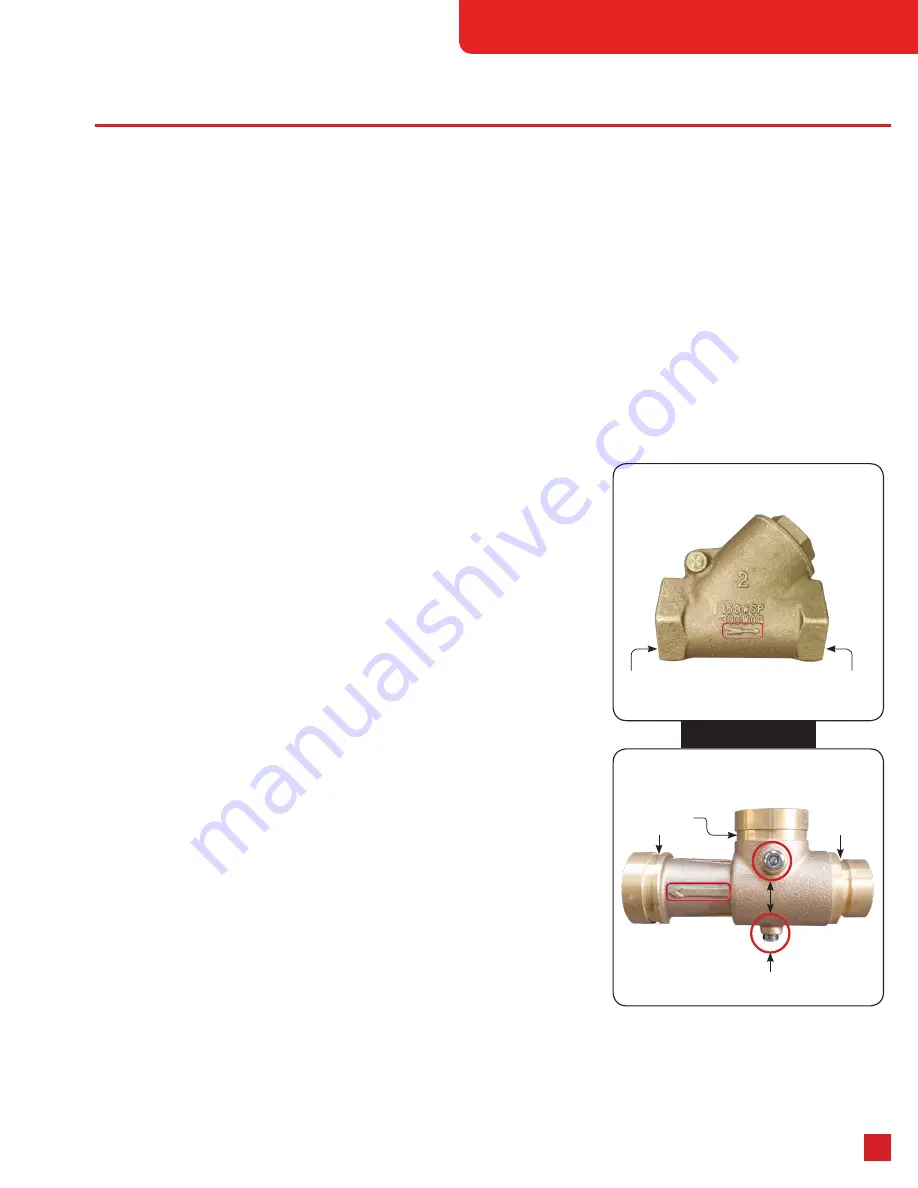
(
215-293-0700
7
215-293-0701
3
Technical Manual
Class B Foam System
Installation Instructions
Eductor
(
Please refer to the
Plumbing Diagram
,
Figure 4
on
Page 6
)
Mount the eductor in a 2"
[50 mm]
diameter line from the discharge side of the fire pump with a 2"
[50 mm]
ball shut-off valve upstream
of the eductor. The discharge side of the eductor is plumbed with 2"
[50 mm]
piping back to the suction side of the fire pump. Observe
the flow direction arrow on the eductor for proper placement.
Foam Concentrate Metering Valve
A 2" metering valve can be mounted to an enclosed pump panel or directly into the piping with access to the pump operator. If mounted
to an enclosed pump panel, piping connections to the valve must be properly supported – see valve mounting hole pattern
Figure 3
on
Page 5
. Supply the inlet side of the metering valve with 2"
[50 mm]
plumbing from the foam concentrate tank. This line
must include a 2"
[50 mm]
foam tank ball shut-off valve. 2"
[50 mm]
plumbing connects the discharge side of the metering valve to the
eductor. Details of the metering valve internals are shown
Figure 5
on
Page 9
.
This Line Must Include a 2"
[50 mm]
Check Valve (supplied
with the kit) to prevent back flow of water to the foam concentrate tank.
NOTE
: The swing check valve must be mounted in a horizontal position and in the correct direction for proper operation.
External Foam Concentrate Connection
A 2"
[50 mm]
valved hose connection can be provided at the pump panel to allow an external foam concentrate supply from drums, pails,
etc. See
Page 7
for optional auxiliary foam concentrate pickup hose and pickup tubes.
Flushing Piping
Piping of 2"
[50 mm]
diameter is to be installed between the water inlet connection of
the eductor and foam concentrate inlet of the metering valve as a means to flush both
the metering valve and eductor after each use. This plumbing must include a 2"
[50
mm]
ball shut-off valve.
Schematic/Instruction Chart
A backing plate is supplied for the schematic/instruction plate and must be mounted in
close proximity to the foam metering valve.
Refer to
Figure 2
on
Page 5
for the mounting hole dimensions.
Plumbing Requirements
NOTE
: The design of the Metering Valve and Eductor are not intended to support
the weight of the 2"
[50 mm]
plumbing. Piping to and from the Eductor and Foam
Metering Valve must be properly supported.
Foam metering valve and all of the 2"
[50 mm]
ball shut-off valves in the system
must be accessible to the pump operator.
Refer to
Figure 3
on
Page 5
for the mounting hole dimensions for the
Metering
Valve
Backing Plate
.
Observe that the cast in arrows in the red rectangles in
Figure 1
on the Check
Valve and Eductor are installed in the manner as shown in the plumbing diagram
Figure 4
on
Page 6
.
The eductor features two (2)
1
⁄
4
" NPT pipe plugs shown in the red circles in
Figure
1
for use as drain points based on the orientation of the eductor. All other plumbing
connections on the eductor are VIC pipe grooved ends.
Plumbing Recommendations
(Also Refer to top of
Page 7
)
Install a valved direct water tank fill line to keep the on-board water tank filled
from hydrant or nurse tanker. With this feature the foam system can be used
continuously from the on-board water tank greatly simplifying the 5 PSI inlet pump
pressure restriction.
Install a valved external auxiliary foam inlet connection at the pump panel to
supplement the on-board foam tank. With this feature, using a pick-up tube, a different type of foam concentrate can be used from
that of the on-board tank. It also eliminates the need to fill the on board foam cell during an extended operation by supplying foam
concentrate directly from containers on the ground. Also, with this auxiliary foam inlet and pick-up tube, foam system training
can be done simply utilizing a container on the ground filled with water; operators can see how the system draws water based on
different metering valve settings.
▲
Figure 1
▼
2" FNPT
[50 mm]
2" VIC
[50 mm]
1
1
⁄
2
" VIC
[38 mm]
1
⁄
4
" NPT
[7.1mm]
2" FNPT
[50 mm]