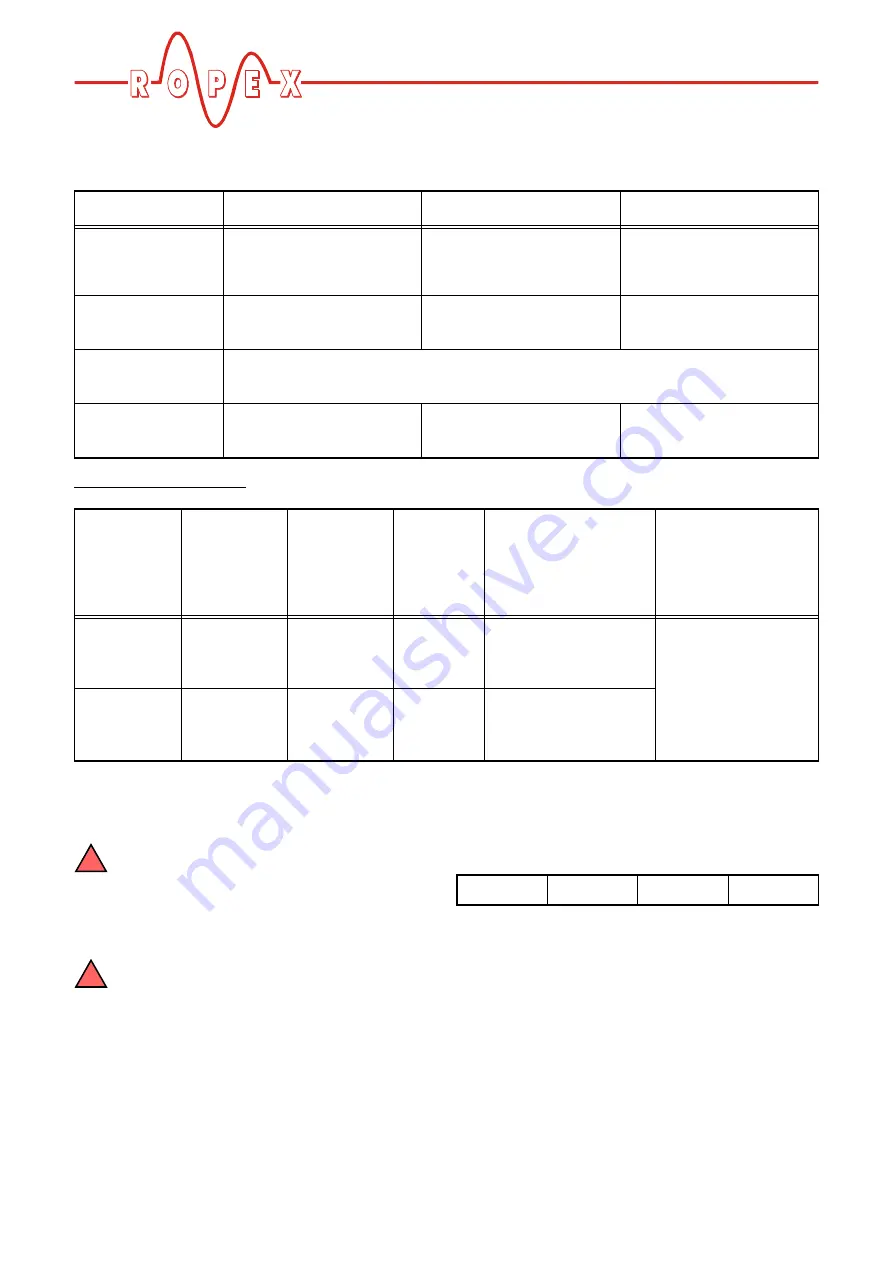
Controller functions
Page 26
RES-409
In addition to the functions shown in the diagram
above, various controller operating states are indicated
by the LEDs. These states are described in detail in the
table below:
As of February 2007 also:
10.2
CAN protocol
The following sections describe only
controller-specific functions. For general
information about the CAN bus and the system
configuration, please refer to the description
provided by your PLC manufacturer.
The CAN BUS-interface of the RES-409 sup-
ports CAN 2.0A according ISO 11898.
CANopen is not supported.
The CAN messages of the RES-409 always consist of
4 bytes. The first two bytes form a 16-bit address and
the last two a 16-bit value:
"Address.H" is the first byte to be transferred while
"value L" is transferred last.
LED
Blinks slowly (1Hz)
Blinks fast (4Hz)
Lit continuously
AUTOCAL
(yellow)
Indicates undervoltage
AUTOCAL requested but
function is locked
(as of February 2007)
AUTOCAL is running
HEAT
(yellow)
—
START requested
but function is locked
START is running
OUTPUT
(green)
In control mode, luminous intensity is proportional to heating current
FAULT
(red)
Configuration error, cannot
run AUTOCAL
Controller calibrated
incorrectly, run AUTOCAL
Error (
section 10.16)
LED
Blinks
once
(red)
Blinks
twice
(red)
Lit (red)
Lit (green)
NETWORK STATUS
blinks (red)
MODULE STATUS
blinks (green)
(alternately)
NETWORK
STATUS
(green/red)
CAN
controller:
Warning
CAN
controller:
Passive level
CAN
controller:
Bus off
Data transfer via CAN
interface
AutoBaud active
(
section 9.2.5)
MODULE
STATUS
(green/red)
—
—
—
Microcontroller
status OK
!
!
Address.H
Address.L
Value.H
Value.L
Byte 1
Byte 2
Byte 3
Byte 4