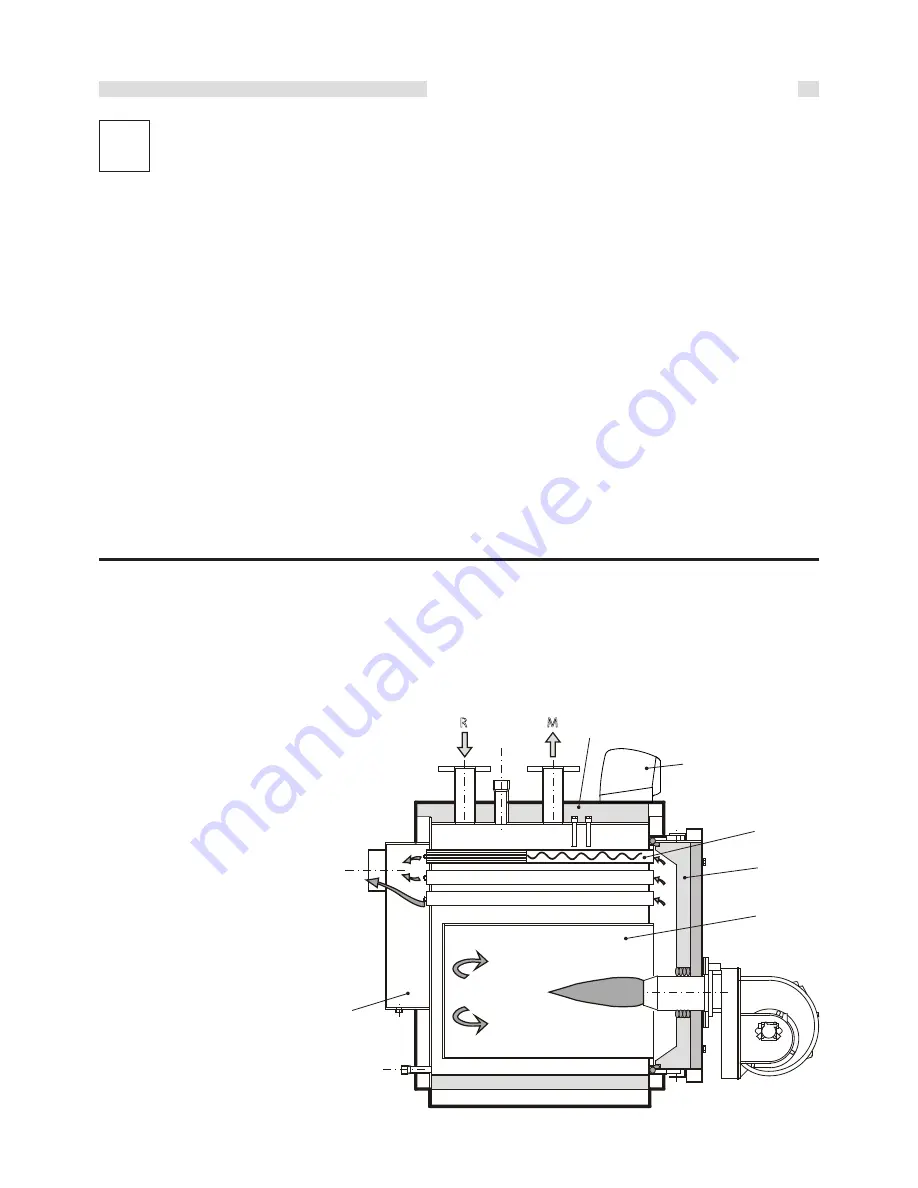
7
Technical features and dimensions
2.1 - TECHNICAL FEATURES
TRISTAR 2S boilers are the horizontal cylindrical type with flame
inversion in furnace and third flue gas pass in tubes.
The construction fully complies with prescriptions laid down in
EN 303 part 1.
The components of the pressurised part, such as sheets and
pipes, are made in certified carbon steel, according to the
EURONORM 25 and EURONORM 28 tables.
Welding devices and procedures are approved by TÜV (D) - UDT
(PL) - SA (S) and ISPESL (I).
Up until model TST 560 2S, the furnace is bonded to the rear
tube plate.
For models TST 680 2S ÷ TST 3100 2S, the furnace is free to
expand (it is only sustained by the front tube plate).
For models from TST 3500 to TST 6100, the furnace is bonded
to the rear tube plate.
The boilers are equipped with an opening door on the right or left.
The outer shell is covered with a glass wool insulation mattress
60 mm thick (from model TST 80 2S to model TST 250 2S), 80
mm thick (from model TST 300 2S to model TST 560 2S), 100
mm thick (from model TST 680 2S to model TST 2350 2S), 80
mm thick (from model TST 2700 2S to model TST 3500 2S), in
turn protected by a mineral fibre fabric.
From models from TST 3900 2S to TST 6100 2S the outer shell
is covered with a lamella mat 50 mm thick, in turn protected by
an aluminium sheet.
The top part of the shell is provided with hooks for lifting the boiler.
Note: TRISTAR 3G 2S boilers are intended to operate with ON/
OFF type GAS burners; as an alternative, they can be equipped
with a dual-stage or modulating burner, as long as the minimum
heat output in the first flame or in modulation does not drop below
60% the furnace load.
The boilers are provided with two ½" connections for conduits
with an inside diameter of 15 mm (suitable to house 3 bulbs
each).
The shell has holes at the sides for the cable glands of the power,
pumps, burner cables and those of any other auxiliary device.
2
TECHNICAL FEATURES
AND DIMENSIONS
2.2 - MAIN COMPONENTS
TRISTAR 2S boilers are equipped with a blind cylindrical furnace,
in which the central flame of the burner is reversed peripherally
towards the front, from whence the combustion gases enter the
smoke pipes. At the end of the pipes they are gathered in the
smoke chamber and sent to the chimney.
The combustion chamber is always pressurised while the burner
is operating, within the power range of the boiler.
For the value of this pressure, see the tables
on pages 9÷14, in the column “Flue gas pressure drop”.
The chimney must be calculated so that
no positive pressure is detected at its base.
1 Furnace
2 Smoke pipes with smoke diverters
(from model TST 300 2S)
3 Door with flame control warning light
4. Smoke chamber
5 Body insulation
6 Panel board
fig. 1
M
R
1
2
4
5
3
6