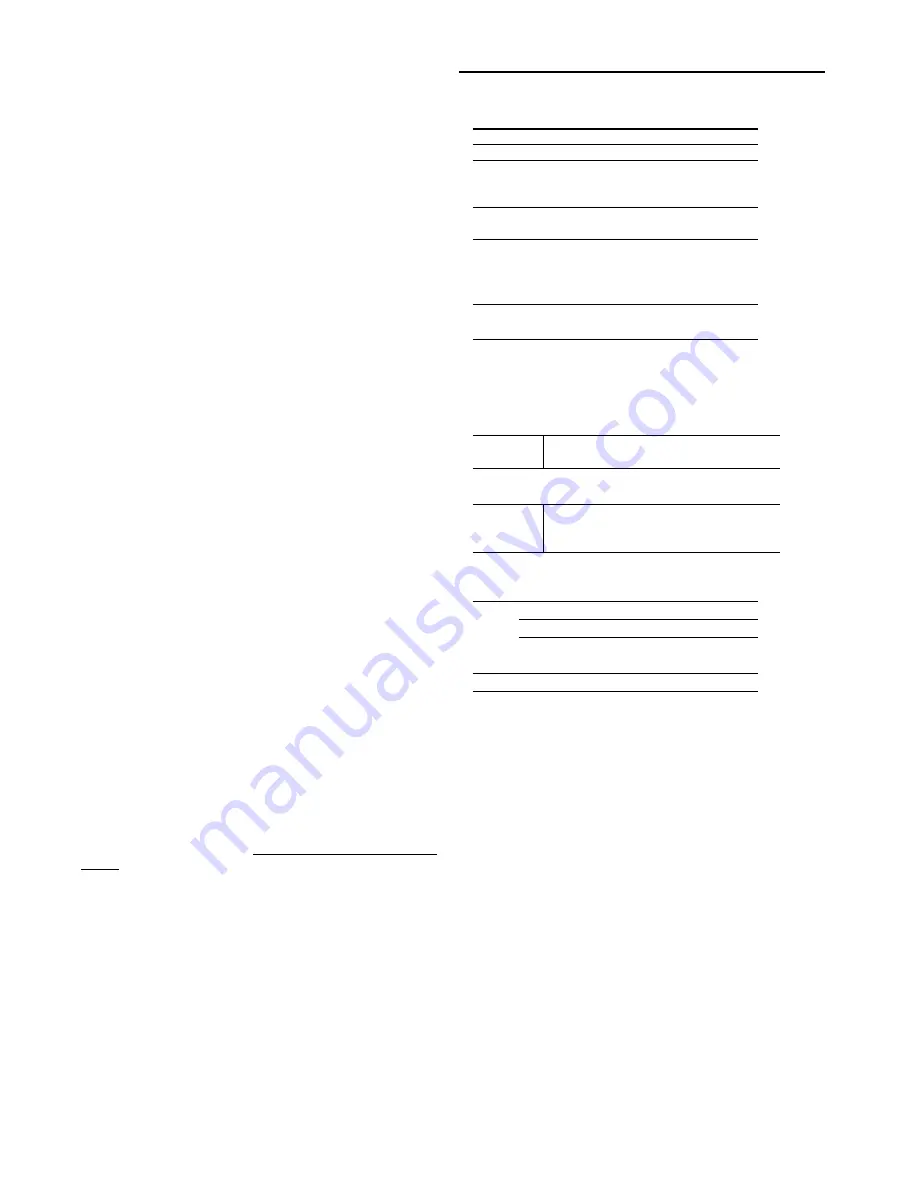
55
Table 5-2
Pressure Control Settings
Pressure Switch
Make
Break
Hi Pressure
350 psi
405 psi
Lo Pressure
EVPB
60 psi
45 psi
All others
40 psi
30 psi
Condenser Fan
Cycling Switch
275 psi
155 psi
(EVP Only w/HGB - wo/HGB)
Std.
Low Ambient
Thermostat
33
o
F
30
o
F
Compressor
Winding T-Stat
181
o
F
221
o
F
Note: Pack Stock units will have both
low pressure switches shipped and the
user should use the above valves that apply.
Table 5-3
Recommended Refrigerant Capacities
Capacity
Total Interconnecting Line Length
50 100 150
Approximate Total System Refrigerant Charge
(Lbs. Per Circuit)
80 Ton
92 107 150
100 Ton
108 131 155
120 Ton
134 157 183
Table 5-4
Minimum Starting Ambient Temperature
Minimum Starting Ambient (1)
Standard Units Low Ambient Units
Unit
With
No
With
No
Size
HGBP
HGBP
HGBP
HGBP
80-120
45°
40°
10°
0°
Note :
1. Minimum starting ambients in degrees F and
is based on the unit operating at minimum
step of unloading and 5 mph wind across
condenser.
d. Subtract the saturated vapor temperature (converted
in c), from the actual suction line temperature
(measured in b). The difference between the two
temperatures is known as “superheat”.
12. Verify that the oil level in each compressor is correct.
The oil level may be down to the bottom of the sight
glass but should never be above the sight glass.
13. Once the checks and adjustments for the operating cir-
cuit has been completed, check and record the:
ambient temperature;
compressor oil level (each circuit);
compressor suction and discharge pressures (each
circuit);
superheat and sub-cooling (each circuit);
Record this data on an “operator’s maintenance log”
shown in Table 5-8. Repeat these procedures for the
second refrigeration circuit, if applicable.
14. Turn the 115-volt control circuit switch 1S2 to the “OFF”
position and open the field provided or optional factory
mounted disconnect switch.
15. After shutting the system off, check the compressor oil
appearance. Discoloration of the oil indicates that an ab-
normal condition has occurred. If the oil is dark and
smells burnt, it has overheated because:
1. Compressor is operating at an extremely high
condensing temperature;
2.
High superheat;
3.
A compressor mechanical failure or motor burnout
has occurred.
If the oil is black and contains metal flakes, a
mechanical failure has occurred. This symptom is
often accompanied by a high compressor
amperage draw.
If a motor burnout is suspected, use an acid test kit
to check the condition of the oil. Test results will
indicate an acid level exceeding 0.05 mg KOH/g if
a burnout occurred.
Compressor Oil
The scroll compressor uses Trane OIL-42 without substi-
tution. The appropriate oil charge for a 9 and 10 Ton scroll
compressor is 8.5 pints. For a 14 and 15 Ton scroll com-
pressor, use 13.8 pints.
Compressor Crankcase Heaters
9 and 10 ton scroll compressors have a 100-watt heater
installed. 14 and 15 ton scroll compressors have two 80-
watt heaters installed per compressor.
System Start-Up (Continued)
Содержание RAUC-IOM-15
Страница 8: ...8 Figure 3 2A RAUC C80 Unit Dimensional Data Recommended Clearances...
Страница 9: ...9 Figure 3 2A Continued RAUC D10 Unit Dimensional Data Recommended Clearances...
Страница 10: ...10 Figure 3 2A Continued RAUC D12 Unit Dimensional Data Recommended Clearances...
Страница 11: ...11 Figure 3 2B EVPB C80 Evaporator Chiller Dimensions...
Страница 12: ...12 Figure 3 2B Continued EVPB D10 Evaporator Chiller Dimensions...
Страница 13: ...13 Figure 3 2B Continued EVPB D12 Evaporator Chiller Dimensions...
Страница 14: ...14 Figure 3 2B Continued EVPB C80 through D12 Chill Water Pipe Stubout Dimensions...
Страница 35: ...35 Installation Continued Field Connection Diagram Notes for all System Control Options...
Страница 57: ...57 Figure 5 5 Typical Scroll Compressor Terminal Block System Start Up Continued...
Страница 67: ...67...
Страница 68: ...68...