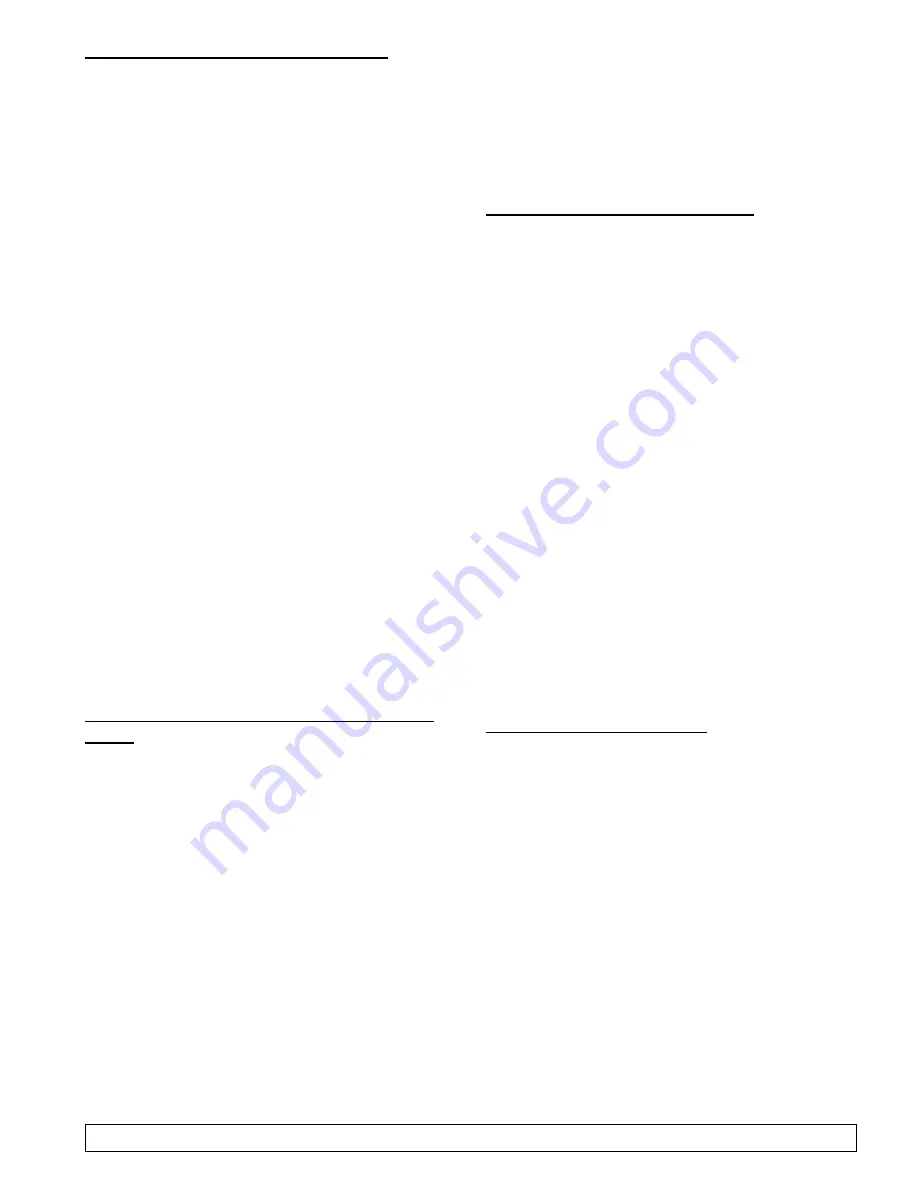
Rev.: 10/13 – NA
Installation and maintenance manual
Tractelift
®
Type II
Page 5 of 24
Copyright 2013,
Tractel
®
P4795 NA
all rights reserved.
YOUR DUTY TO TRAIN AND CONTROL PEOPLE
21. An operator must not be assigned to a hosting job or to
rigging for the job, if the person is not:
a) mentally or physically fit for that purpose
b) competent for the job to be performed
c) familiar with all application safety rules and require-
ments
d) trained for working under the above requirements
22. Never disassemble the Tractelift
™
Type II by yourself or
by your staff. Except for the operations described in this
manual, the maintenance of the Tractelift™ Type II, as
well as disassembly and repair, must be exclusively done
by qualified repairers authorized in writing by Tractel®
Inc. for USA or Tractel
®
Ltd. for Canada. Tractelift™ Type
II spare parts in accordance with the serial number of
each machine must be exclusively utilized. No substitu-
tions are allowed.
23. Never let the Tractelift™ Type II and other equipment
of a system be managed or operated by a person other
than those authorized and assigned to the job.
24. Training operators must be set up by a competent
person, or of its technical consultant. According to the
working conditions, prior to putting the equipment into
operation, contact Tractel® Inc. for the USA or Tractel
®
Ltd. for Canada. (see back cover)
25. Every job must be placed under the control of a per-
son having the required competence and the authority
for checking that all the instructions prescribed by this
manual be regularly and efficiently carried out.
YOUR DUTY OF SAFETY BEYOND THE TRACTELIFT™
TYPE II
As being only one component of the system, the Tractelift™
Type II can contribute to the required SAFETY, IF:
26. It is fitted on and with compatible equipment.
27. Other components meet the requirements of the ap-
plicable safety regulations and are of the proper quality,
and assembled to form a safe system.
28. Every support is stable, sufficiently strong, according to
the load either static and dynamic.
29. Supporting structure provides the required resistance to
every load to be applied either static or dynamic, during
operating the equipment.
30. All the requirements in strength and resistance are ob-
tained with the necessary safety factor (see regulations
and professional standards).
31. All the calculations, design and subsequent work neces-
sary to the above requirements have been made by a
competent person on the basis of proper technical infor-
mation regarding the site.
32. Do not use the Tractelift™Type II or climb the ladder dur-
ing periods of severe weather or during electrical storms.
YOUR DUTY TO AVOID TAKING CHANCES
33. Tractelift™ Type II MUST NOT be used in explosive at-
mosphere. It has not been designed for such an applica-
tion.
34.
The Tractelift™ Type II control panel is factory
set - no adjustments are necessary or allowed.
Any tampering with the factory settings voids
the warranty and Tractel is not liable for the con-
sequences of this tampering.
35. When climbing the internal ladder you must
maintain 3-points of contact, two hands and a
foot, or two feet and a hand on the ladder at all
times. you must keep your body near the middle
of the rung and always face the ladder while
climbing (see diagram). OSHA 3246-09N-05
Using improper and unsafe climbing techniques
such as sliding or Peter Panning the ladder
during decent can have a negative effect on the
motor that will void the warranty of the system.
36. The tractelift system should never be used in the
“OFF” mode. The Tractelift system must be”ON”
for use in both directions up and down, with the
correct direction selection done form the remote
keys. The correct direction must be selected on
the wireless remote before climbing up or down.
AN ULTIMATE RECOMMENDATION
In order to keep improving its products, Tractel
®
reserves its right to apply any modification at any
time to the product described in this manual.
The companies of The Tractel
®
and their
appointed repairers will supply on request their
documentation regarding other Tractel
®
products
available: Lifting and pulling equipment and their
accessories, site and facade access equipment,
handling equipment, safety devices for load, per-
sonal fall protection equipment, load and tension
indicators, etc.
Go to
www.tractel.com
The Tractel
®
network can supply an after sales
and periodic inspection service.