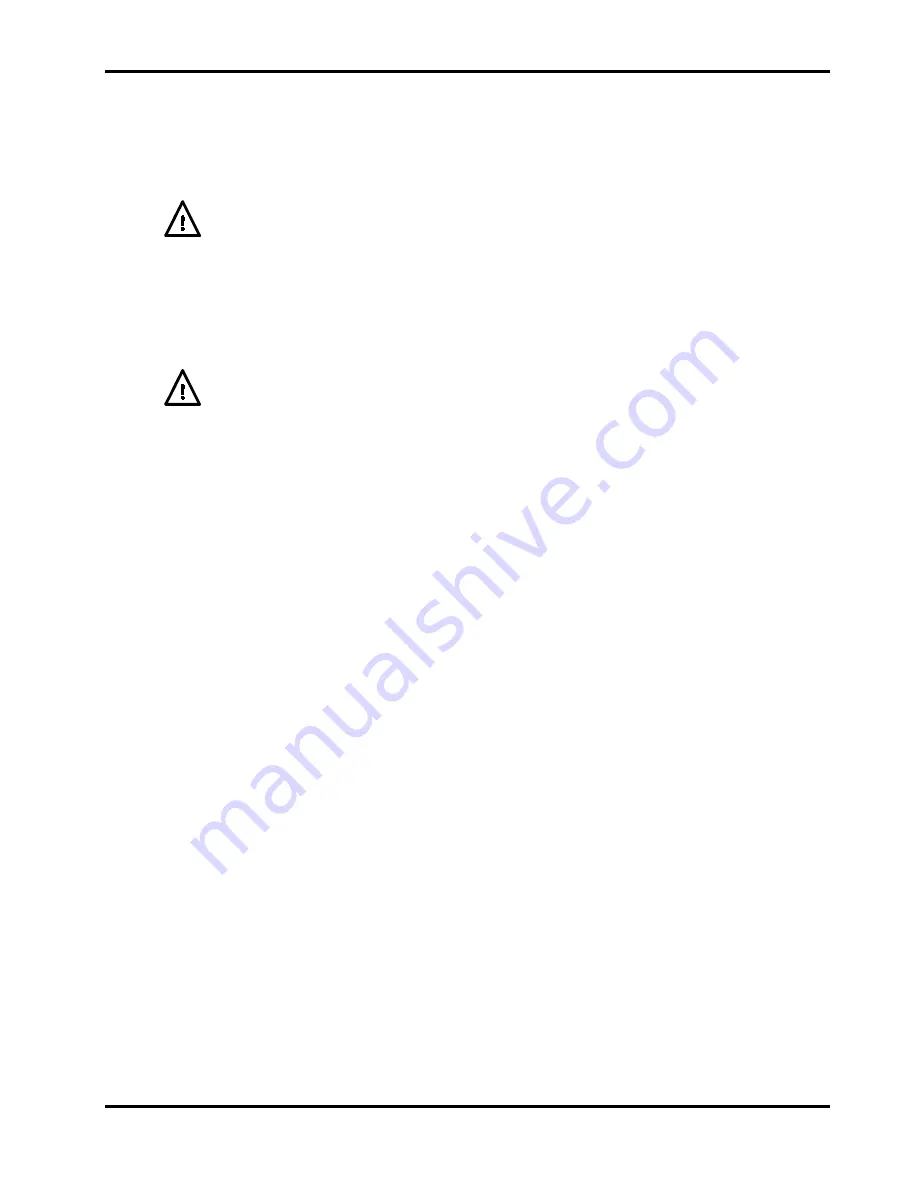
11
Battery replacement
The battery consists of three 2.5Ah NiMH cells. They are conservatively constructed and should
provide hundreds of charge-discharge cycles. Extended storage or use in high temperature
environments may reduce cell life. If it appears that the discharge time has reduced significantly,
or if the cell voltages have become mismatched, then the cells may be replaced.
Replace all three cells simultaneously, using new cells of the same make and type.
Use only A or AF size 2.5Ah NiMH (Nickel Metal Hydride) rechargeable cells.
Do not use AA size cells. Do not use Nickel Cadmium cells.
Remove the top cover of the instrument and disconnect the ribbon cable from the rear of the
Main PCB. Disconnect the AC adaptor.
Remove the old cells from the unit by cutting the tags attached to the battery and then the tie-
wraps holding them to the PCB. Cut the tags; do not attempt to unsolder them. Tape up the cells
to avoid accidental short circuits and dispose of safely.
Do not incinerate the cells, or place them with domestic waste.
Dispose of them in accordance with local regulations and facilities.
These cells are recyclable.
Early units may be fitted with cells having tags with connecting holes; these are attached to the
PCB with lengths of wire. Current production cells have tags without holes. These are attached
using standard 0.025” square connecting posts taken from a SIL pin header. Clean up the
connections and fit new posts if required.
Note that there is a thermistor near the centre cell which is used by the charger circuit to sense
its temperature. Place a small amount of heatsink compound over the thermistor to ensure good
thermal conductivity.
Place the cells on the PCB, making sure that they are all correctly oriented (they all point in the
same direction) and that the tags are aligned with the correct connecting pads. Secure the cells
to the PCB with tie-wraps (only sufficiently tight to hold the cells – do not bend the PCB).
Finally wrap the tags around the 0.025” square posts and solder as quickly as possible. It is
important not to overheat the seals of the cell.
As quickly as possible, confirm the polarities by using a DVM to check that the voltage between
the test points T0V (to the right of the USB socket) and TV (in front of the large gold heatsink
area) is equal to the sum of the cell voltages – it should be between 3V and 4V.
Reattach the ribbon cable to the Main PCB. The unit should now be functional.
Attach the AC adaptor and provide power; it the cell voltages are low charging will start
automatically, in which case wait a few minutes until the cells are charged past the threshold.
Test the charge termination circuits as follows:
Press SW1 to start charging, then briefly short LK1: charging should stop.
Press SW1 again, then briefly short LK2: charging should stop.
Place a shorting link across LK3 (to run the timer at test speed)
Note the time and press SW1 to start charging; charging should stop in 45 to 55 secs.
Wait a further 60 secs then press SW1 again; charging should not restart.
Disconnect the AC power and remove the test link across LK3. If any of these test fail, return the
PCB for repair or replacement.
Re-apply power, press SW1 and monitor the first charging cycle by watching the yellow charge
indicator on the front panel. Charging must automatically stop within four hours. At the end of the
charging cycle check that the cell voltages are equal within ±50mV and that the temperature of
the three cells feels similar to the touch.
If charging does not automatically stop, then it should be assumed that the old cells were
destroyed by a faulty charging circuit and the whole PCB should be returned for repair.