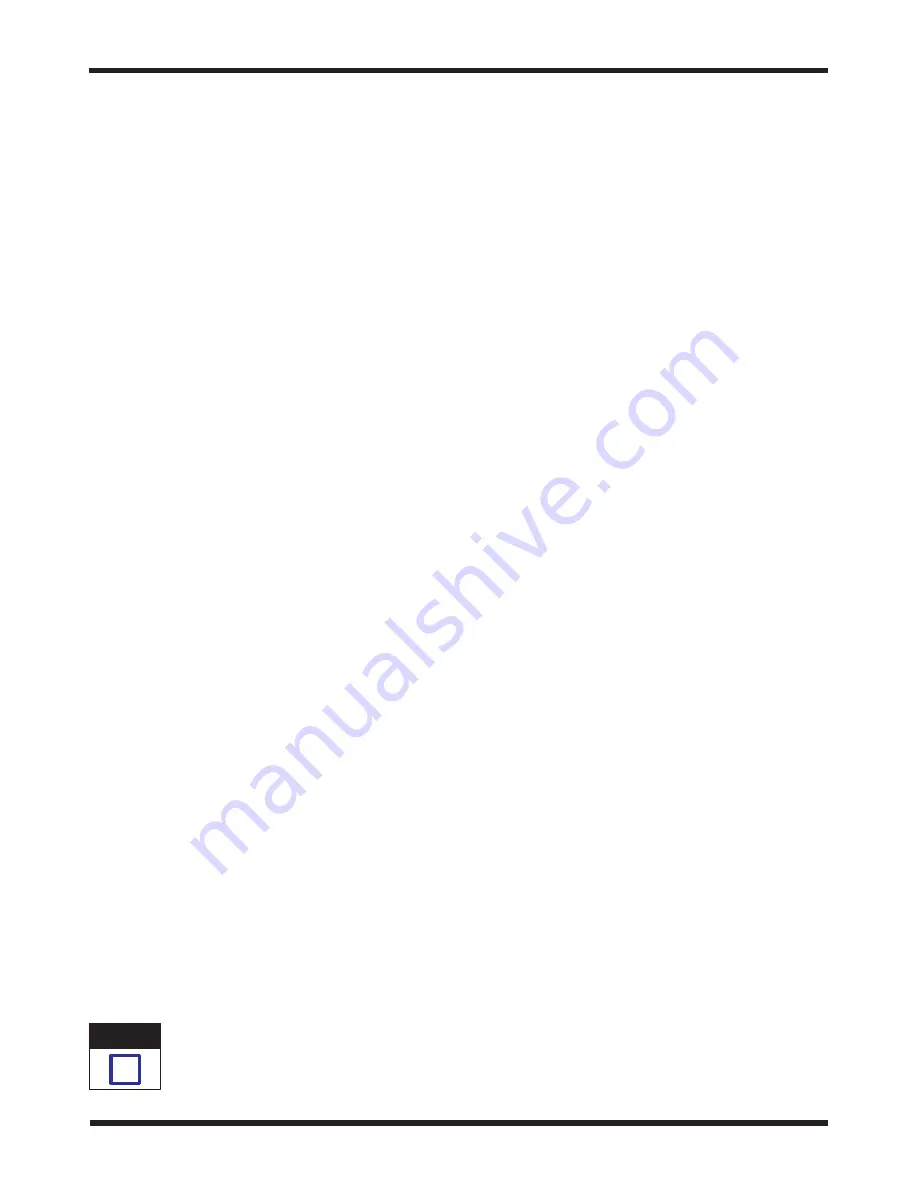
409-10083
AMP 3K andAMP 5K Terminating Machines with the SL Starlite CQM
Rev E
13 of 38
Tyco Electronics Corporation
c. Trigger/Trg. Edge = H –> L
d. Sorting Output/Mode = Standard
e. Sorting Output/Learn as = Good
f. Sorting Output/Duration = 100ms
A. Machine Power Up
During power up, the machine looks to see if the monitor’s interface cable is connected. Specifically, it
looks to see if the jumper from J10–3 to J10–4 is installed on the CPU/Motor Controller Board.
If the jumper is seen, the green and yellow lights will alternately flash a couple of times on power up. If the
jumper is not detected, the green and yellow lights flash together a couple of times.
After seeing the jumper, the machine looks to see if the monitor is ready to accept a crimp by looking at
the monitor’s STOP output relay. The STOP relay is a normally open relay that is closed when the monitor
is ready for a crimp.
If the STOP relay is not closed when the machine is powered up, it will flash both lights seven times
(Monitor Not Detected Fault).
This fault can be cleared by holding down the footswitch until the lights stop flashing or by cycling power
on the machine.
B. Cycling the Machine
When the footswitch is pressed to cycle the machine, the machine looks at the SL Starlite’s STOP output
and the GOOD crimp output. The indicator light, DS2, on the machine’s CPU/Motor Controller Board
indicates the status of the STOP output. The light will be turned on when the STOP output is closed.
If the STOP output is not closed, the green and yellow lights will flash together three times (Monitor Not
Ready Fault). If the GOOD crimp output is not OFF (open) the green and yellow light will flash together six
times (Good Crimp Signal Fault).
Both of these faults can be cleared by holding the footswitch until the lights stop flashing or by cycling
power on the machine.
C. BadCrimp Fault (After the Machine Cycles)
After the machine has been cycled, the machine looks at the monitor’s GOOD crimp output and at the
STOP relay output. If the GOOD crimp output is pulsed and the STOP relay output remains closed, the
machine will be ready for the next crimp cycle.
If the GOOD crimp is not pulsed and the STOP relay is open, the monitor has detected a BAD crimp and
both the green and yellow light will be flashed four times (Bad Crimp Fault).
The fault can be cleared by holding the footswitch until the lights stop flashing, or by cycling power on the
machine.
D. Crimp Analysis Fault (After the Machine Cycles)
If the GOOD crimp pulse is not detected and the STOP relay output remains closed (after the machine
has cycled), the green and yellow light will be flashed five times (Crimp Analysis Fault). This fault could be
the result of a faulty trigger sensor.
The fault can be cleared by holding the foolswitch until the lights stop flashing, or by cycling power on the
machine.
4.3. Applicator Installation
These instructions apply to Machines -15, -16, -19, -20, -23, and -24. Since machines -17 and -18 do not contain
a quick-release feature, they do not contain a quick-change mounting base plate. The appropriate additional
baseplate tooling will be required on machines -17 and -18. The -21, -22, and -25 machines use a swing handle to
release applicators. Installation is in the reverse order of removal.
NOTE
i