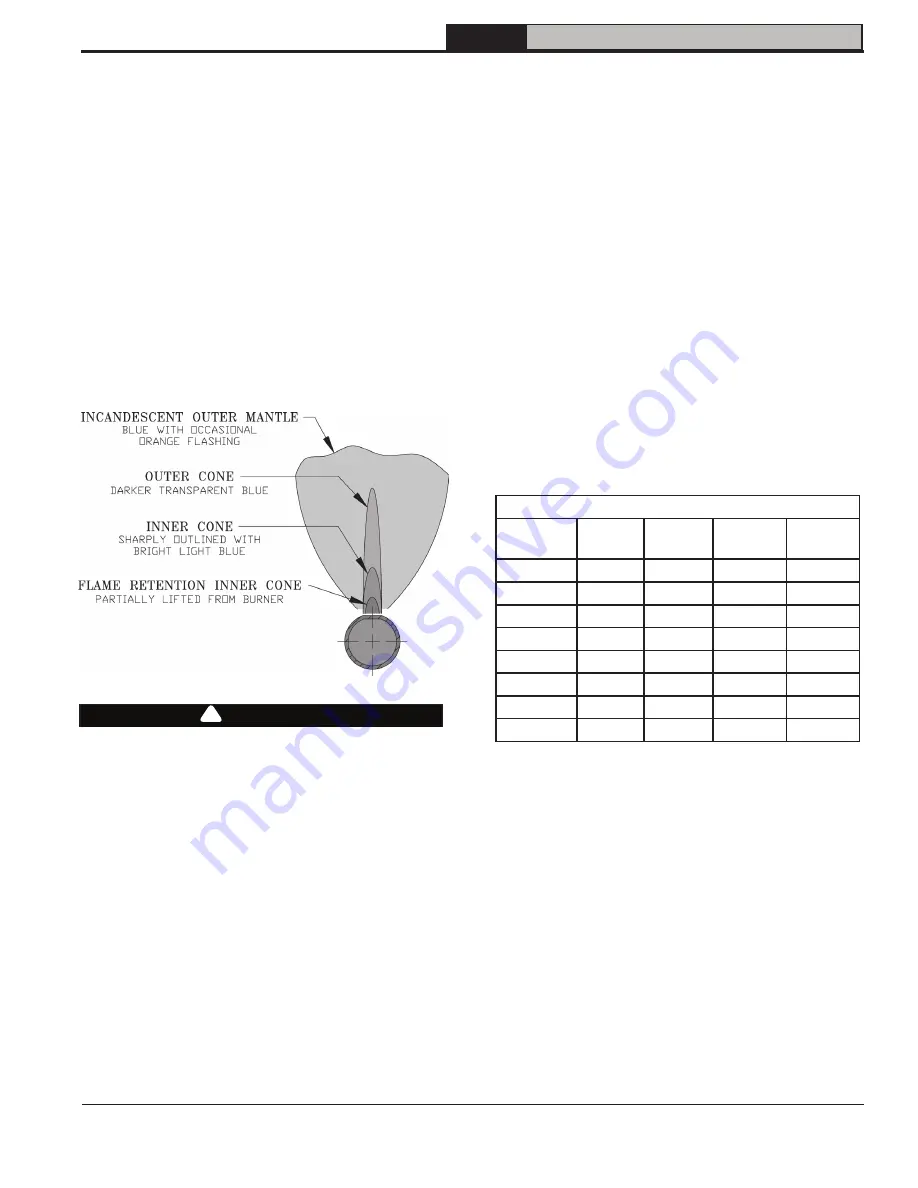
106636-02 - 12/19
21
X-2
Installation, Operating & Service Manual
9
System Start-up and Checkout
(continued)
CAUTION
Avoid operating boiler in an environment where
saw dust, loose insulation fibers, dry wall dust,
etc. are present. If boiler is operated under
these conditions, burner interior and ports
must be cleaned and inspected daily to ensure
proper operation.
!
J. Check Main Burner Flame (see Figure 9-6)
1. NORMAL FLAME:
a. Clearly defined inner cone with no yellow
tipping.
b. Orange-yellow streaks caused by dust
should not be confused with true yellow
tipping.
2. ABNORMAL FLAME (if found, check inlet and
outlet gas pressure. Procedure found in
following steps):
a. Over fired - large flame
b. Under fired - small flames
c. Lack of primary air - yellow tipping on
flames.
K. Check gas inlet pressure
1. While boiler and all other gas appliances
are not firing, gas inlet pressure should not
exceed ½ psig.
2. While boiler and all other gas appliances
are firing, gas inlet pressure must be
between minimum and maximum shown
on rating label.
L. Check gas outlet (manifold) pressure
1. Install manometer on 1/8" outlet pressure
tap on gas valve (see Figure 9-3). Use
of shutoff valve between manometer and gas
valve can prevent pressure surge that blows
out manometer fluid.
2. Adjust regulator on gas valve so manifold
pressure matches values listed on rating label.
3. Turning regulator adjustment screw
clockwise (
) increases pressure.
4. Turning regulator adjustment screw
counterclockwise (
) decreases pressure.
M. Check gas input rate to boiler
1. When checking rate, ensure all other
appliances connected to same meter as
boiler are off.
2. Input ratings shown on boiler rating label
can be used for elevations up to 2,000 ft. For
elevations 2,000 ft. or higher, reduce input
rate to 4 percent per 1,000 ft. above sea level.
Do not install at elevations above 12,000 ft.
See Table below.
Figure 9-6: Main Burner Flame
N. Measure carbon monoxide (CO) level in vent after
5 minutes of main burner operation. CO should
not exceed 400ppm air free.
O. Check vent damper operation.
Vent damper must be in open position when
appliance main burners are operating.
Input (MBH)
Boiler
Model
Rating
Label
5,000 ft. 7,000 ft.
10,000
ft.
X-202
38
30.5
27.5
23
X-203
70
56
50
42
X-204
105
84
76
63
X-205
140
112
101
84
X-206
175
140
126
105
X-207
210
168
151
126
X-208
245
196
176
147
X-209
280
224
202
168