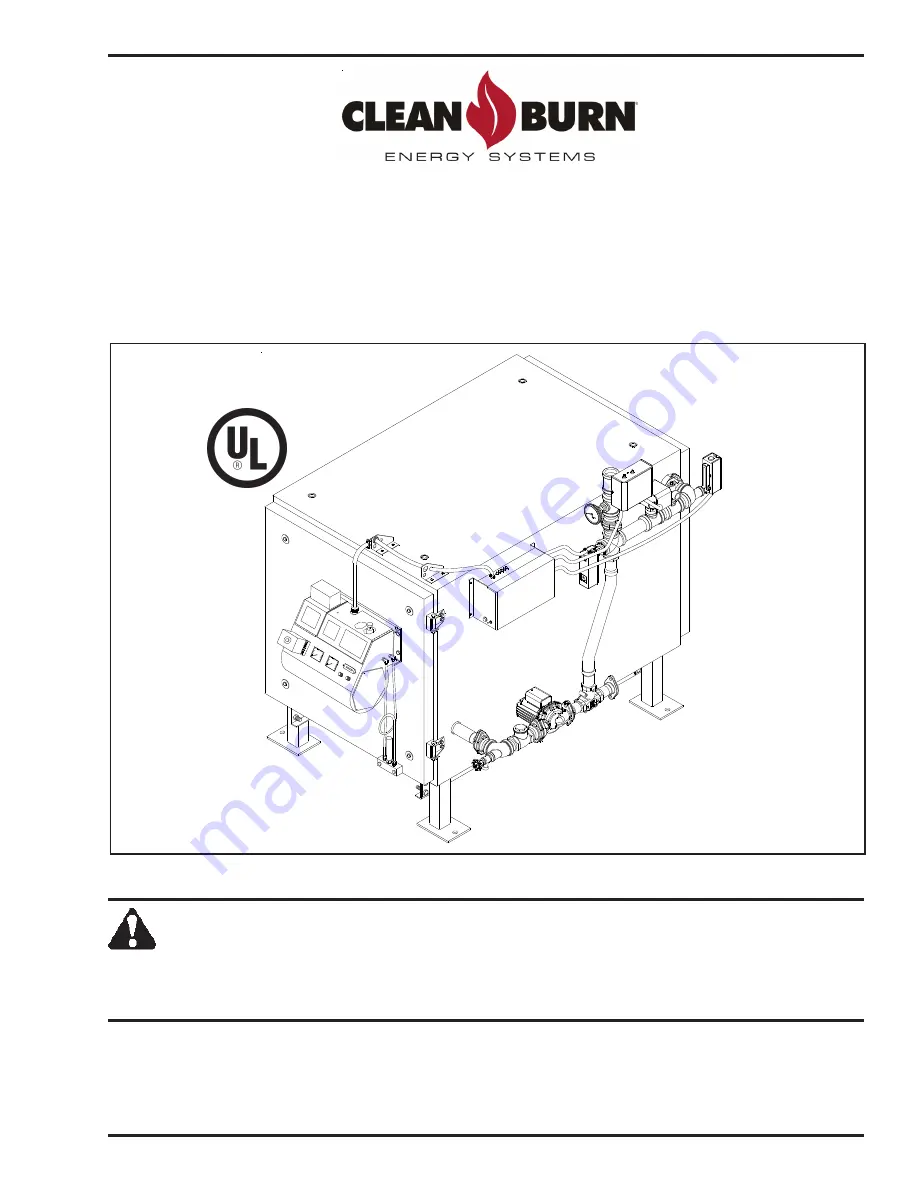
PUBLICATION DATE: 1/24/11, Rev. 11
CLEAN BURN PART #43146
OPERATOR'S MANUAL
CLEAN BURN MODELS:
CB-200-CTB COIL TUBE BOILER
with CB-525-S2 Burner & Metering Pump
CB-350-CTB COIL TUBE BOILER
with CB-551-H3 Burner & Metering Pump
CB-500-CTB COIL TUBE BOILER
with CB-551-H5 Burner & Metering Pump
IMPORTANT FOR U.S. INSTALLATIONS: All installations must be made in accordance with state and local codes
which may differ from the information provided in this manual. Save these instructions for reference.
IMPORTANT FOR CANADIAN INSTALLATIONS: The installation of this equipment is to be accomplished by
qualified personnel and in accordance with the regulation of authorities having jurisdiction and CSA Standard B 139,
Installation Code for Oil Burning Equipment.
WARNING: DO NOT assemble, install, operate, or maintain this equipment without first
reading and understanding the information provided in this manual. Installation and
service must be accomplished by qualified personnel. Failure to follow all safety precautions
and procedures as stated in this manual may result in property damage, serious personal injury
or death.
I88460−C
U.L. Listed Used Oil
Burning Appliance
#MH15393
Manufactured & Tested to meet
ASME Section IV
Summary of Contents for CB-200-CTB
Page 2: ......
Page 4: ......
Page 20: ...CoilTubeBoilerOperator sManual ModelsCB 200 CTB CB 350 CTB andCB 500 CTB 1 12 ...
Page 24: ...CoilTubeBoilerOperator sManual ModelsCB 200 CTB CB 350 CTB andCB 500 CTB 2 4 ...
Page 72: ...CoilTubeBoilerOperator sManual ModelsCB 200 CTB CB 350 CTB andCB 500 CTB 5 6 ...
Page 78: ...CoilTubeBoilerOperator sManual ModelsCB 200 CTB CB 350 CTB andCB 500 CTB 6 6 ...
Page 82: ...CoilTubeBoilerOperator sManual ModelsCB 200 CTB CB 350 CTB andCB 500 CTB 7 4 ...
Page 86: ...CoilTubeBoilerOperator sManual ModelsCB 200 CTB CB 350 CTB andCB 500 CTB 8 4 ...
Page 108: ...CoilTubeBoilerOperator sManual ModelsCB 200 CTB CB 350 CTB andCB 500 CTB 11 8 ...
Page 117: ...CoilTubeBoilerOperator sManual ModelsCB 200 CTB CB 350 CTB andCB 500 CTB A 9 ...
Page 140: ...CoilTubeBoilerOperator sManual ModelsCB 200 CTB CB 350 CTB andCB 500 CTB A 32 ...
Page 148: ...CoilTubeBoilerOperator sManual ModelsCB 200 CTB CB 350 CTB andCB 500 CTB C 2 ...