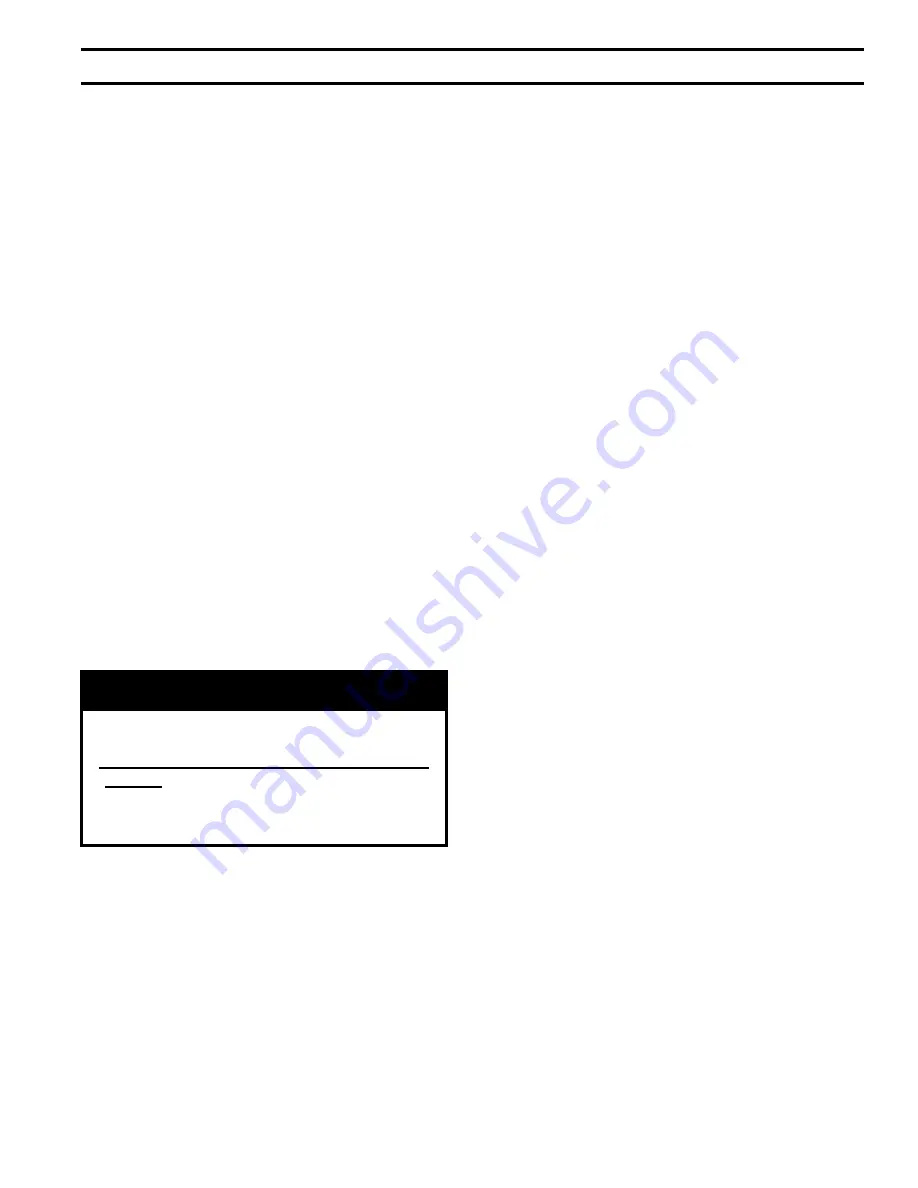
7
A.
INSPECT SHIPMENT
carefully for any signs of
damage.
1. ALL EQUIPMENT is carefully manufactured,
inspected and packed. Our responsibility ceases
upon delivery of created Boiler to the carrier in good
condition.
2. ANY CLAIMS for damage or shortage in shipment
must be filed immediately against the carrier by
the consignee. No claims for variances from,
or shortage in orders, will be allowed by the
manufacturer unless presented within sixty (60) days
after receipt of goods.
B.
LOCATE BOILER
in front of final position before
removing crate. See Figure 1.
1. LOCATE so that smoke pipe connection to chimney
will be short and direct. BOILER IS SUITABLE
FOR INSTALLATION ON COMBUSTIBLE
FLOOR.
2. FOR BASEMENT INSTALLATION, provide a
concrete base if floor is not perfectly level, or if
water may be encountered on floor around Boiler.
3. PROVIDE CLEARANCE of at least 24" on right
side of Boiler for cleaning flueways and for removal
of Tankless Heater. Provide clearance of at least
14" in front (measured from front jacket panel) for
servicing burner.
C.
PROVIDE COMBUSTION AND VENTILATION
AIR
. Local code provisions may apply and should be
referenced.
WARNING
Adequate combustion and ventilation air must
be provided to assure proper combustion and
to maintain safe ambient air temperatures.
DO NOT install boiler where gasoline or other
flammable vapors or liquids, or sources of
hydrocarbons (i.e. bleaches, fabric softeners,
etc.) are used or stored.
1. Determine volume of space (boiler room). Rooms
communicating directly with the space in which
the appliances are installed, through openings not
furnished with doors, are considered a part of the
space.
Volume(ft
3
) = Length(ft) x Width(ft) x Height(ft)
2. Determine total input of all appliances in the space.
Add inputs of all appliances in the space and round
the result to the nearest 1000 BTU per hour.
3. Determine type of space. Divide Volume by total input
of all appliances in space. If the result is greater than or
equal to 50 ft
3
/1000 BTU per hour, then it is considered
SECTION II: PRE-INSTALLATION
an
unconfined space
. If the result is less than 50 ft
3
/1000
BTU per hour then the space is considered a
confined
space
.
4. For boiler located in an
unconfined space of a
conventionally constructed building
, the fresh air
infiltration through cracks around windows and doors
normally provides adequate air for combustion and
ventilation.
5. For boiler located in a confined space or an unconfined
space in a building of unusually tight construction,
provide outdoor air with the use of two permanent
openings which communicate directly or by duct
with the outdoors or spaces (crawl or attic) freely
communicating with the outdoors. Locate one opening
within 12 inches of top of space. Locate remaining
opening within 12 inches of bottom of space. Minimum
dimension of air opening is 3 inches. Size each opening
per following:
a.
Direct communication with outdoors.
Minimum
free area of 1 square inch per 4,000 BTU per hour
input of all equipment in space.
b.
Vertical ducts.
Minimum free area of 1 square inch
per 4,000 BTU per hour input of all equipment in
space. Duct cross-sectional area shall be same as
opening free area.
c.
Horizontal ducts.
Minimum free area of 1 square
inch per 2,000 BTU per hour input of all equipment
in space. Duct cross-sectional area shall be same
as opening free area.
Alternate method for boiler located within confined
space.
Use indoor air if two permanent openings
communicate directly with additional space(s) of
sufficient volume such that combined volume of
all spaces meet criteria for unconfined space. Size
each opening for minimum free area of 1 square
inch per 1,000 BTU per hour input of all equipment
in spaces, but not less than 100 square inches.
6. Louvers and Grilles of Ventilation Ducts
a. All outside openings should be screened and
louvered. Screens used should not be smaller
than 1/4 inch mesh. Louvers will prevent the
entrance of rain and snow.
b. Free area requirements need to consider the
blocking effect of louvers, grilles, or screens
protecting the openings. If the free area of the
louver or grille is not known, assume wood
louvers have 20-25 percent free area and metal
louvers and grilles have 60-75 percent free area.
c. Louvers and grilles must be fixed in the open
position, or interlocked with the equipment
to open automatically during equipment
operation.
Содержание V13A RO/FO
Страница 5: ...5 SECTION I GENERAL INFORMATION Figure 1 VI RO FO Water Boiler with Tankless Heater Beckett AFG Burner...
Страница 40: ...40 XI REPAIR PARTS continued Figure 25 Flush Jacket Components...
Страница 42: ...42 XI REPAIR PARTS continued Figure 26 V1 RO FO Trim and Controls...
Страница 48: ...48 U S Boiler Company Inc P O Box 3020 Lancaster PA 17604 1 888 432 8887 www usboiler net...