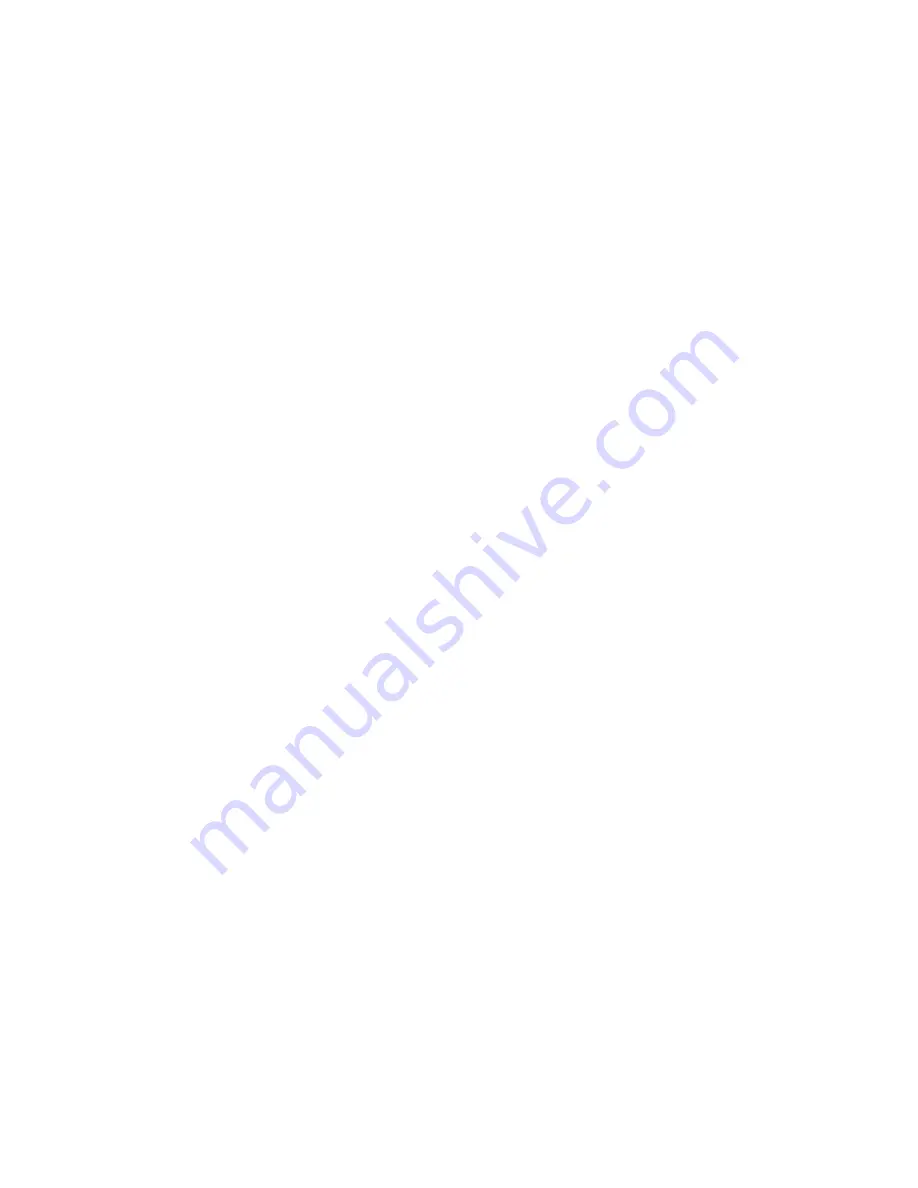
Contents
Pump Identification
..................................................................................................4
1.0 General
................................................................................................................6
1.1 Declaration of Conformity
.................................................................................................. 6
1.2 General Description
............................................................................................................ 8
1.2.1 Limitation
.................................................................................................................................................. 8
1.2.2 Noise Emission ........................................................................................................................................ 8
1.2.3 Marking - CE
............................................................................................................................................. 8
1.2.4 Marking - Standard
................................................................................................................................... 8
2.0 Before Start-Up
...................................................................................................9
2.1 Pump Head
.......................................................................................................................... 9
2.2 Direction of Flow
................................................................................................................. 9
2.3 Pipe Layout
....................................................................................................................... 10
2.4 Port Positioning
................................................................................................................ 10
2.5 Alignment and Mounting Suggestions
........................................................................... 11
2.6 Clean the System Before Start-Up
.................................................................................. 11
3.0 Shaft Seal Service
............................................................................................12
3.1 Double O-Lip
TM
Seal
.......................................................................................................... 12
3.1.1 Double O-Lip
TM
Seal Removal
............................................................................................................... 12
3.1.2 Double O-Lip
TM
Seal Installation
........................................................................................................... 12
3.2 Single Mechanical
TM
Seal
................................................................................................. 13
3.2.1 Single Mechanical
TM
Seal Removal
....................................................................................................... 13
3.2.2 Single Mechanical
TM
Seal Installation
................................................................................................... 13
3.3 Seal Installation- Final Steps
........................................................................................... 14
4.0 Gearbox Maintenance and Service
.................................................................15
4.1 Gearbox Disassembly
...................................................................................................... 15
4.2 Gearbox Assembly
........................................................................................................... 16
4.2.1 Assembling the Gearbox
....................................................................................................................... 16
4.2.2 Assembling the Gearbox- Final Steps
.................................................................................................. 16
4.3 Lubricants and Gearbox Volumes
................................................................................... 17
4.4 Torque Requirements and Limits
.................................................................................... 17
5.0 Rotor Clearances
..............................................................................................18
6.0 Relief Valve Cover Settings and Maintenance
...............................................19
6.1 Setting the Relief Valve Cover
......................................................................................... 20
6.1.1 Setting Relief Valve Cover: P/N 3237
.................................................................................................... 20
6.1.2 Setting Relief Valve Cover: P/N 3239B
................................................................................................. 20
6.2 Relief Valve Cover Maintenance
...................................................................................... 21
6.2.1 Servicing Relief Valve Cover: P/N 3237
................................................................................................ 21
6.2.1 Servicing Relief Valve Cover: P/N 3239B
............................................................................................. 21
7.0 Troubleshooting
...............................................................................................24
8.0 Pump Dimensions ............................................................................................26
9.0 Parts Lists
.........................................................................................................30
Содержание UNIBLOC-PD 501
Страница 26: ...26 UNIBLOC PD Operation Service Manual PD501 576 8 0 Pump Dimensions UNIBLOC PUMP ...
Страница 27: ...UNIBLOC PD Operation Service Manual PD501 576 27 UNIBLOC PUMP ...
Страница 28: ...28 UNIBLOC PD Operation Service Manual PD501 576 UNIBLOC PUMP ...
Страница 30: ...30 UNIBLOC PD Operation Service Manual PD501 576 UNIBLOC PUMP 9 0 Parts Lists ...
Страница 31: ...UNIBLOC PD Operation Service Manual PD501 576 31 UNIBLOC PUMP ...
Страница 33: ...UNIBLOC PD Operation Service Manual PD501 576 33 3 ...
Страница 34: ......
Страница 35: ......