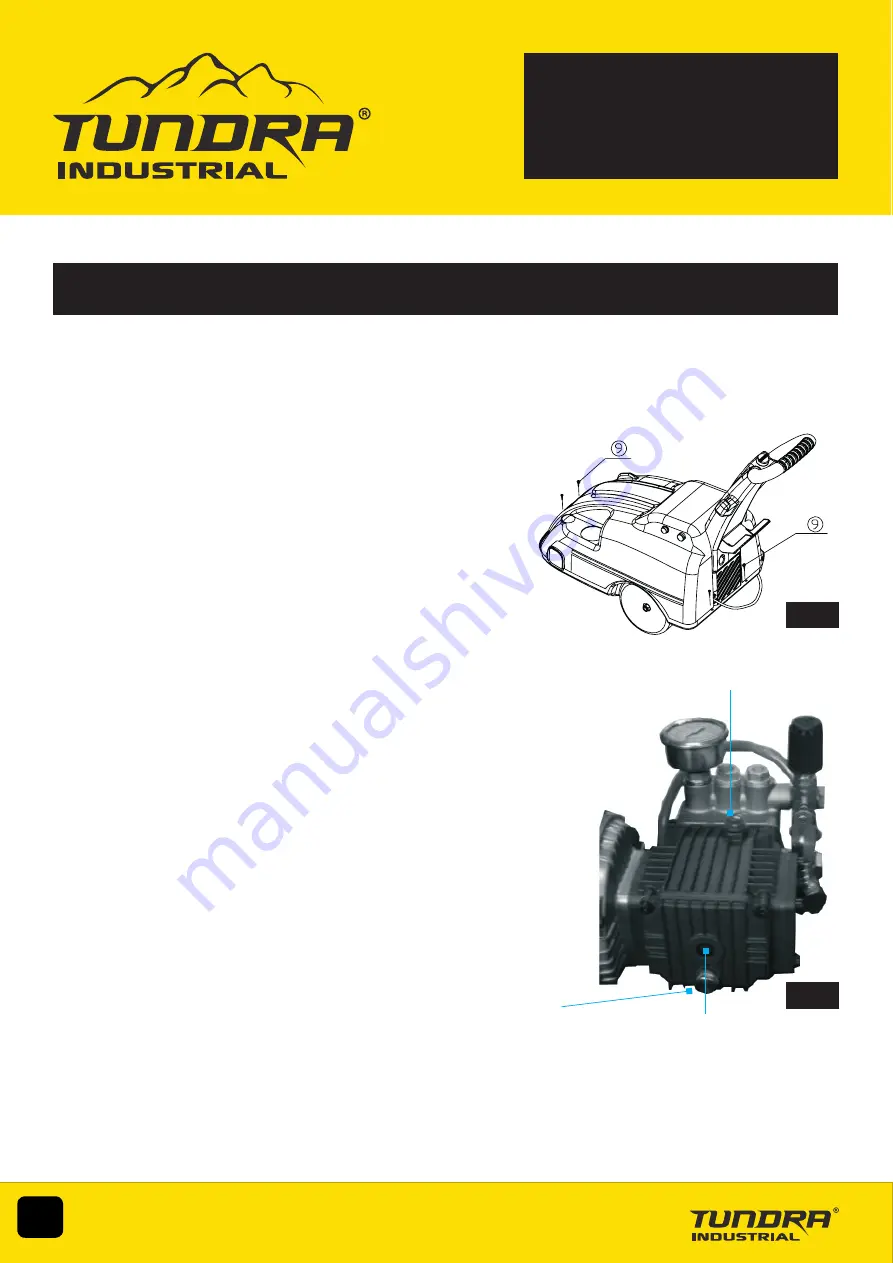
12
USER MANUAL
TUNWAS12-100
v.1.1
MAINTENANCE
IMPORTANT:
Before performing any maintenance be aware that the equipment should be completely shutdown, depressurised and allowed to
cool down. This will ensure that no injuries can be sustained by moving parts, water pressure or hot surfaces. All repairs should be carried out by
approved engineers. All replacement parts should be supplied or recommended by Tundra Industrial. Any unapproved repairs or modifications will
invalidate the warranty. To ensure efficient operation and longer life of your pressure washer a routine maintenance schedule should be prepared
and followed. If the equipment is used in unusual conditions such as high-temperature or dusty conditions more frequent maintenance checks will
be required.
Pump Oil:
Change the pump oil regularly. Change the pump oil after the first 50 hours
of work and successively every 100 hours. In either case ensure that the oil
is changed at least once a year. Oil Type: SAE 15W-40
To access the pump to top up the oil level or change the pump oil
transport bung as described earlier in the manual remove the 4 screws on
the housing as shown in (
Fig.10
).
Remove the dipstick and fill the oil level using a funnel as required. The
capacity of the oil reservoir is 375ml ±5ml (
Fig.11
)
Changing Oil:
Remove the drainage bung and gather the waste oil into a suitable container. Clean any
spillage or residue and replace the drainage bung.
Spray Gun & Nozzle Cleaning:
Keep the gun case, trigger area and quick release connections clean at all times Check and clean
regularly with every use.
If the nozzle becomes clogged with dirt and debris excessive pressure can build up. If the nozzle
becomes partially clogged or restricted the pump pressure will fluctuate and can become harmful
and dangerous.
Clean the nozzle immediately and follow these instructions:
1. Shut-off the engine and turn off / disconnect the water supply.
2. Pull the trigger on the gun to relieve any water pressure
3. Disconnect the lance from the gun
4. Remove the nozzle from the lance - remove any obstructions
with the nozzle cleaning tool provided and back flush with clean water
5. Direct the water supply into the spray wand end to back flush loosened
particles for 30 seconds.
6. Reassemble the nozzle onto the lance
7. Reconnect the lance to the gun and turn on the water supply
8. Start the washer pump and place the lance into the high pressure setting to test.
Cleaning The Water Filter:
The water filter should be checked regularly and cleaned if necessary:
1.
Remove the filter by grasping the end and removing it from the water inlet on the pump
2.
Clean the filter by flushing it with water on both sides
3.
Re-insert the filter in the water inlet on the pump
Fig.10
Fig.11
Pump Oil
Sight Glass
Oil Transit Bung / Dipstick
Replace as described
Pump Oil
Drainage Bung
Содержание COLD WASH TUNWAS12-100
Страница 1: ...USER MANUAL TUNWAS12 100 v 1 1 COLD WA SH ...
Страница 16: ...16 USER MANUAL TUNWAS12 100 v 1 1 PARTS LIST DIAGRAM ...
Страница 20: ...20 USER MANUAL TUNWAS12 100 v 1 1 ...