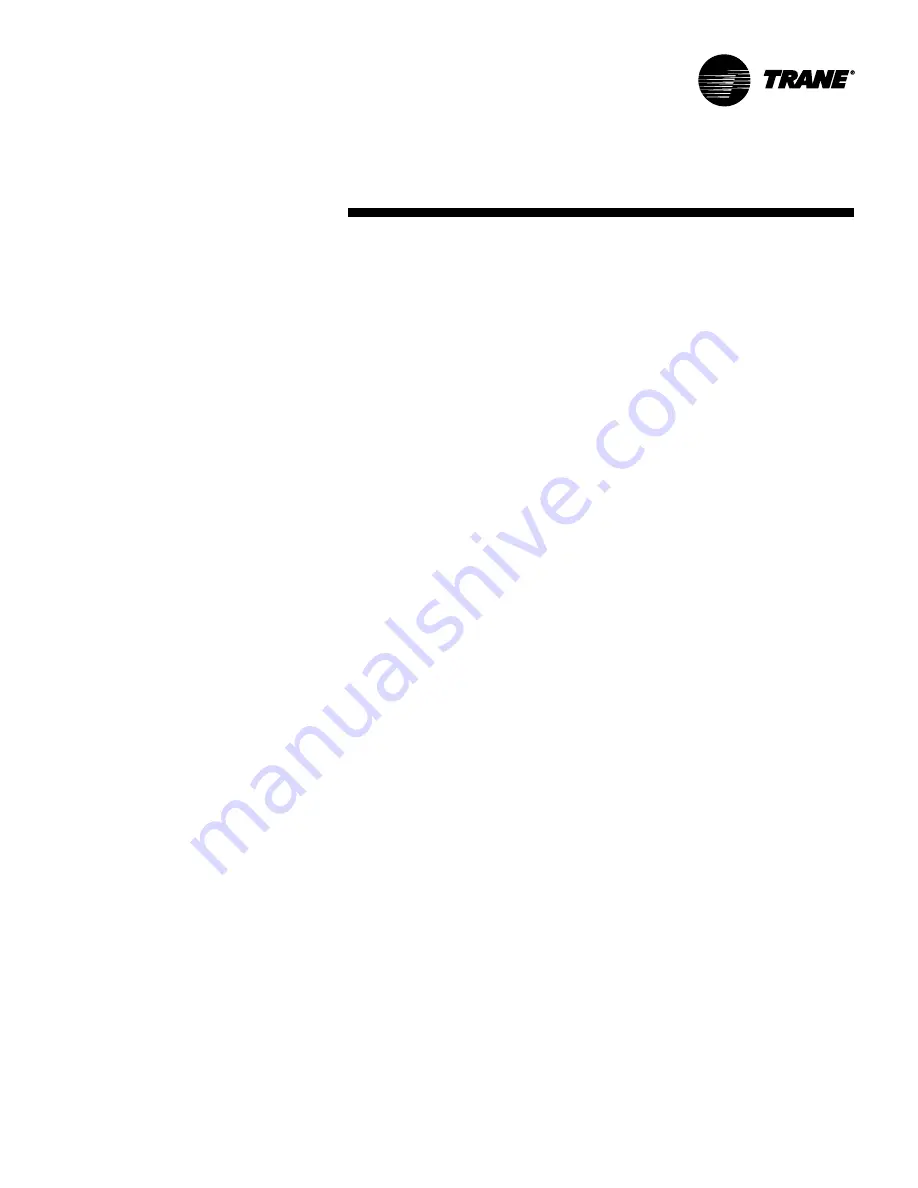
101
RT-PRC010-EN
Mechanical
Specifications
Standard filters provided shall be two-
inch thick throwaway glass fiber filter,
30 percent efficient mounted in a metal
rack.
Permanent cleanable wire mesh option
Shall be washable permanent wire mesh
with metal frame.
High efficiency throwaway option
Shall be two-inch high efficiency media
filters with average dust spot efficiency
of 25-35 percent and an average
arrestance in excess of 90 percent when
tested in accordance with ASHRAE 52-
76.
90-95 percent bag filter option
Shall have glass fiber media mounted in
a galvanized steel frame. These Class 1
single piece disposable bag filters shall
have a 90-95% dust spot efficiency rating
per ASHRAE 52-76. To ensure maximum
bag filter life two-inch prefilters shall be
included with the bag filters.
90-95 percent cartridge filter option
Twelve-inch deep cartridge filters shall
be mounted in a galvanized steel frame.
Filters shall be Class 1 listed by
Underwriters Laboratories and have a
90-95% dust spot efficiency per ASHRAE
52-76. To ensure maximum cartridge
filter life, two-inch prefilters shall be
provided.
Exhaust Air
General
Return air options shall include no relief,
barometric relief, 50 percent exhaust fan,
100 percent modulating exhaust fan and
100 percent modulating exhaust fan with
direct space building pressurization
control.
No Relief (standard)
Relief air opening shall be sealed with
panel and made watertight.
Barometric relief option
Gravity dampers shall open to relieve
positive pressure in the return air section
of the rooftop. Barometric relief dampers
shall relieve building overpressurization,
when that overpressurization is great
enough to overcome the return duct
pressure drops.
50 percent exhaust air fan option
One, double inlet, forward-curved fan
shall be mounted rigidly to base with
fixed sheave drive. Fan shall be
dynamically balanced and tested in
factory. Unit shall reach rated rpm before
fan shaft passes through first critical
speed. Fan shaft shall be mounted on
two grease lubricated ball bearings
designed for 200,000 hours average life.
Optional extended grease lines shall
allow greasing of bearings from unit
filter section. Barometric dampers at fan
outlet shall prevent air backdraft. Fifty
percent exhaust fan shall be an on/off
control based on economizer OA
damper position. All exhaust fan motors
meet the U.S. Energy Policy Act of 1992
(EPACT).
Modulating 100 percent exhaust air fan
option
Two, double-inlet, forward-curved fans
shall be mounted on a common shaft
with fixed sheave drive. All fans shall be
dynamically balanced and tested in
factory before being installed in unit.
Exhaust fan shall be test run in unit as
part of unit test. Unit shall reach rated
rpm before fan shaft passes through first
critical speed. Fan shaft shall be
mounted on two grease lubricated ball
bearings designed for 200,000-hour
average life. Optional extended grease
lines shall be provided to allow
greasing of bearings from unit filter
section. Fan motor and assembly shall
be mounted on common base to allow
consistent belt tension with no relative
motion between fan and motor shafts.
On motor sizes larger than five hp
entire assembly shall be completely
isolated from unit and fan board by
double deflection, rubber in shear
isolators or spring isolation. Discharge
dampers at unit outlet shall modulate
exhaust airflow in response to OA
damper position. All exhaust fan motors
meet the U.S. Energy Policy Act of 1992
(EPACT).
Modulating 100 Percent Exhaust Fan
with Statitrac™ Control Option
Two, double-inlet, forward-curved fans
shall be mounted on a common shaft
with fixed sheave drive. All fans shall be
dynamically balanced and tested in
factory before being installed in unit.
Exhaust fan shall be test run as part of
unit final run test. Unit shall reach rated
rpm before fan shaft passes through first
critical speed. Fan shaft shall be
mounted on two grease lubricated ball
bearings designed for 200,000-hour
average life. Optional extended grease
lines shall be provided to allow greasing
of bearings from unit filter section. Fan
motor and assembly shall be mounted
on common base to allow consistent
belt tension with no relative motion
between fan and motor shafts. Entire
assembly shall be completely isolated
from unit and fan board by double
deflection, rubber in shear isolators or
spring isolation on motor sizes larger
than five hp. For both CV and VAV
rooftops, the 100 percent modulating
exhaust discharge dampers (or VFD)
shall be modulated in response to
building pressure. A differential pressure
control system, (Statitrac™), shall use a
differential pressure transducer to
compare indoor building pressure to
outdoor ambient atmospheric pressure.
The FC exhaust fan shall be turned on
when required to lower building static
pressure setpoint. The (Statitrac™)
control system shall then modulate the
discharge dampers (or VFD) to control
the building pressure to within the
adjustable, specified dead band that
shall be adjustable at the Human
Interface Panel. All exhaust fan motors
meet the U.S. Energy Policy Act of 1992
(EPACT).