница 14: ...Project 22 753 Model KP5522 Page 13 Pellet Fuel Analysis...
Страница 17: ...Project 22 753 Model KP5522 Page 16 Sealed Unit...
Страница 19: ...Appendix A...
Страница 66: ...Project 22 751 Model Charnwood Skye E700 Page 16 Tunnel Schematic...
Страница 100: ......
Страница 101: ......
Страница 102: ......
Страница 103: ...Appendix B...
Страница 127: ...2022 United States Stove Company 23 NOTES...
Страница 128: ...24 2022 United States Stove Company NOTES...
Страница 129: ...2022 United States Stove Company 25 NOTES...
Страница 160: ......
Страница 161: ......
Страница 162: ......
Страница 163: ...Appendix C...
Страница 171: ......
Страница 172: ......
Страница 174: ......
Страница 175: ......
Страница 181: ......
Страница 182: ......
Страница 189: ...Appendix E...
Страница 192: ...1 1 2 2 3 3 4 4 A A B B A B C...