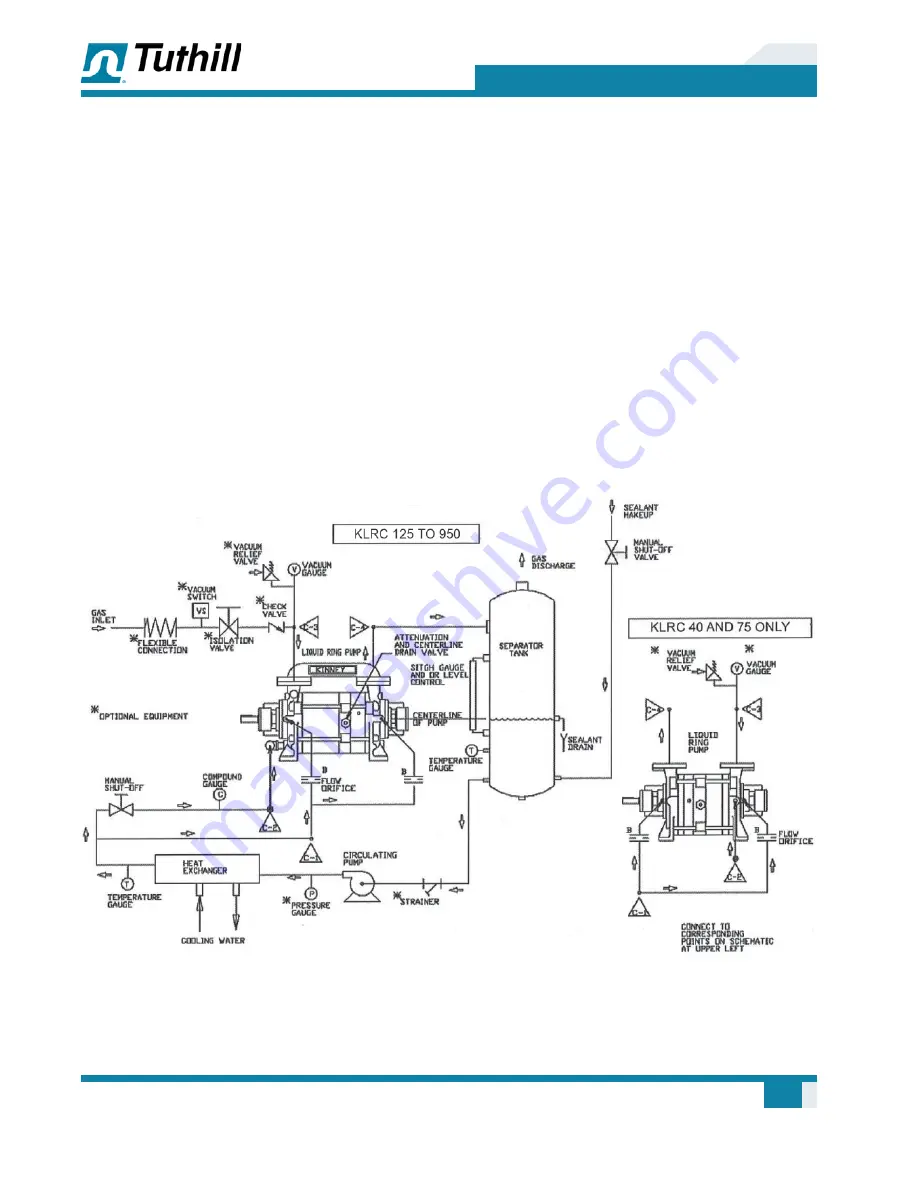
9
03
Installation
Manual 4804 Rev C p/n 004804 0000
FULL SEALANT RECOVERY (FSR)
A full sealant recovery system is a closed-
loop sealing con
¿
guration that employs a heat
exchanger (water- or air-cooled) to maintain proper
sealing
À
uid temperature.
See Figure 3-3
for piping
arrangement. This arrangement is not suitable
for prolonged operation at pressure above 400
Torr (533.28 mbar) unless a circulating pump is
installed.
Full liquid recovery systems often operate under
conditions where condensation would cause the
liquid level to rise, making it necessary to drain
liquid from the unit in order to maintain the liquid
level. The opposite condition can exist whereby
liquid evaporation makes it necessary to add
makeup liquid to maintain the liquid level. If there
are extensive piping
¿
ttings and valves and other
restrictive devices in the sealant line on a full
recovery system that does not use a circulation
pump, the sealant liquid is induced into the
pump under pump suction entirely. For sustained
operation above 400 Torr (533.28 mbar), on rapid
cycling of pump-down from the atmosphere, a
circulation pump may be required. A circulation
pump, when added to a full recovery system,
maintains proper sealant
À
ow at all inlet pressure
conditions.
The pressure on the sealant gauge will vary
depending upon the inlet pressure, from several
inches of vacuum to a slightly positive pressure.
Normally, a common supply line is used for both
seal liquid and mechanical seal cooling.
The optional system components are described
on
page 12
.
Figure 3-3 – Piping Schematic: Full Sealant Recovery System with Circulating Pump
Содержание KLRC Series
Страница 6: ...iv Table of Contents Manual 4804 Rev C p n 004804 0000 ...
Страница 33: ...27 08 Reassembly Manual 4804 Rev C p n 004804 0000 Figure 8 2 Bearing Driver Tool ...
Страница 34: ...28 08 Reassembly Manual 4804 Rev C p n 004804 0000 Figure 8 3 Foot Alignment Tool ...
Страница 37: ...31 09 Troubleshooting Manual 4804 Rev C p n 004804 0000 NOTES ...
Страница 38: ...32 Parts Lists and Assembly Drawings Manual 4804 Rev C p n 004804 0000 CROSS SECTION KLRC 40 AND KLRC 75 ...
Страница 42: ...36 Parts Lists and Assembly Drawings Manual 4804 Rev C p n 004804 0000 CROSS SECTION KLRC 125 TO KLRC 525 ...