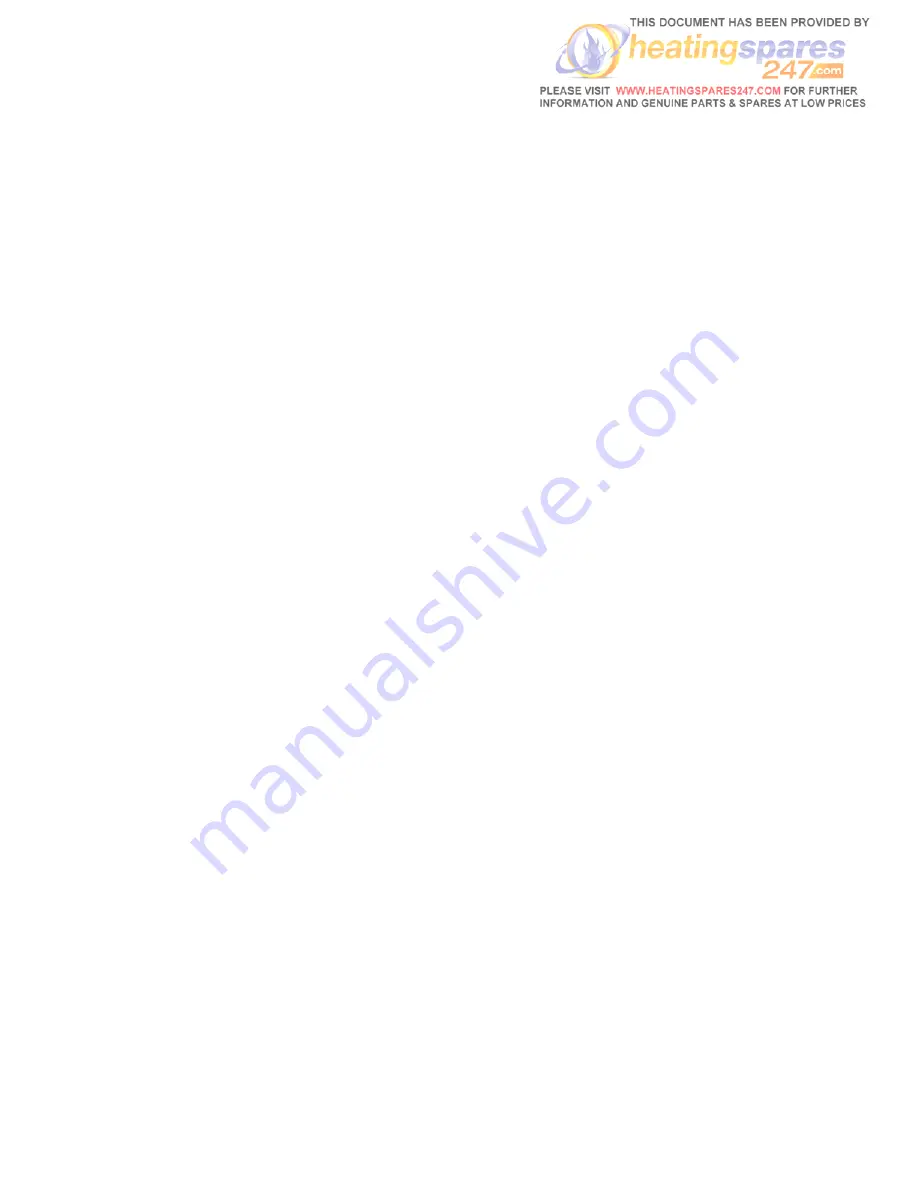
3
TRIANCO
CUSTOMER AFTER SALES SERVICE INFORMATION
SERVICE CENTRE AND TECHNICAL SUPPORT
Tel: 0114 257 2300 Fax: 0114 257 2338
Hours of business Monday to Thursday 8.30am - 4.45pm
Friday 8.30am - 2.30pm
A step by step guide to reporting a fault
with your appliance
A qualified field SERVICE ENGINEER is available to
attend a breakdown or manufacturing fault occurring
whilst the appliance is under guarantee.
The appliance must be made available for service during
normal working hours, Monday to Friday (no weekend
work is accepted).
A charge will be made where:
•
Our Field Service Engineer finds no fault with the
appliance
or
•
The cause of a breakdown is due to other parts of the
plumbing/heating system (including oil line/lack of
oil), or with equipment not supplied by Trianco.
or
•
Where the appliance falls outside the guarantee
period (see terms and conditions enclosed).
or
•
The appliance has not been correctly installed,
commissioned or serviced as recommended (see
commissioning, installation and servicing
instructions)
or
•
The breakdown occurs immediately following an
annual service visit. In this instance your appointed
Service Agent must check all his work PRIOR to
requesting Trianco to attend.
NOTE: Burner nozzles are currently guaranteed
until the first service.
Over 50% of all service calls made are
found to have no appliance fault.
What to do in the event of an appliance
fault or breakdown:
Step 1:
Always contact your installer or commissioning
engineer in the first instance, who must
thoroughly check all his work PRIOR to
requesting a service visit from Trianco.
Step 2:
If your appliance has developed an in-guarantee
fault your installer should contact Trianco
Service Centre for assistance.
What happens if my installer/engineer is
unavailable?
Step 3:
Contact Trianco Direct. We will provide you with
the name and telephone number
of our
Service Agent. However, a charge may apply if
the fault is not covered by the appliance
guarantee (payment will be requested on site by
our independent Service Agent).
PLEASE NOTE:
Unauthorised invoices for attendance and repair work
carried out on this appliance by any third party will not be
accepted by Trianco.