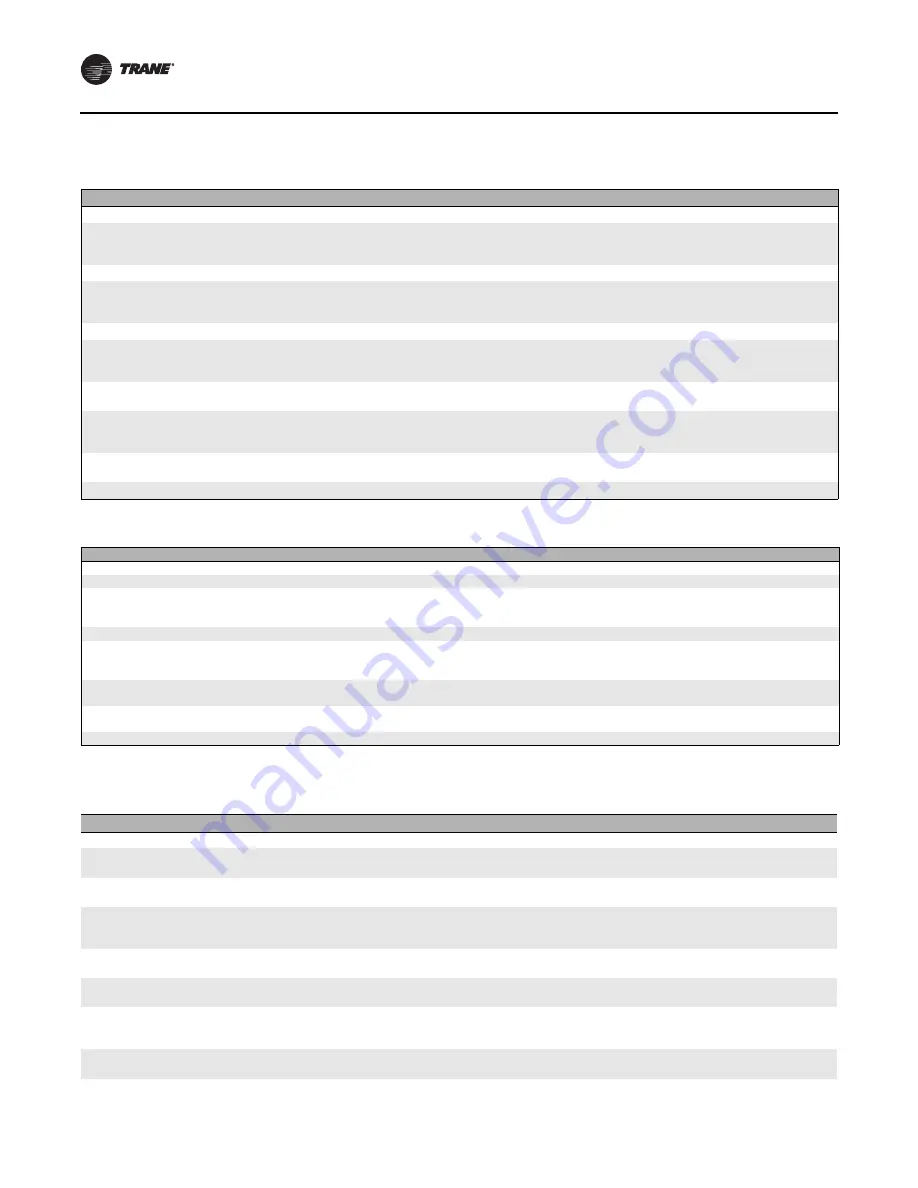
Diagnostics and Troubleshooting
142
UNT-SVX07J-EN
Valves with ZN010, ZN510, or ZN520 Controllers
Table 80. Valves remain closed
Probable Cause
Explanation
Normal operation
The controller opens and closes the valves to meet the unit capacity requirements.
Requested mode: off
It is possible to communicate the operating mode (such as off, heat, and cool) to the controller. When off is
communicated to the controller, the unit controls the fan to off. The unit is not capable of heating or cooling
when the controller is in this mode.
Valve override
The controller can communicate a valve override request.This request affects the valve operation.
Manual output test
The controller includes a manual output test sequence to verify analog and binary output operation and the
associated wiring. However, based on the current step in the test sequence, the valves may not be open. Refer
to the
.
Diagnostic present
A specific list of diagnostics affects valve operation. For more information, see
Sampling logic
The controller includes entering water temperature sampling logic that automatically invokes during 2-pipe
or 4-pipe changeover. It determines when the entering water temperature is either too cool or too hot for the
desired heating or cooling mode. Refer to
“Water Temperature Sampling Function,” p. 104
Unit configuration
The controller must be properly configured based on the actual installed end devices and application. When
the unit configuration does not match the actual end device, the valves may not work correctly.
No power to the controller
If the controller does not have power, the unit fan does not operate. For the Tracer
®
ZN010, ZN510 controller
to operate normally, it must have an input voltage of 24 Vac. When the green LED is off continuously, the
controller does not have sufficient power or has failed.
Unit wiring
The wiring between the controller outputs and the valve(s) must be present and correct for normal valve
operation. Refer to the unit wiring diagrams on the unit.
Valve configuration
For modulating valves, ensure the stroke time is set correctly. Refer to
Table 81.
Valves remain open
Probable Cause
Explanation
Normal operation
The controller opens and closes the valves to meet the unit capacity requirements.
Valve override
The controller can communicate a valve override request to affect the valve operation.
Manual output test
The controller includes a manual output test sequence that verifies analog and binary output operation and
the associated wiring. However, based on the current step in the test sequence, the valves may be open. Refer
to the
Diagnostic present
A specific list of diagnostics affects valve operation. For more information, see
and
.
Sampling logic
The controller includes entering water temperature sampling logic that automatically invokes during 2-pipe or
4-pipe changeover to determine if the entering water temperature is correct for the unit operating mode. Refer
to
“Water Temperature Sampling Function,” p. 104
.
Unit configuration
The controller must be properly configured based on the actual installed end devices and application. When
the unit configuration does not match the actual end device, the valves may not work correctly.
Unit wiring
The wiring between the controller outputs and the valve(s) must be present and correct for normal valve
operation. Refer to the unit wiring diagrams on the unit.
Valve configuration
For modulating valves, ensure the stroke time is set correctly. Refer to
Electric Heat with ZN010, ZN510, or ZN520 Controllers
Table 82. Electric heat not operating
Probable Cause
Explanation
Normal operation
The controller cycles electric heat on and off to meet the unit capacity requirements.
Requested mode: off
It is possible to communicate the operating mode (such as off, heat, cool) to the controller. When off is
communicated to the controller, the units shuts off the electric heat.
Communicated disable
Numerous communicated requests may disable electric heat, including an auxiliary heat enable input and the heat/
cool mode input. Depending on the state of the communicated request, the unit may disable electric heat.
Manual output test
The controller includes a manual output test sequence that verifies analog and binary output operation and
associated output wiring. However, based on the current step in the test sequence, the electric heat may not be
on. Refer to
“Manual Output Test,” page 138
Diagnostic present
A specific list of diagnostics affects electric heat operation. For more information, see
.
Unit configuration
The controller must be properly configured based on the actual installed end devices and application. When the
unit configuration does not match the actual end device, the electric heat may not work properly.
No power to the controller
If the controller does not have power, electric heat does not operate. For the controller to operate normally, a 24 Vac
input voltage must be applied. When the green LED is off continuously, the controller does not have sufficient power
or has failed.
Unit wiring
The wiring between the controller outputs and the electric heat contacts must be present and correct for normal
electric heat operation. Refer to the unit wiring diagrams on the unit.
ECM motor/Motor control
board failure
ECM controls include sophisticated fan proving / interlock circuitry that will disable electric heat if one or more
motors are not performing normally
Содержание UniTrane
Страница 163: ......