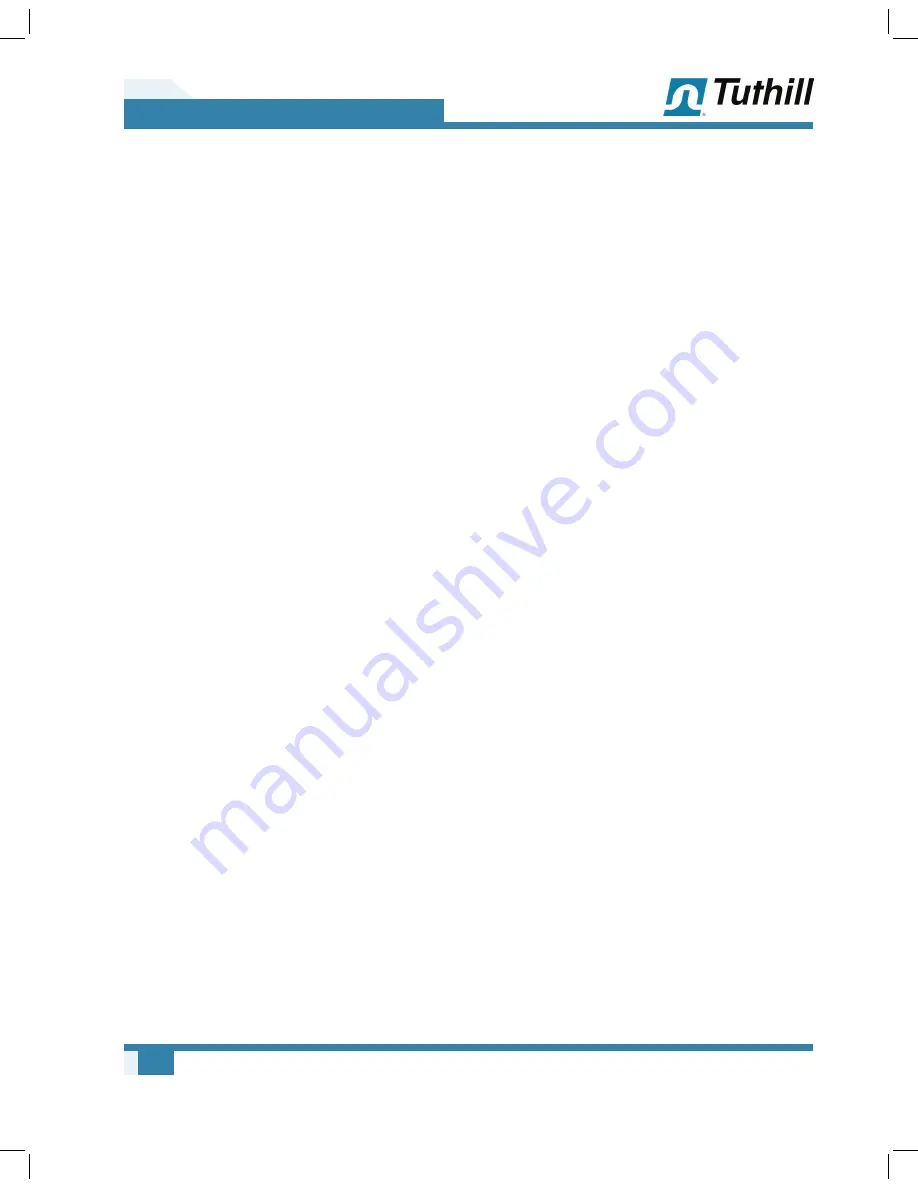
24
07
Maintenance
Manual 1843 Rev B p/n 001843 0000
Changing the Oil
Run the pump until the oil reaches a normal
operating temperature of 145 to 165°F (63 to 75°C)
and pressure below 100 Torr (130 mbar). Stop the
pump, place a container under the oil drain valve
and open the valve until the oil is removed from the
pump. Close the valve.
If the oil is being drained because it has been
contaminted, drain the oil from the discharge
valve well. The well is between the pump cylinder
and separator housing. Oil trapped there can be
drained by removing the pipe plug(s) from the
cylinder located above the heads.
When the oil has drained from the pump, close all
drains and fill the pump with the quantity and type
of oil shown in the specifications. The oil level will
show above the center of the sight gauge until the
pump is started and the oil is distributed through
the pump.
Oil Contamination
When the pump has operated satisfactorily for
some time followed by gradually declining vacuum
performance, clean the oil by applying gas ballast,
or change the oil as directed in
Changing the Oil
on page 24
. A change in the color of the oil does
not necessarily mean that it is not satisfactory for
use. On the other hand, vapors may contaminate
the oil and not show any color change.
The following factors may cause the pump oil to
deteriorate:
• Water and solvents will lower viscosity
• Solid accumulation will increase viscosity and
“feel gritty”
• Polymerization and chemical attack on oil will
change viscosity and odor
As a “Rule of Thumb,” the oil should be changed if:
• The oil “feels gritty”
• Viscosity changes more than 100 SSU @ 100°F
(38°C)
• Oil color becomes opaque
• Smells burnt or acrid
• Total Acid Number increases to 0.3
In a new application, it is recommended that the oil
be changed at intervals of 500 hours of operation
and that the oil change interval be reduced or
increased, depending on the condition of the oil
after that period of operation, according to the
previous guidelines.
If oil contamination is suspected, change the
oil and operate the pump for 15 to 30 minutes.
Repeat this procedure as required to flush out all
contaminants from the pump or operate the pump
with gas ballast as explained under
Gas Ballast
on page 19
and
Handling Large Quantities of
Water on page 19
.
Oil filtration systems are available for filtering
solids, water, and acids continuously or
periodically.
REPLACEMENT PARTS
Replacement parts for the KT-150 C Series and
KT-300, KT-500, and KT-850 D Series pumps used
with standard hydrocarbon vacuum pump oil are
shown in
Pump Parts List – KT-150C, KT-300D,
KT-500D, KT-850D on page 39
. Two levels
of maintenance kits are available for the KT line
of pumps. Contact the factory with serial number
information for kit part numbers. Delivery can be
provided at that time.
Various parts, particularly internal components for
earlier versions of KT-series pumps, are different
and cannot be interchanged. Many pumps are
ordered and equipped with special modifications
and accessories, or adaptations for special fluids.
Therefore, when ordering spare parts, the pump
model and nameplate serial number must always
be provided to ensure verification and shipment of
the correct parts.