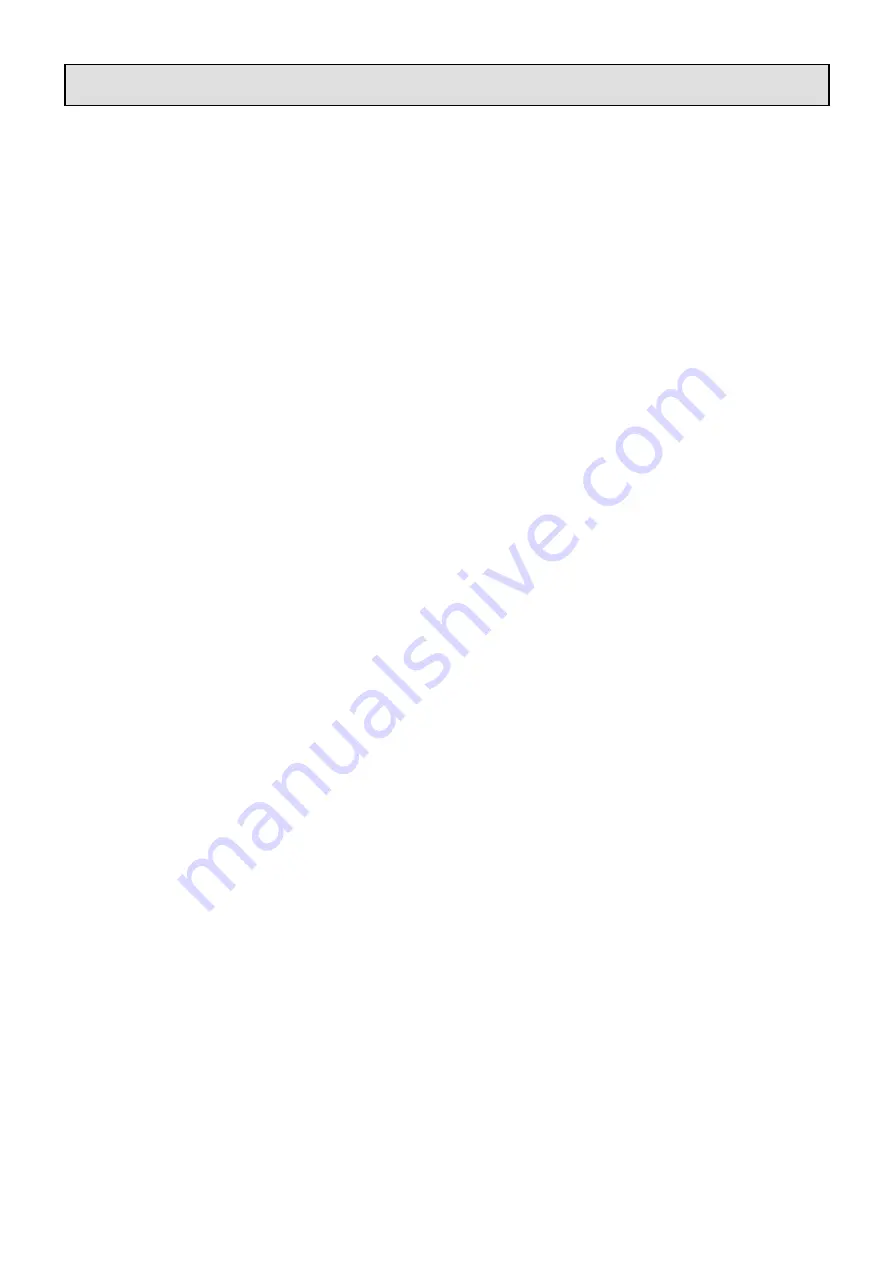
6
The whole information is gathered in various menus
according to the location of the sensor and/or the
function performed.
Chiller report menu
This menu gathers the information relating to the liquid
chiller (reading only). Active setpoints and their origins,
chilled water, air temperature, current draws, are found
in this menu.
Custom report menu
This menu is peculiar because originally it does not
include any information at all. However, the operator
can build his own menu which is comprised of read-
only information, by simply pressing the + key when in
other menus. To remove information from this menu,
simply press the - key when displayed.
Refrigerant report menu
This menu gathers the information, read-only, relating
to the refrigerant. Refrigerant pressures and
temperatures at various points of the refrigerant circuit
can be found in this menu.
Compressor report menu
This menu gathers the information, read-only, relating
to the compressor. Voltages and amps, hour and start
counters, as well as oil temperature (GP compressor
only) can be found in this menu.
Operator settings menu
This menu comprises all the particular setpoints and
operating modes existing in the unit and which are
accessible by the usual operator of the chiller. In
addition, the following can be programmed: chilled
water pump operation, temperature resets, ice-making
operation, and low ambient limit.
Service settings menu
This menu has three access levels. The first one
contains information which can be adjusted by the
customer such as the unit voltage, the validation of
over/under voltage protection, the display language,
and the programmable relay function of the units. The
keyboard can also be locked if the relating function is
validated. A second level contains the setpoints
adjusted by the service engineer to adapt the operation
of the unit to a particular site, such as the address of
the serial link, the water and refrigerant limit
parameters, and so forth. The third level contains the
configuration and protection information: number of
circuits, compressors and fans, compressor amps and
expansion valve settings.
Service tests menu
This menu allows the operator to perform some tests
when the unit is in operation or during the initial start-
up of the unit: expansion valve test, circuit locking, or
pump-out.
Diagnostics menu
This menu contains all the information on the current
faults or faults that occurred in the past. It allows the
possibility to reset a manual reset fault or to erase the
historic list of faults.
Description of the operation
Previous key
Pressing the Previous key allows the operator to
scroll up to the previous information in the current
menu. All the display items are looped, so it is
possible to scroll from the first item to the last one.
Next key
Pressing the Next key allows the operator to scroll
down to the next information in the current menu. All
the display items are looped, so it is possible to scroll
from the last item to the first one.
+ key
If this information displayed is a read-only item,
pressing the + key will add it to the operator’s menu.
if the information can be modified, the value is
increased by 1. Pressing the key for longer than 1
second will increase the value of 1 every .25 seconds.
A logical stop prevents an adjustment higher than the
maximum value; a message is displayed to indicate
this status.
- key
If the information displayed is a read-only item,
pressing the - key will remove it from the operator’s
menu. If the information can be modified, the value is
increased by 1. Pressing the key for longer than 1
second will increase the value of 1 every .25 seconds.
A logical stop prevents an adjustment higher than the
maximum value; a message is displayed to indicate
this status.
Enter key
Pressing this key allows the validation of a value after
it has been modified by pressing the + or - key.
Cancel key
Pressing this key allows the cancellation of a value
after it has been modified by pressing the + or - key
and to come back to the original value.
Auto key
Pressing this key (green) allows the unit to come back
in auto mode if it was previously placed in stop mode
with the stop key. The unit cannot be forced into auto
mode if it has been stopped by an external contact or
the serial link. When the unit is stopped by the remote
interface (Remote CLD), the local “auto” mode order
is prioritary.
Stop key
Pressing this key (red) allows the unit to go into stop
mode. In every case, and wherever the origin (except
a local stop), the stop order and stop status have
priority over a run order. The stop generated is a soft
stop, meaning the unit unloads before stopping.