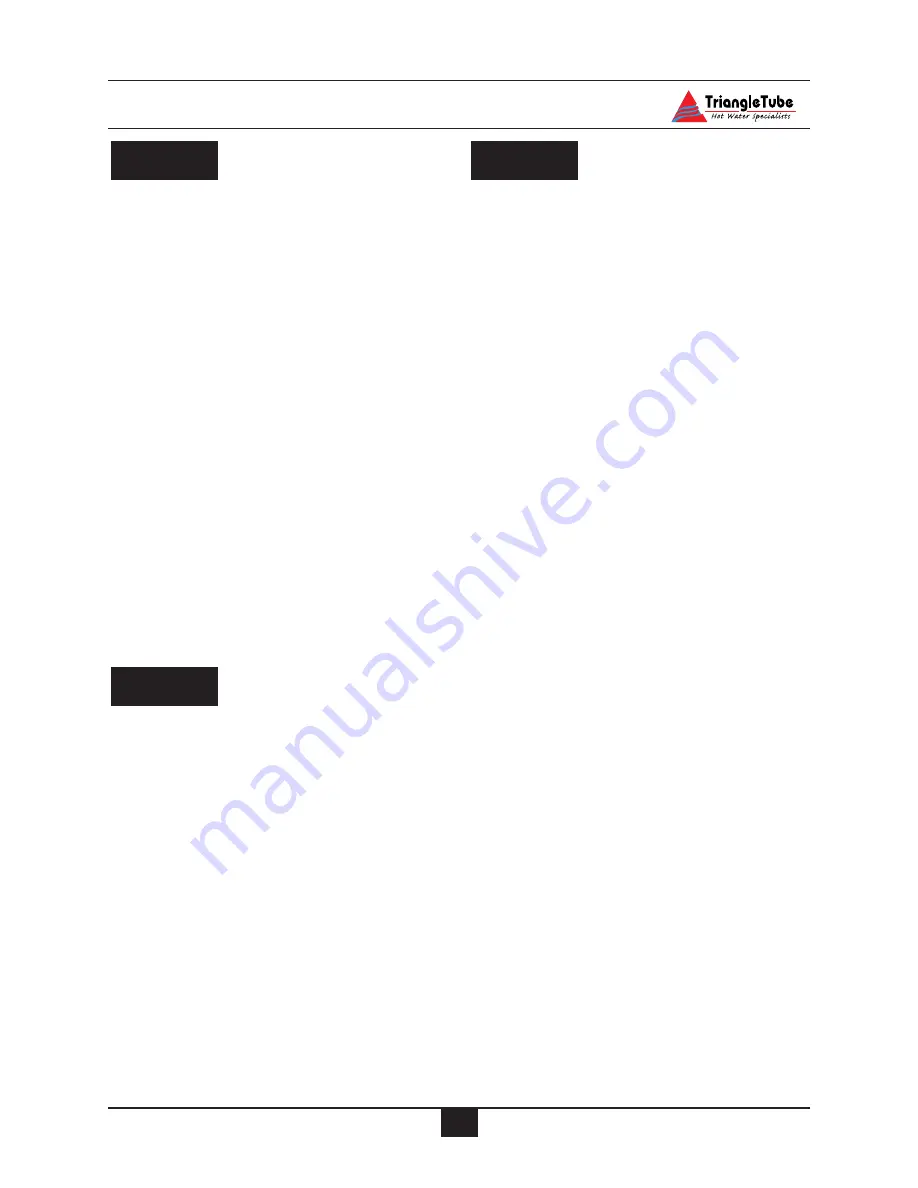
9
Domestic Piping
Failure to properly direct the discharge
piping of the T&P relief valve may result
in flooding of the area adjacent to the
appliance and/or lower floors in the
structure causing substantial property
damage.
The installer
must not
install the T&P
relief valve discharge piping in a manner
that is:
•
Excessively long: Using more than 2
elbows and/or 15 feet of discharge pip-
ing can reduce the discharge capacity.
•
Terminated directly into a drain: The
discharge piping must terminate within
6 inches of the drain. Check with local
plumbing codes for termination guide-
lines.
•
The discharge piping is plugged, reduced
in size or restricted in any manner.
•
The discharge piping is subject to
freezing.
DO NOT install any valves between the
T&P relief valve and the discharge pip-
ing. DO NOT plug the T&P relief valve
or the discharge piping. Improper place-
ment and piping of the T&P relief valve
can cause severe personal injury, death
or substantial property damage.
Thermostatic Mixing Valve
The MODULATING DELTA contains a facto-
ry equipped thermostatic mixing valve with
built-in check valve. The operating range of the
thermostatic mixing is 90ºF to 120ºF.
For applications with a domestic recirculation
loop, the recirculation pump should be con-
trolled by an aquastat. The maximum recom-
mended setting of the aquastat is 10ºF lower
than the thermostatic mixing valve setting.
For proper operation of the thermostatic
mixing valve and to prevent potential
scalding hazards, the recirculation loop
should be controlled by an aquastat. DO
NOT use continuous recirculation or
timers.
Mixing Valve Installation
1. Remove the jacket top panel by pushing up
on the corners.
2. Remove the mixing valve from the carton
located inside the front control cover.
3. Apply pipe dope to the male threads locat-
ed on the “H” (hot) side of the mixing valve
and the internal threads of the domestic hot
water supply tee.
4. Thread the “H” side of the mixing valve in
to the domestic hot water supply tee, align
valve and tighten using two wrenches to
avoid pipe damage.
Domestic Cold Water Supply Piping
Assembly Installation
1. Locate the domestic cold water supply pip-
ing assembly at the top of the appliance.
2. Apply pipe dope to the male threads of the
domestic cold water supply piping assembly
and the internal threads of the cold water
supply tee.
3. Thread the domestic cold water supply pip-
ing assembly in to the domestic cold water
supply tee, align the branch with the
domestic system piping and tighten using
two wrenches to avoid pipe damage.
U-Tube Assembly
The MODULATING DELTA is supplied
with a U-Tube Assembly that directs cold
water to the thermostatic mixing valve.
To install the U-Tube Assembly the
installer must:
DANGER
WARNING
CAUTION