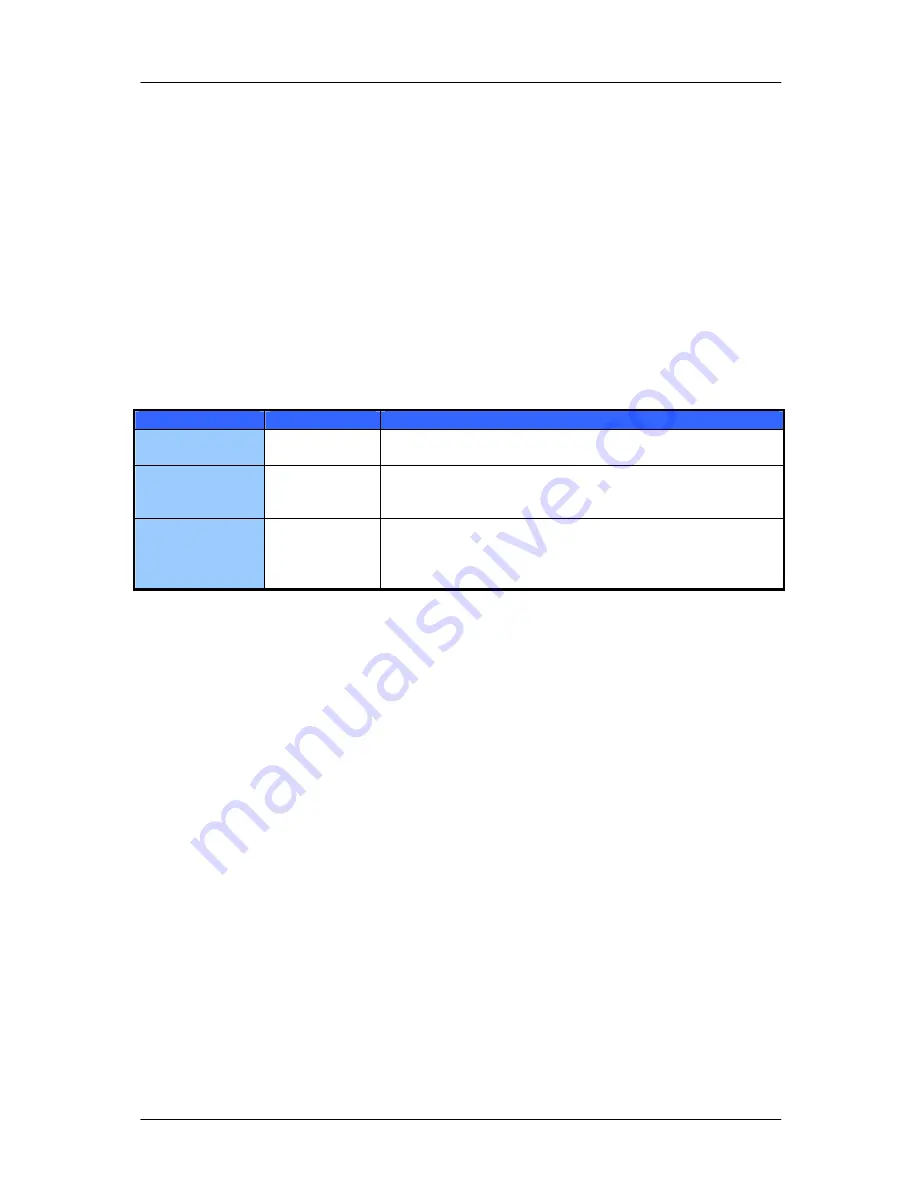
QSH4218 Manual (V1.03 /13-November-2007)
10
Copyright © 2007, TRINAMIC Motion Control GmbH & Co. KG
5.3 Motor Driver Supply Voltage
The driver supply voltage in many applications can not be chosen freely, because other components
have a fixed supply voltage of e.g. 24V DC. If you have to possibility to choose the driver supply
voltage, please refer to the driver data sheet, and consider that a higher voltage means a higher
torque at higher velocity. The motor torque diagrams are measured for a given supply voltage. You
typically can scale the velocity axis (steps / sec) proportionally to the supply voltage to adapt the
curve, e.g. if the curve is measured for 48V and you consider operation at 24V, half all values on the
x-Axis to get an idea of the motor performance.
For a chopper driver, consider the following corner values for the driver supply voltage (motor
voltage). The table is based on the nominal motor voltage, which normally just has a theoretical
background in order to determine the resistive loss in the motor.
Comment on the nominal motor voltage:
U
COIL_NOM
= I
RMS_RATED
* R
COIL
(Please refer to motor technical data table.)
Parameter
Value
Comment
Minimum driver
supply voltage
2 * U
COIL_NOM
Very limited motor velocity. Only slow movement without
torque reduction. Chopper noise might become audible.
Optimum driver
supply voltage
≥
4 * U
COIL_NOM
and
≤
22 * U
COIL_NOM
Choose the best fitting voltage in this range using the motor
torque curve and the driver data. You can scale the torque
curve proportionally to the actual driver supply voltage.
Maximum rated
driver supply
voltage
25 * U
COIL_NOM
When
exceeding this value, the magnetic switching losses in
the motor reach a relevant magnitude and the motor might
get too hot at nominal current. Thus there is no benefit in
further raising the voltage.
Table 5.2: Driver supply voltage considerations
Hints:
Q: How to determine if the given driver voltage is sufficient?
A1:
Just listen to the motor at different velocities. Does the “sound” of the motor get raucous or
harsh when exceeding some velocity? Then the motor gets into a resonance area. The reason is,
that the motor back-EMF voltage reaches the supply voltage. Thus, the driver can not bring the full
current into the motor any more. This is typically a sign, that the motor velocity should not be
further increased, because resonances and reduced current affect motor torque.
A2:
Measure the motor coil current at maximum desired velocity.
For microstepping: If the waveform is still basically sinusoidal, the motor driver supply voltage is
sufficient.
For Fullstepping: If the motor current still reaches a constant plateau, the driver voltage is sufficient.
If you determine, that the voltage is not sufficient, you could either increase the voltage or reduce
the current (and thus torque).
5.4 Back EMF (BEMF)
Within SI units, the numeric value of the BEMF constant has the same numeric value as the numeric
value of the torque constant. For example, a motor with a torque constant of 1 Nm/A would have a
BEMF constant of 1V/rad/s. Turning such a motor with 1 rps (1 rps = 1 revolution per second =
6.28 rad/s) generates a BEMF voltage of 6.28V.