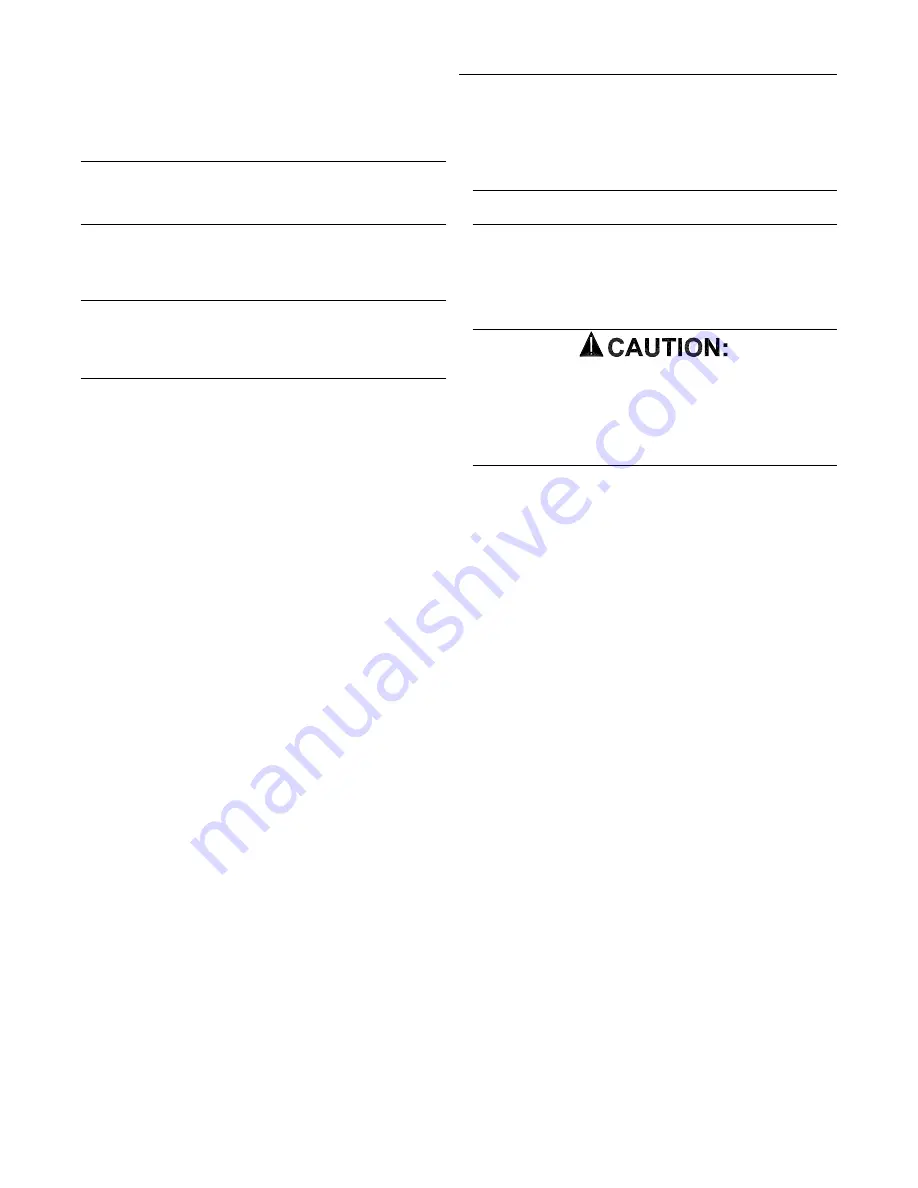
20
Installation (Continued)
Leak Testing Procedure
When Leak-testing a refrigerant system, observe all safety
precautions.
Note: Never use oxygen, acetylene or compressed
air for leak testing. Always install a pressure
regulator, shutoff valves and gauges to control
pressure during leak testing.
Trane condensing units are shipped with a Nitrogen hold-
ing charge. If there is no pressure, the unit must be leak
tested to determine the location of leak as follows:
Note: These service procedures require working
with refrigerant, Do NOT release refrigerant to the
atmosphere! The service technician must comply
with all federal, state, and local laws. Refer to
general service bulletin MSCU-SB-1 (latest edition).
Use refrigerant gas as a tracer for leak detection and use
oil-pumped dry nitrogen to develop the required test pres-
sure. Test the high and low side of the system at pressures
dictated by local codes.
1. Close the field supplied liquid line service valve(s) in-
stalled near the evaporator and the compressor dis-
charge service valve to isolate the system's high side
from the low side. Pressure test the liquid line, discharge
line, and condenser coils at pressures dictated by local
codes. Do not exceed 10# above the pressure control
settings.
2. Connect a refrigerant cylinder to the charging port of the
liquid line service valve. Use the refrigerant to raise the
high side pressure to 12 to 15 psig.
3. Disconnect the refrigerant cylinder. Connect a dry nitro-
gen cylinder to the charging port and increase the high
side pressure. Do not exceed the condenser maximum
working pressure listed on the unit nameplate.
4. Use a halide torch, halogen leak detector or soap
bubbles to check for leaks. Check all piping joints,
valves, etc...
5. If a leak is located, use proper procedures to remove the
refrigerant/nitrogen mixture, break the connection and re-
make as a new joint. Retest for leaks after making re-
pairs.
6. Repeat the test procedure for the low side of the system,
charging through the suction pressure gauge port or
through an access provided on the suction line by the in-
staller. Increase the system pressure to 100 psig.
7. If a leak is located, use proper procedures to remove the
refrigerant/nitrogen mixture, break the connection and re-
make as a new joint. Retest for leaks after making re-
pairs.
8. Open the liquid line service valve and the compressor
discharge service valve.
Field Installed Power Wiring
An overall dimensional layout for the field installed wiring
entrance into the unit is illustrated in Figure 3-2. To insure
that the unit’s supply power wiring is properly sized and in-
stalled, follow the guidelines outlined below.
Note: All field installed wiring must conform to NEC
guidelines as well as State and Local codes.
Verify that the power supply available is compatible with the
unit’s nameplate ratings. The available supply power must
be within 10% of the rated voltage stamped on the name-
plate. Use only copper conductors to connect the 3-phase
power supply to the unit.
U S E C O P P E R C O N D U C T O R S O N L Y !
UNIT TERMINALS ARE NOT DESIGNED TO ACCEPT
OTHER TYPES OF CONDUCTORS.
Failure to do so may cause damage to the equip-
ment.
Main Unit Power Wiring
Table 3-3 list the field connection wire ranges for the main
power terminal block 1TB1. Table 3-4 lists the condensing
unit electrical data. The electrical service must be protected
from over current and short circuit conditions in accordance
with NEC requirements. Protection devices must be sized
according to the electrical data on the nameplate. Refer to
the "Electrical Service Sizing Equations", for determining;
a. the appropriate electrical service wire size based on
"Minimum Circuit Ampacity" (MCA).
b. the "Maximum Over Current Protection" (MOP)
device.
c. the "Recommended Dual Element fuse size" (RDE).
1. A field supplied disconnect switch must be installed at or
near the unit in accordance with the National Electrical
Code (NEC latest addition). Refer to the "Electrical Ser-
vice Sizing Equations" (DSS calculation), for determining
the correct size.
2. Complete the unit's power wiring connections onto the
main terminal block 1TB1 inside the unit control panel.
Refer to the customer connection diagram that shipped
with the unit for specific termination points.
3. Provide proper supply power (with over current protec-
tion) to the Compressor unit and Air Handling unit (“No
Control”, "VAV", and "Constant Volume") applications.
For chilled water systems, provide a properly sized
power supply to the circulating pump motor (EVP control
applications). Be certain that these components are
properly grounded.
4. Provide proper grounding for the unit in accordance with
local and national codes.
Содержание CAUC-C20
Страница 5: ...5 General Information Continued Unit Component Layout and Shipwith Locations 60 Ton Unit Illustrated...
Страница 8: ...8 Figure 3 2 CAUC C20 Unit Dimensional Data Recommended Clearances...
Страница 9: ...9 Figure 3 2 Continued CAUC C25 Unit Dimensional Data Recommended Clearances...
Страница 10: ...10 Figure 3 2 Continued CAUC C30 Unit Dimensional Data Recommended Clearances...
Страница 11: ...11 Figure 3 2 Continued CAUC C40 Unit Dimensional Data Recommended Clearances...
Страница 12: ...12 Figure 3 2 Continued CAUC C50 Unit Dimensional Data Recommended Clearances...
Страница 13: ...13 Figure 3 2 Continued CAUC C60 Unit Dimensional Data Recommended Clearances...
Страница 24: ...24 Figure 3 7 Typical Interface Connection Diagram for CCAD 20 through 60 Ton Package Chiller...
Страница 25: ...25...
Страница 33: ...33 Blank...
Страница 34: ...34 Figure 5 2 Typical Wiring Schematic for 20 through 60 Ton Units...
Страница 35: ...35...
Страница 36: ...36 Figure 5 3 Typical Control Panel Connections Diagram for 20 through 60 Ton Units...
Страница 37: ...37...
Страница 42: ...42...
Страница 43: ...43...
Страница 44: ...44...