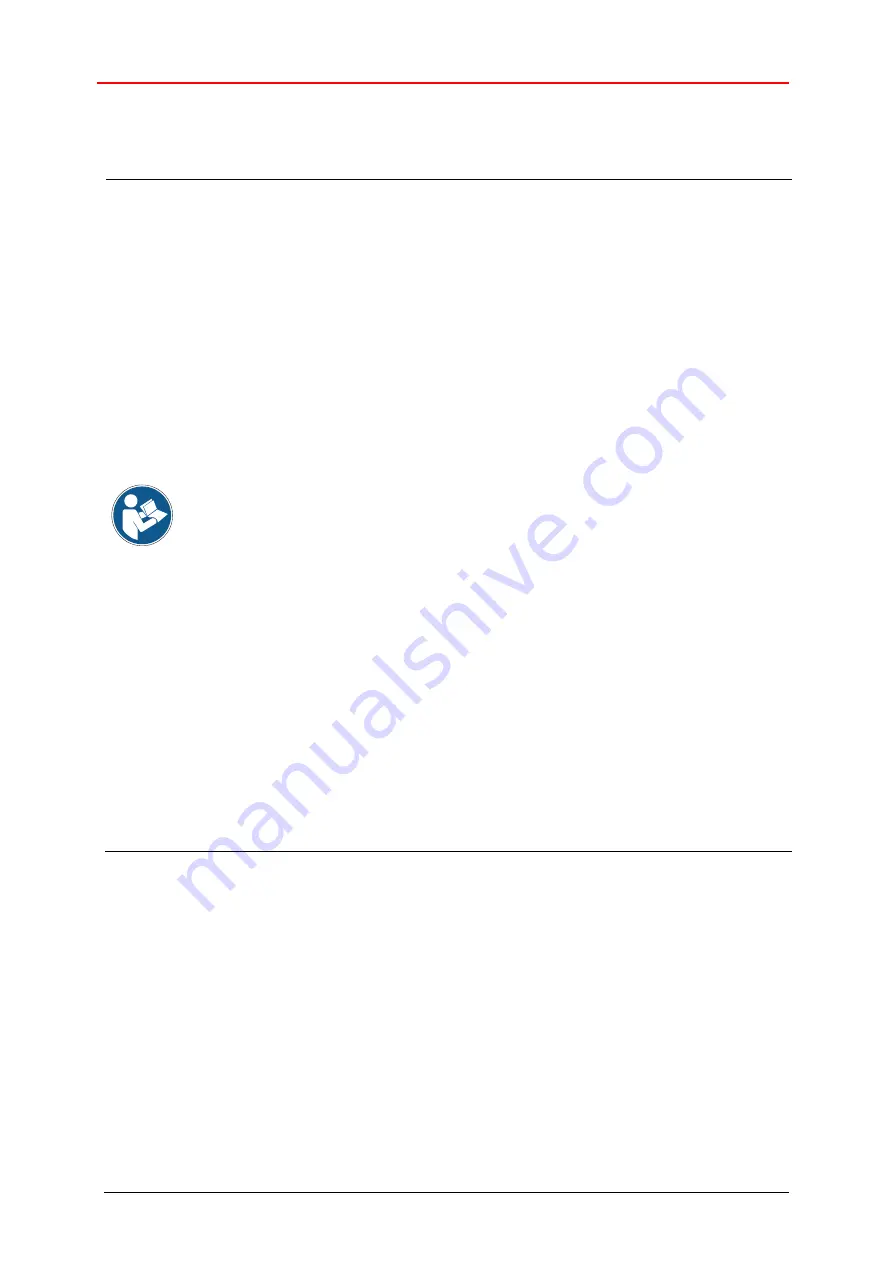
Safety instructions
TR-Electronic GmbH 2020, All Rights Reserved
Printed in the Federal Republic of Germany
Page 16 of 91
TR-ECE-BA-GB-0163 v03
10/07/2020
2.3 Safety functions of the fail-safe processing unit
The
originator
connected to the measuring system must perform the safety checks listed below.
To ensure the appropriate measures can be taken in the event of an error, the
following applies:
1.
The CIP Safety™ data channel is automatically put into the fail-safe state if
the measuring system detects an error and a safe position cannot be
output. In this state, so-called “passivated data” are output via
CIP Safety™.
Passivated data as seen by the measuring system:
CIP Safety™ data channel:
all outputs are set to 0
CIP Safety™ Device Status: in
ABORT
state
CIP Mode Byte:
Run/Idle-Bit is set to Idle
CIP Safety™ CRC:
valid
TR Safety status:
Safe State-Bit 2
4
= 0
Upon receipt of passivated data, the Originator must put the system
into a safe state. The error state can be terminated only by eliminating
the error and exiting the
ABORT
state!
2.
The CIP Safety stack is stopped if a safe position cannot be output due to
a critical error (memory error) recognized by the measuring system. This
state doesn’t permit any safety-related communication; a connection
timeout error is output.
Again, the Originator must put the system into a safe state if this
occurs. To exist this error state, try switching the supply voltage off
and then on again. The measuring system must be replaced if this
doesn’t work.
This does not necessarily affect the process data channel that can be addressed via
EtherNet/IP™. The process data continue to be output if an internal non-safety-
related channel diagnosis does not detect an error. However, these data are not
safe in terms of a safety standard.