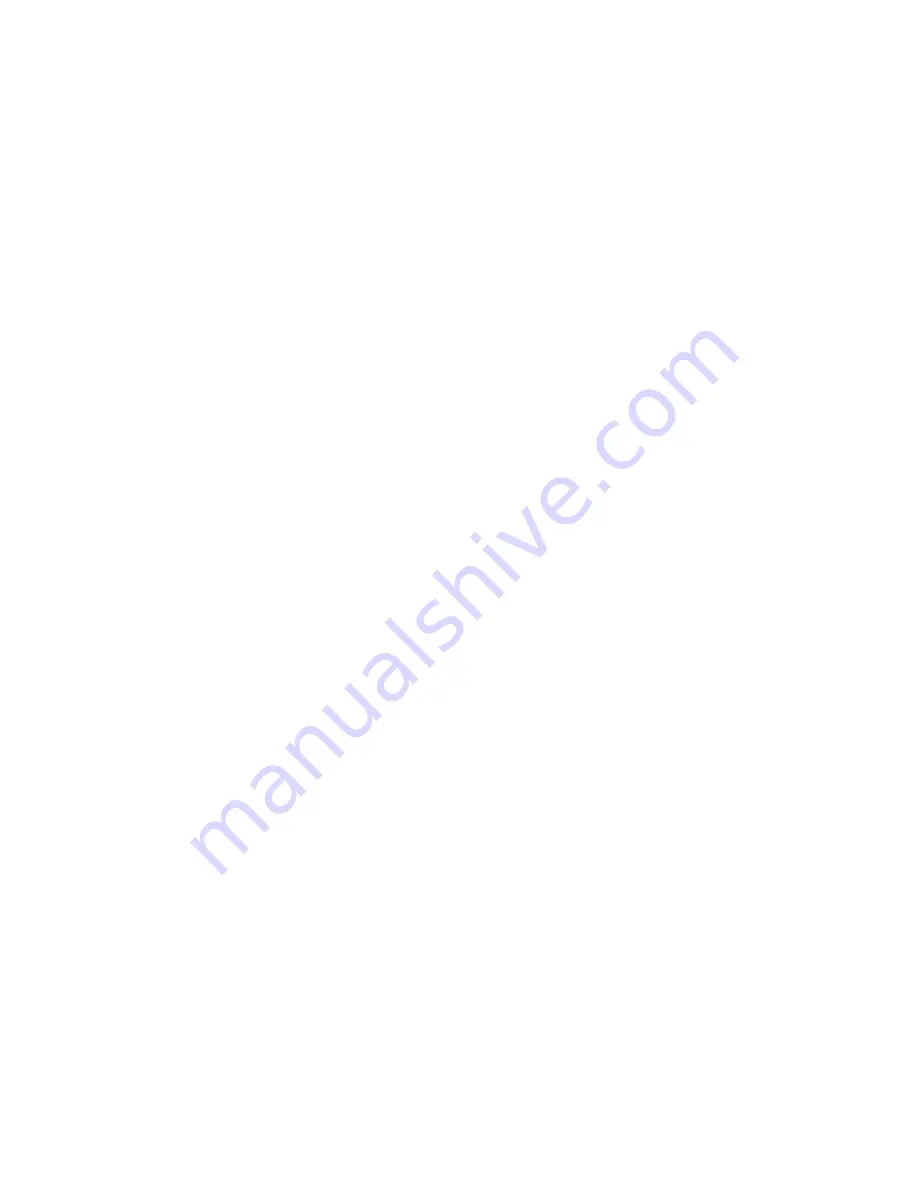
minimal amount of time.
5.
Apply solder to the work and not the iron. A properly heated (and clean) connection will
readily accept solder, further reducing the chances for unreliability.
6.
Use only clean, good quality, rosin core solder. Poor quality or dirty solder will not melt
smoothly and will deposit contaminants into the connection, making it weak.
7.
Use only the amount of solder necessary to flow into and around the connection. Too
much solder can create a “solder bridge” with a neighboring connection. If too little
solder is used, the connection will be physically and electrically weak.
8.
Finish the connection by removing both the solder and the soldering iron quickly and at
the same time. It is important to apply heat only for as long as is needed to properly
flow the solder. Too much heat runs the risk of overheating the parts being soldered.
9.
Do not move the parts of the connection while the solder is hardening. It is important
that everything stays totally still until the solder has fully set. Any movement while the
solder is in a plastic state will result in a weak, unreliable, and cracked connection.
10.
Clean any rosin residues from freshly made solder connections. Solder flux residues
can trap moisture, dirt and dust that can weaken a connection and possibly create
arcing conditions. Cleaners such as Isopropyl or ethyl alcohol and even acetone are
very good at removing flux residues. Use a stiff bristled (acid) brush to mechanically
scrub the surfaces as well as a paper towel to absorb the contaminants.
By following the below sequence of events every time you make a solder connection, your
connections will perform better than ever before. And they will look great too …
Sequence of Events in Making a Good Connection
1.
Make sure all surfaces to be soldered are clean and free of oxides.
2.
Establish a good mechanical connection of the components prior to soldering.
3.
Place the tip of the iron firmly against the connection to be soldered.
4.
Let connection reach soldering temperature (usually within 1 to 5 seconds).
5.
Feed solder into the point where the soldering iron tip meets the connection.
6.
Feed just enough solder into the connection for the solder to flow around the
components to be joined.
7.
When adequate solder amounts have been applied, remove the unused solder and
soldering iron simultaneously.
8.
Keep the connection totally still until the solder has solidified.
9.
Clean any solder flux residue from the connection.
A note regarding soldering to anything gold plated
Gold plating is great for a corrosion free signal transfer but problematic for soldering
reliability. Where as solder adheres wonderfully well to gold plating, gold plating often doesn't
stick well to the base metals to which it is plated. This is the underlying problem.
Connections soldered directly to gold plating will adhere for awhile. But eventually the gold
plating will peel off the base metal (while still adhering to the solder) leaving no connection
with the intended base metal. This has become a broken connection.
The solution is to always scrape the gold plating off of a potential connection, down to the
base metal, prior to soldering. This will guarantee a faithfully soldered connection.
TubeDepot.com 39
Содержание JTM45+
Страница 17: ...TubeDepot com 13 Drawing 5 5a Drawing 5 5b T65 T63...
Страница 20: ...16 TubeDepot com photo 5 11a...
Страница 21: ...TubeDepot com 17 photo 5 11b...
Страница 27: ...TubeDepot com 23 drawing 5 15c...
Страница 33: ...TubeDepot com 29 drawing 7 1...
Страница 38: ...10 Schematic 34 TubeDepot com...