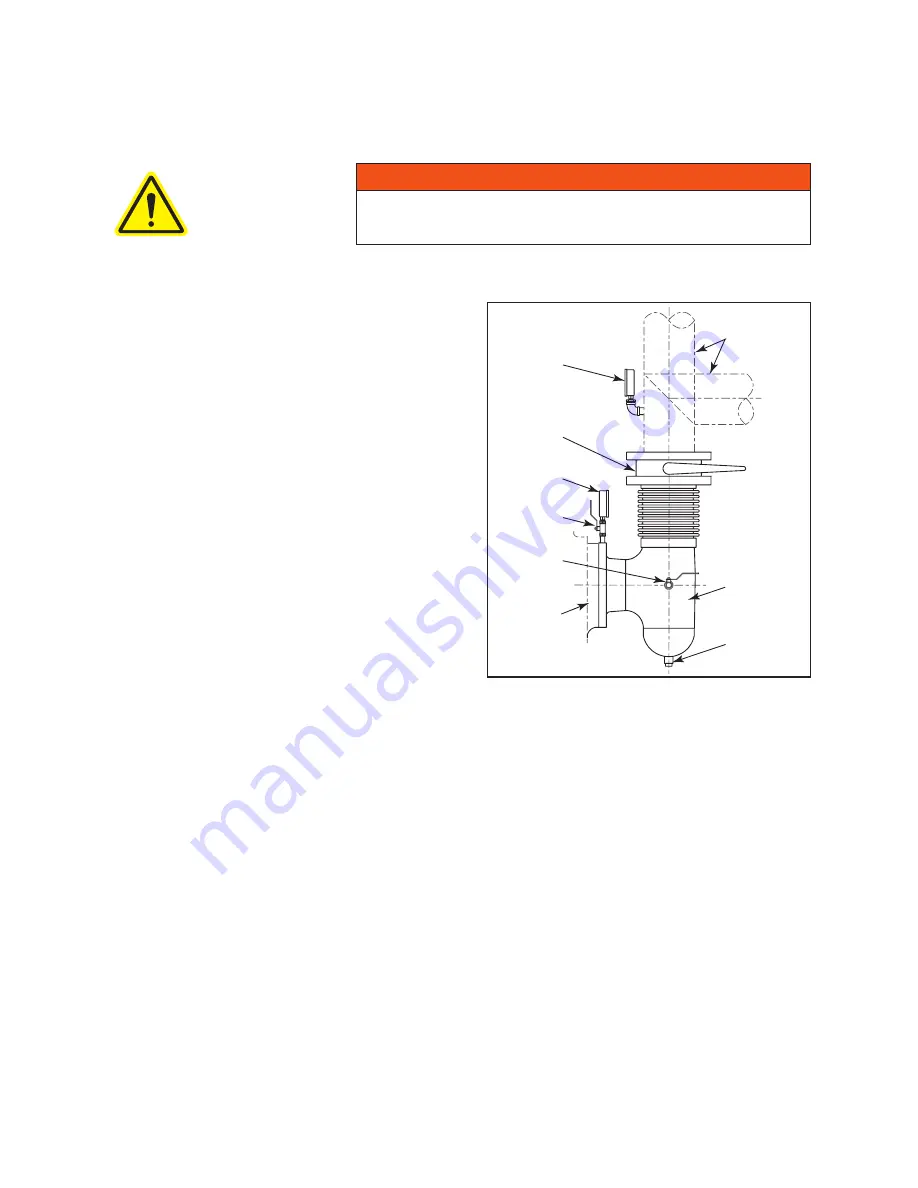
11
5.4 PIPING CONNECTIONS
Manifolding should be no smaller than the pump connections in oder to minimize restrictions to gas flow.
Accurately align the mating flanges to the inlet and discharge manifolding to prevent distortion of the pump
housing.
WARNING
Pipe loading on the pump should be negligible as pipe loading can cause
distortion of the pump. Use proper supports and pipe hangers to assure
that there is no loading.
5.4.1 MAIN PIPING
SUCTION MANIFOLDING
Inlet manifolding should be sized and designed with
four objectives in mind:
•
To avoid gas flow restrictions.
•
To prevent pump fluids from entering the process
chamber.
• To protect the pump from the ingestion of
particulate matter.
• To allow proper venting of the pump and suction
manifold.
Under the normal conditions, the diameter of the
manifolding should not be less than the diameter of the
pump connection and the pipe length should be kept
to a minimum.
Oil may splash from inside the pump through the
suction port so the suction line must be designed to
prevent oil from collecting there and draining back to
the system or process. See Figure 2 for recommended
arrangement as a guide for fabricating inlet manifolding.
In all cases the inlet manifolding should include a 90° flanged elbow vertically oriented upward to retain
pump oil at low pressures, an isolation valve, and a flex connector, and vent valve.
A flexible connection should be installed in the suction manifold to provide freedom for vibramounts. The
vacuum piping must be well aligned with the pump connections so as not to place a strain on the piping.
Provisions for gauge installation and any other drilling in the piping must be made prior to piping installation,
otherwise, drilling particles entering the piping could be entrained into the pump. A vacuum isolation valve
should be installed adjacent to the suction port to be used for leak checking, shutting down the system, or
blanking off the pump.
Before connecting the suction manifolding, distribute 4 quarts of oil over the three slide pins. This will
necessitate reaching through the suction port with a container and pouring oil directly onto the slide pins.
Then rotate the pump by hand a minimum of two revolutions to distribute the oil throughout the pump
interior.
During the initial operation and as long thereafter as necessary, a fine mesh screen should be installed
across the inlet connection to prevent abrasive or solid particles left in the line from being sucked into the
pump. This screen can be removed when particles no longer accumulate. If particles continue to accumulate,
a filter should be installed in the line.
VACUUM
GAUGE
VACUUM
GAUGE
ISOLATION
VALVE
AIR VENT
VALVE
SHUT OFF
VALVE
PUMP
SUCTION
FLANGE
TRAP
DRAIN
TO
SYSTEM
RIGHT
ANGLE
FLEXIBLE
CONNECTOR
Figure 2 - Detailed Manifold Arrangement
Содержание KINNEY 850D
Страница 29: ...29 NOTES ...
Страница 35: ...35 NOTES ...