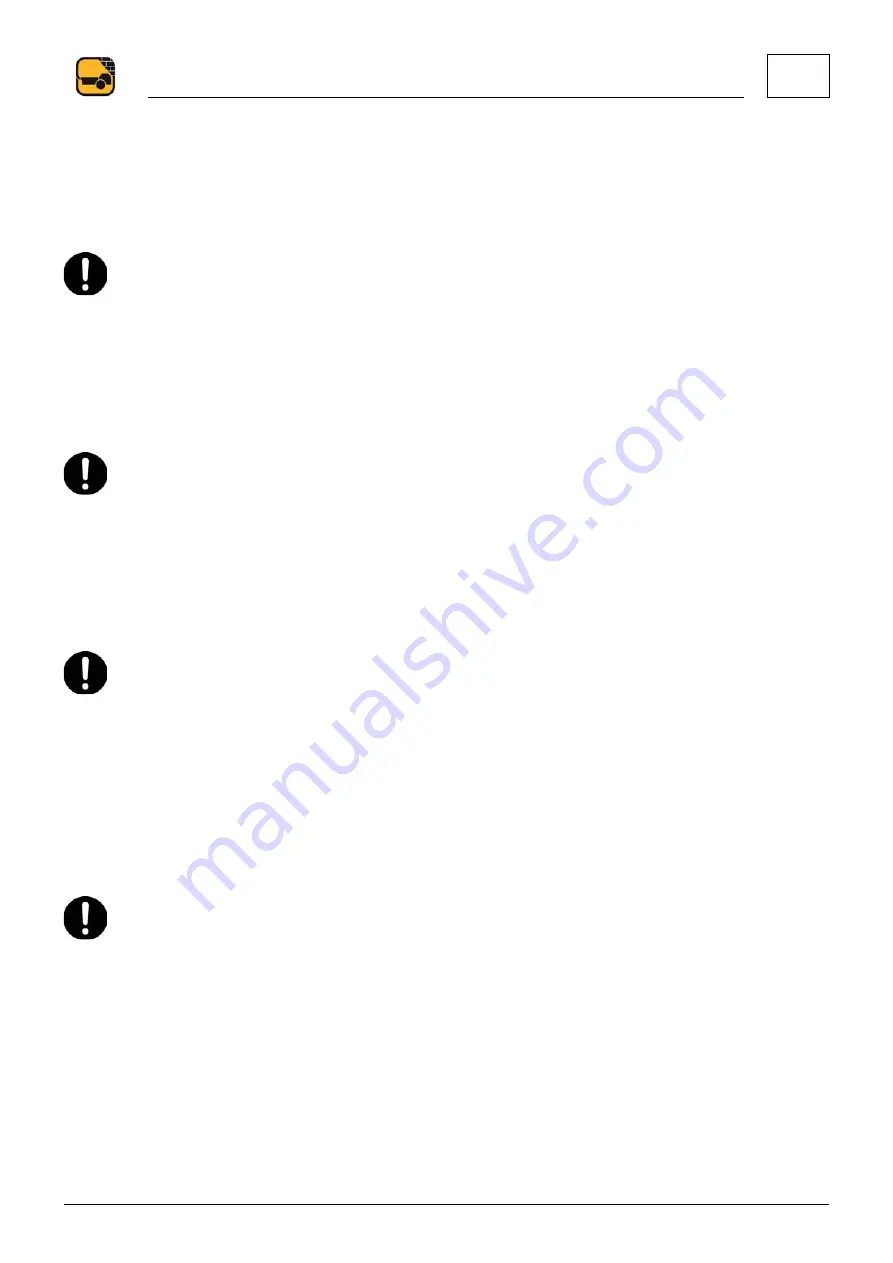
MAINTENANCE
6
561400 - IS16/09 - EN
69/84
6.1.7
Conveying pipe anchor check
When
When beginning work
Anchor state
Clean, not released from the conveying pipes
Tools
Visual inspection
None
Check the good condition of the anchors: the metal parts must not be damaged or rusty, the rubberised canvas parts must not
be cut or torn.
If the anchors are damaged or you are not sure of their good condition, replace them with new and original
ones.
6.1.8
Pneumatic piping check
When
When beginning work
Pipe state
Clean, disconnected from the machine
Tools
Visual inspection
None
The pipes must always be in good conditions. The rubber must not be cut or cracked. The fittings must not be deformed and
the locking system must be intact. The seal gasket inside the fitting must be intact and not be cut or deformed.
If the pipes are damaged or you are not sure of their good condition, replace them with new and original
ones.
6.1.9
Spraying gun check
When
When beginning work
Gun state
clean and disconnected
Tools
Visual inspection
None
Check that the nozzle is clean; the flap must be intact and the valves perfectly working. The fittings must not be deformed and
the closing cams must fasten properly.
If the certain parts of the gun are damaged or you are not sure of their good condition, replace them with
new and original ones.
6.1.10
Check the pumping pressure gauge
When
When beginning work
Machine state
With machine off and cold
Tools
Visual inspection
None
Check that pressure gauge 1 is not broken or illegible (e.g. due to fouling).
Check that the transparent rubber 2 is not broken or deformed.
Check that there are no large air bubbles inside the gauge.
On the contrary, replace the pressure gauge.
If the pressure gauge is damaged or you are not sure of its good condition, replace it with a new and
original one.
Содержание T20X
Страница 1: ...Serial number Year USE AND MAINTENANCE MANUAL T20X IS16 09 561400 EN ORIGINAL ...
Страница 2: ...THIS MANUAL IS PROPERTY OF TURBOSOL ANY TOTAL OR PARTIAL REPRODUCTION IS STRICTLY FORBIDDEN ...
Страница 3: ...THIS MANUAL IS PROPERTY OF TURBOSOL ANY TOTAL OR PARTIAL REPRODUCTION IS STRICTLY FORBIDDEN ...
Страница 17: ...MACHINE PRESENTATION 2 561400 IS16 09 EN 17 84 ...
Страница 39: ...SAFETY AND PREVENTION 3 561400 IS16 09 EN 39 84 ...
Страница 47: ...TRANSPORT AND INSTALLATION 4 561400 IS16 09 EN 47 84 ...
Страница 51: ...USE AND OPERATION 5 561400 IS16 09 EN 51 84 1 2 3 4 5 6 7 8 9 11 10 12 ...
Страница 62: ...5 USE AND OPERATION 62 84 561400 IS16 09 EN ...
Страница 80: ...7 DEMOLITION 80 84 561400 IS16 09 EN ...
Страница 84: ...8 TROUBLESHOOTING 84 84 561400 IS16 09 EN ...