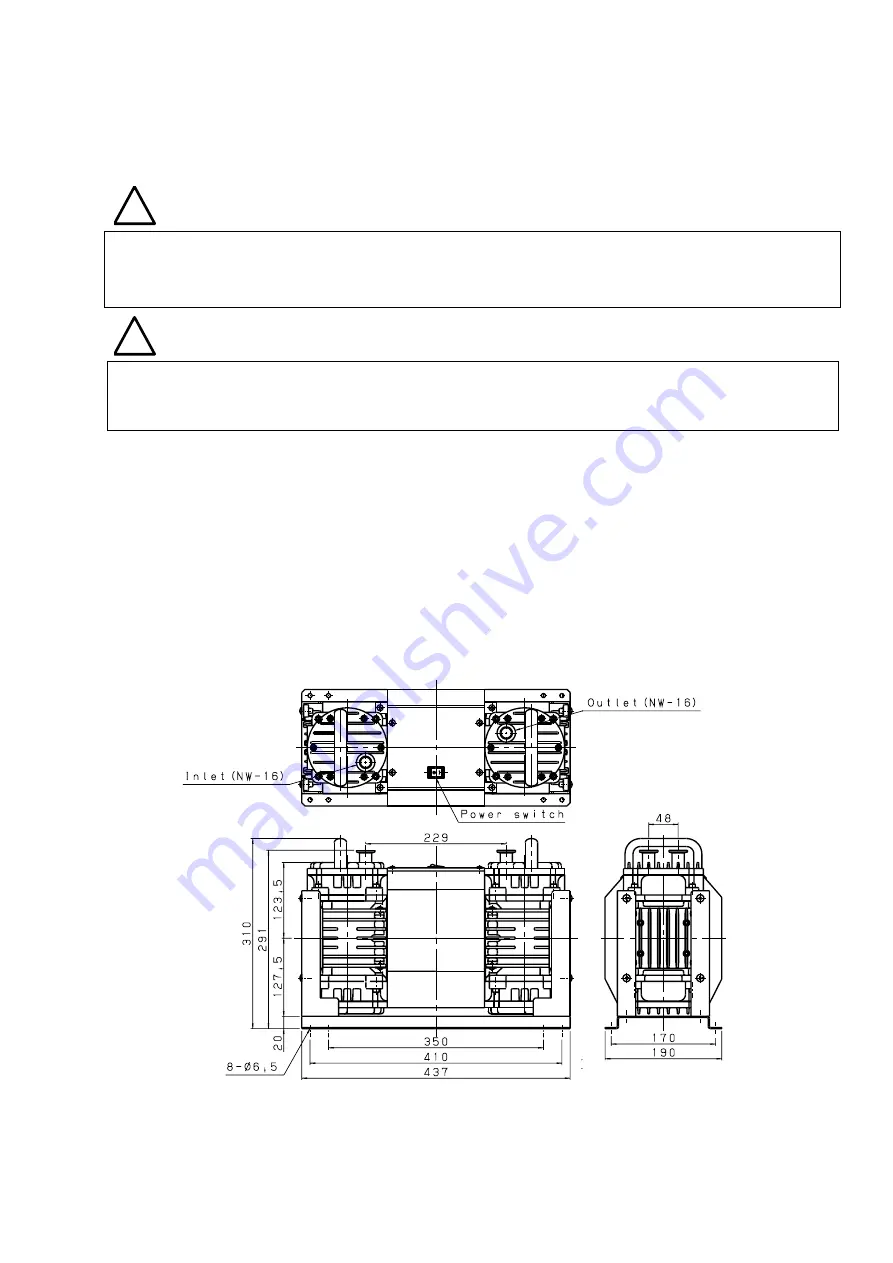
2
1.3
Thermal Protection Relay
1) This pump is fitted with an automatic reset thermal protection relay for overload protection.
This device shuts off the motor power supply circuit automatically to prevent burn-out if the
motor temperature rises due to a pump fault which prevents rotation, or if load becomes
excessive.
2) It is recommended that additional protective devices (eg. earth leakage breaker) be fitted.
*
Use only at the rated voltage for the motor. Use at other voltages will interfere
with normal operation of the overload protection relay, and may result in motor
burnout or fire.
*
When the overload protection relay operates the pump will be extremely hot.
Touching the pump in this condition may result in burns.
1-4 Solenoid Valve (vent valve)
This pump incorporates a solenoid valve (vent valve).
This valve functions to introduce air into the pump chamber, thus eliminating the pressure
difference between the pump chamber and atmosphere, and permitting the pump to be
restarted smoothly.
Note that low voltage, or the timing with which the pump was stopped, may prevent starting of
the pump.
2. Dimensions
Fig.2-1. DAU-100 External Dimensions
!
Warning
!
Caution