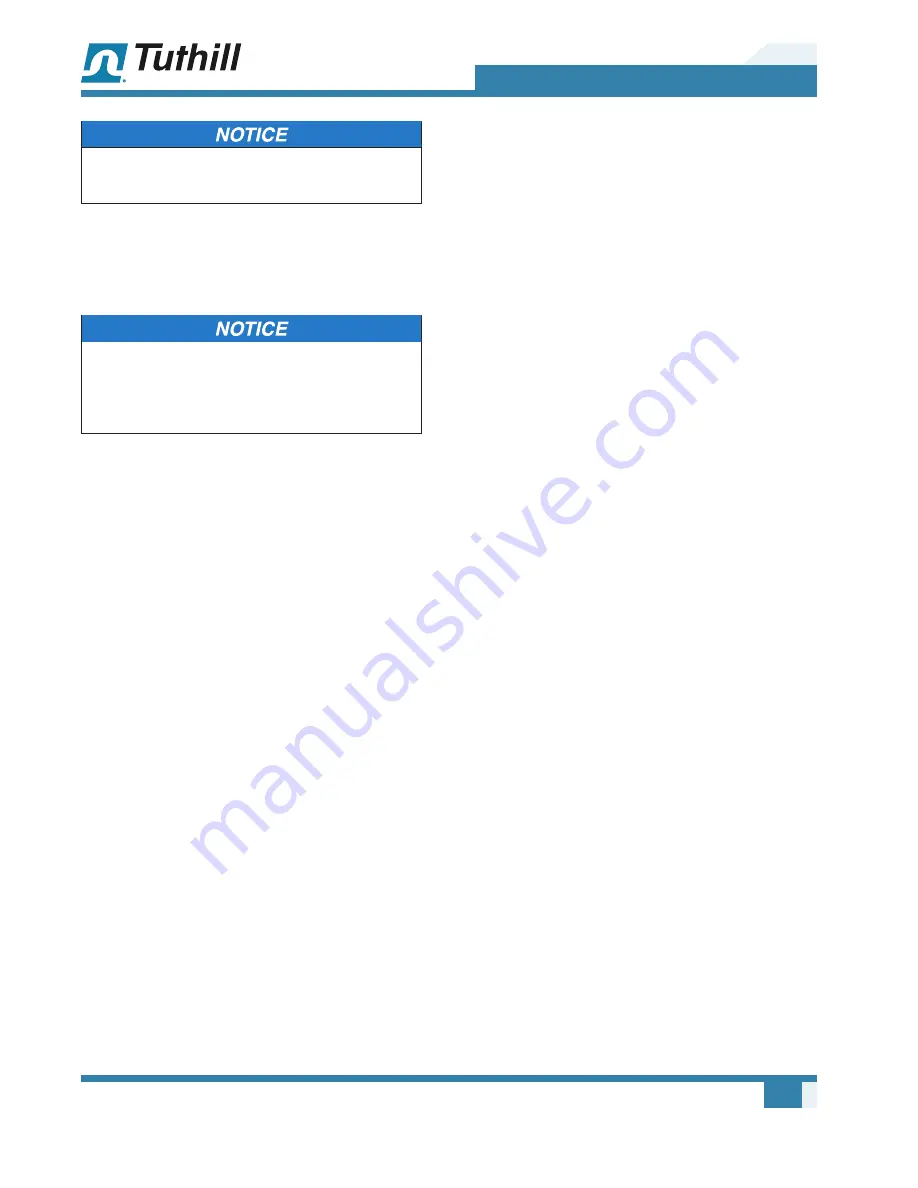
Manual 2003 Rev D p/n 2003
11
05
Installation
Remove the protective covers from the shaft
and inspect for damage.
Carefully check to ensure that no transit damage
has been sustained. If damage has occurred from
shipment, file a claim with the carrier immediately.
Preserve the shipping container for inspection by
the carrier.
If booster sustains damage while being
shipped to your facility, do not return it to
the factory without first obtaining shipping
instructions from Tuthill.
Do not remove protective covers and plugs until
the connections are complete. Mount the booster
on a flat, level surface. Use a baseplate that is
rigid, solidly supported, and structurally sound.
Shim under the legs where necessary so that
each leg of the booster supports an equal share
of the booster weight. This is necessary to prevent
eventual twisting of the booster. Make sure the
feet rest evenly on the mounting surface before
fastening down. Twisting or cramping the booster
during mounting will cause rotor contact and
binding during operation, resulting in a condition
called “soft foot”.
See Soft Foot on page 12
for
further details and preventative measures.
A booster that is factory-mounted on a base should
not require the above adjustments. However, since
the assembly can become twisted in shipping or
installation, check for soft foot after installating the
base. Shims may be needed for alignment. Loosen
the foot hold-down screws to check foot contact
with the mounting surface. Mount the base on a
solid foundation or heavy flooring, using shims as
necessary at bolting points to prevent warping the
assembly.
Transmission of small operating vibrations to a
support structure may be objectionable in some
applications. Use of vibration isolators or vibration
absorbing materials can be effective in overcoming
this transmission. To avoid causing distortion,
apply the treatment under the common motor/
booster base or mounting plate rather than directly
under the feet alone.
Make sure piping is accurately squared with the
booster and supported independently. Stress
imparted from incorrectly aligned piping or
mounting will create problems with bearing and
seal life, possibly leading to internal contact. The
booster should sit stress-free and evenly on its
supporting surface. Take care to evenly tighten
the mounting bolts to avoid imparting undue stress
into the booster. Stress can be checked in a free
state with feeler stock or verified on a previously
installed booster with the aid of a dial indicator.
Spring or gap should be less than 0.002 in.
(0.05 mm).
A booster may be driven by direct-coupling to
the driver or by V-belt drive for the purpose of
obtaining other speeds within the approved
range.
See Motor Drives on page 18
for
more information.
Boosters from Tuthill Vacuum & Blower Systems
are internally and externally treated after factory
assembly and testing to protect against rusting in
normal atmospheric conditions prior to installation.
The maximum period of internal protection is
considered to be up to 6 months under average
conditions, provided closing plugs and seals are
not removed. Protection against chemical or salt-
water atmosphere is not provided. Avoid opening
the booster until ready to begin installation, as
protection will be quickly lost due to evaporation.
For recommended preparations for long term
storage (longer than 6 months),
see Long-Term
Storage on page 28
.
Booster Air Intake
To minimize maintenance, supply the booster with
the cleanest air possible. The air must not contain
any flammable or toxic gases, as the booster
will concentrate these gases. This could result in
damage to the booster and surrounding property
and lead to personal injury or death. Do not block
or restrict the opening or the booster, as the motor
and booster could overheat and fail.
Do not use boosters on explosive or hazardous
gases. Do not exceed the limits described in
Table 4-1 – Specifications on page 8
on
pressure differential, running speed, and discharge
temperature.