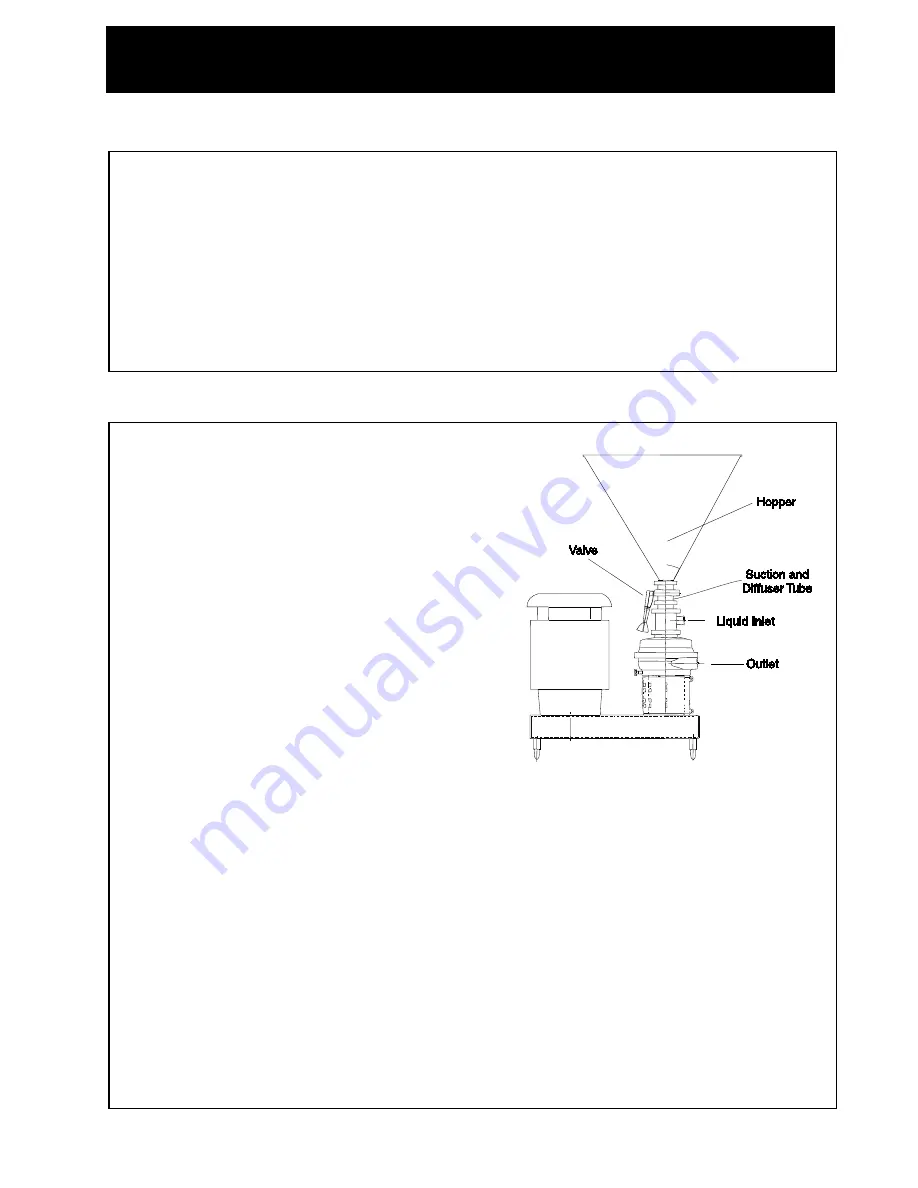
5
INTRODUCTION
DESCRIPTION
The Dual Stage Tri-Blender consists of two basic sections, the dry material section and the liquid
material section.
The Dual Stage Tri-Blender is mounted on a base plate. It is mounted adjacent to the drive motor
and is driven by belts running between pulleys under the base plate. The manually controlled
Butterfly valve is standard equipment.
On this model, the connection ends, the diffuser and the suction tube, the inlet adapter, the casing,
screens, washer, the impellers and backplate are made of 316 stainless steel. The hopper is made of
304 stainless steel. All of the tubes are fastened with quick couple Tri-Clamps for easy care and fast
access. The four legs supporting the Tri-Blender are adjustable for easy leveling of the blender during
installation.
BASIC OPERATION
The Tri-Blender basically consists of a centrifugal pump
head and impeller mounted so that the normal suction
port, or inlet, is pointed upward. The inlet piping
consists of a patented tube-within-a-tube arrangement.
This serves to keep the liquid and dry ingredients
separated until they are in the mixing chamber. The
tube-within-a-tube arrangement eliminates prewetting,
one of the major problems of wet-dry mixing.
Our patented (U.S. Patent # 4,850,704) dual stage Tri-
Blender incorporates the proven design characteristics
of our popular Single Stage Tri-Blender, but takes the
concept a step further for even more efficiency.
The Dual Stage concept provides for "double blending."
The product passes through the initial liquid/dry
ingredient blending chamber directly below to a
secondary chamber, which effectively acts as a
discharge pump.
Due to its close proximity, the dual (or second) chamber concept actually increases, rather than
decreases vacuum. The vacuum from the suction of the second pumping stage is added to that of
the first stage, greatly improving product addition rates. The "double blend" feature improves end
product consistency, providing a smoother, more uniform blend.
With the Dual Stage, in applications up to 500 CPS and up to 50 feet (15m) of discharge head, no
discharge pump is required. This is a significant improvement over the Single Stage units, which
normally require an auxiliary discharge pump at 25 feet (7.5m) of discharge head and above. On
some applications with higher CPS, a discharge pump may be necessary.
By incorporating the discharge pump function into the blender itself, you can achieve e significantly
higher vacuum rates over a wider range of process conditions. The increased vacuum provides for
fast, consistent product flow rates with no drop-off through your entire production run.
Содержание DS3218
Страница 1: ...TB DS SM 97 Tri Clover DualStageTri Blender Model DS3218 Service Installation Manual ...
Страница 2: ...2 ...
Страница 19: ...19 EXPLODED VIEW ...