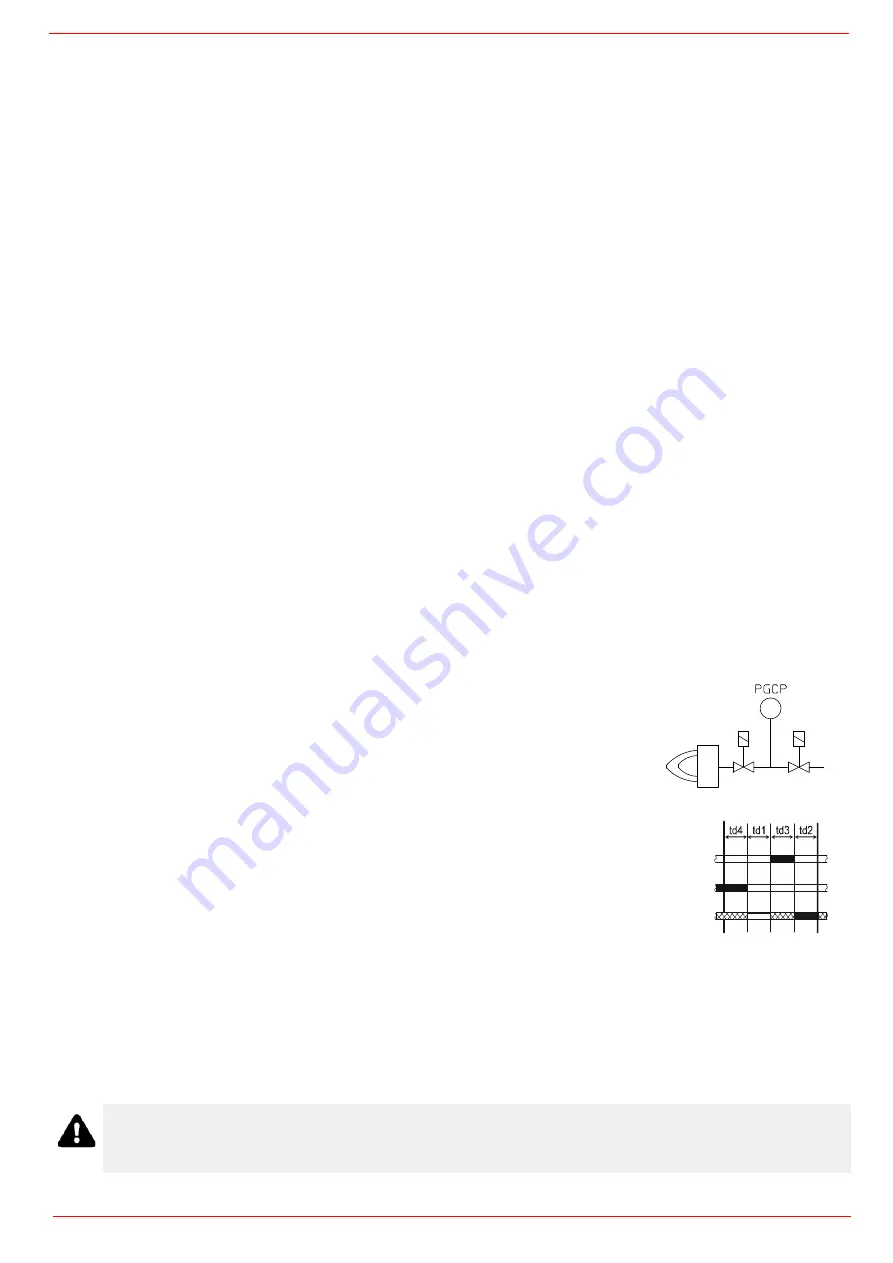
PART III: OPERATION
28
Fuel selection:
In order to start the burner with gas or light oil, the operator must commute the selector on the burner control panel on (1) = gas, or
(2) = light oil.
If the selector is set on (1) the gas cock must be open, while the light oil cock must be closed. Viceversa if the selector is set on (2).
CAUTION:
if the fuel chosen is oil, be sure the cutoff valves on the feed and return pipes are open.
Check the control box is not locked; if so, reset it by means of the button on LMV panel.
Check the series of thermostats and pressure switches turn the burner to on.
Gas operation
At the beginning of the start-up cycle, the actuator drives the air damper to the maximum opening position, then the fan motor
starts up: the pre-purge phase begins.
At the end of the pre-purge, the air damper is driven to the ignition position, the ignition transformer is energised (signalled by the
light
B4
on the front panel) then, few seconds later, the EV1 and EV2 gas valves are energised (light G1 and G2 on the front
panel).
Few seconds after the gas valves opening, the ignition transformer is de-energised and light
B4
turns to off.
The burner operates in the low flame stage; few seconds later the two-stages operation begins and the burner output increases or
decreases, driven by the external thermostats (progressive burners) or by the modulator (fully-modulating burners).
Light oil operation
The fan motor starts and the pre-purge phase as well. Since the pre-purge phase must be carried out at the maximum air rate, the
control box drives the actuator opening and when the maximum opening position is reached, the pre-purge time counting starts.
At the end of the pre-purge time, the actuator is in the light oil ignition position: the ignition transformer is energised (lamp
B4
on);
the ignitor gas valves and the light oil valves open. Few seconds after the valves opening, the transformer is de-energised and
lamp
B4
turns off.
The burner is now operating, meanwhile the actuator goes to the high flame position; after some seconds, the two-stage operation
begins; the burner is driven automatically to high flame or low flame, according to the plant requirements.Operation in high or low
flame is signalled by LED
B2
on the burner control panel.
The fuel is pushed into the pump to the nozzle at the delivery pressure set by the pressure governor. The solenoid valve stops the fuel
immission into the combustion chamber. The fuel flow rate that is not burnt goes back to the tank through the return circuit. The nozzle
is feeded at constant pressure, while the return line pressure is adjusted by means of the pressure governor controlled by an actuator..
Integrated proving system (burners equipped with LME7x, LMV, LDU)
AIR FLOW AND FUEL ADJUSTMENT
WARNING! During commissioning operations, do not let the burner operate with insufficient air flow (danger of
formation of carbon monoxide); if this should happen, make the fuel decrease slowly until the normal combustion
values are achieved.
WARNING! the combustion air excess must be adjusted according to the values in the following chart.
PS
EV1
EV2
/
EV2
EV1
PGCP
This paragraph describes the integrated proving system operation sequence:
At the beginning both the valves (EV1 and EV2) must be closed.
Test space evacuating: EV2 valve (burner side) opens and keep this position for a preset time
(td4), in order the bring the test space to ambient pressure.Test atmospheric pressure: EV2 clo-
ses and keep this position for a preset time (test time td1). The pressure switch PGCP has not to
detect a rise of pressure.
Test space filling: EV1 opens and keep this position for a preset time (td3), in order to fill the test
space.
Test gas pressure: EV1 closes and keep this position for a preset time (td2). The pressure switch
PGCP has not to detect a pressure drop down.
If all of the test phases are passed the proving system test is successful, if not a burner lockout
happens.
On LMV5x and LMV2x/3x and LME73 (except LME73.831BC), the valve proving can be parameteri-
zed to take place on startup, shutdown, or both. On LME73.831BC the valve proving is parameteri-
zed to take place on startup only.
Содержание HRX2060
Страница 39: ...PART III OPERATION 39 Pump flow rate Nozzle flow rate...
Страница 49: ...Siemens LMV5x Service Manual M12920CC rev 2 1 08 2017...
Страница 56: ...8...
Страница 57: ...9 1 4 1 Servomotor wiring example 1 4 2 Bus cable wiring on LMV5x and AZL doors 1 4 3 EARTH connection example...
Страница 60: ...12 2 2 LMV5x program structure...
Страница 87: ...39...
Страница 94: ......
Страница 95: ......
Страница 96: ...Note Specifications and data subject to change Errors and omissions excepted...
Страница 98: ...Annex1 Example for motor cable...
Страница 99: ......
Страница 100: ...Annex 2 Example for sensor cable...
Страница 101: ......
Страница 102: ......
Страница 106: ......