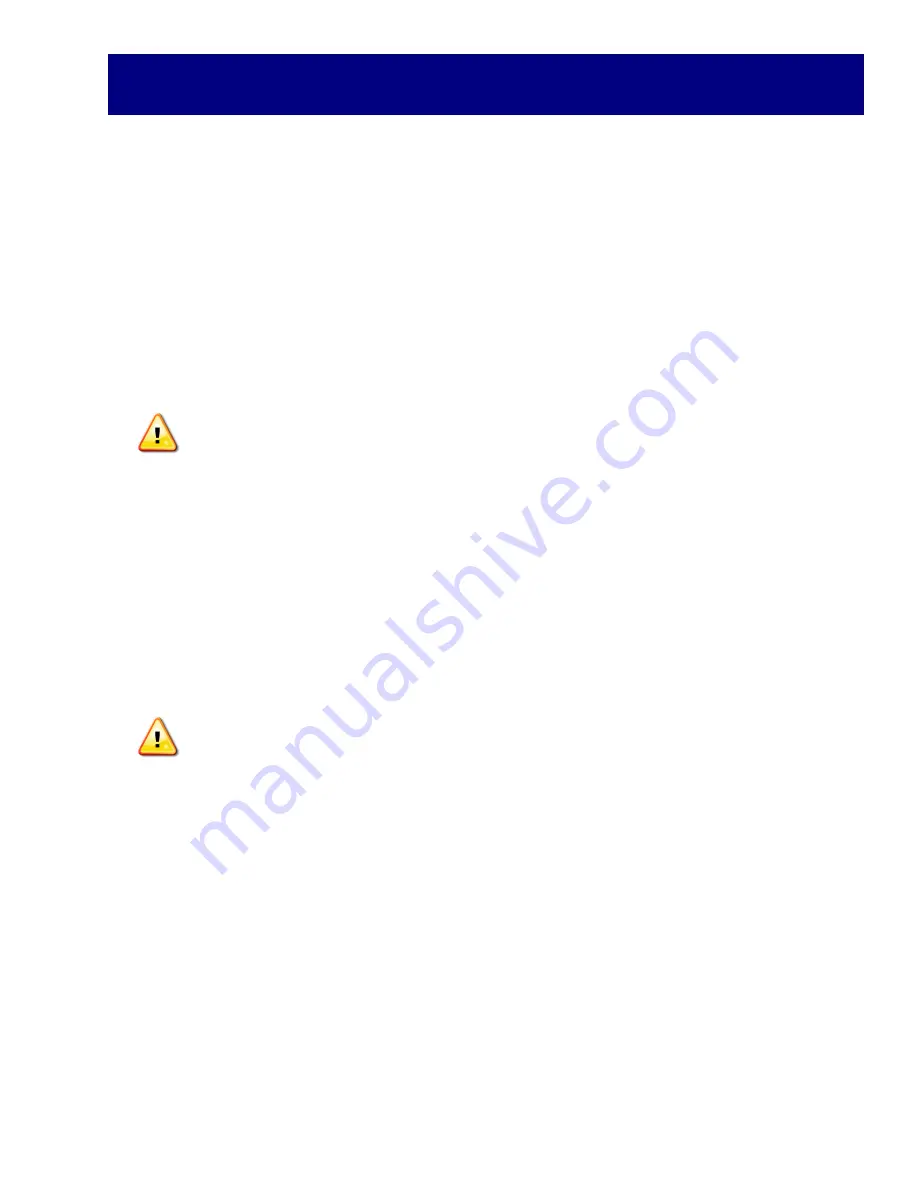
4
Safety is everyone’s responsibility. TRU
-
WELD designs every machine with safety in mind, and a
safe work environment depends largely on you.
Do not install, operate, or repair this equipment without carefully reading this manual and observ-
ing all of the safety precautions mentioned. If there is a question, ask your supervisor!
Safety Symbols
Every effort has been made to protect trained operators from injury or unnecessary risk. Certain
symbols are used throughout this manual to call attention to safety
-
related information and in-
struction. The safety symbols in this manual have these meanings:
This symbol indicates Dangerous Situations. When this symbol is used in this manual,
death or serious bodily harm is possible or probable if the corresponding preventative
measures are not taken. Operators must take caution in the method and manner of
handling or using the machine when this symbol is displayed.
Safety Precautions
Do not install, operate, or repair the SC1100 welding equipment without reading this manual and
all safety precautions stated within!
This machine was designed and built with operator safety in mind, but safety begins with you! Eve-
ry effort has been made to protect the trained operator from injury. Please become familiar with
the information in this manual to minimize the risk of shock or injury.
STUD WELDING CAN BE HAZARDOUS. ALWAYS PROTECT YOURSELF AND OTHERS
FROM POSSIBLE INJURY OR DEATH. KEEP CHILDREN AWAY.
Operators who have a pacemaker should consult with their physician before operating stud weld-
ing equipment.
FUMES and OXYGEN DEPLETION
Only weld in areas or rooms where adequate ventilation of weld gases is possible and where
there is not fire, smoke or explosion hazards.
When working in a confined space always have trained support personnel nearby.
Welding fumes and gases can displace air and lower the oxygen level causing injury or death. Be
sure the breathing air is safe.
Do not weld in locations near degreasing, cleaning, or spraying operations. The heat and rays of
the arcs can react with vapors to form highly toxic and irritating gases.
Do not weld on coated metals, such as galvanized, lead, or cadmium plated steel. The coating
must be removed from the area to be welded. Coatings and metals containing above elements
can generate toxic fumes when heated to welding temperature.
Stud Welding Safety Precautions