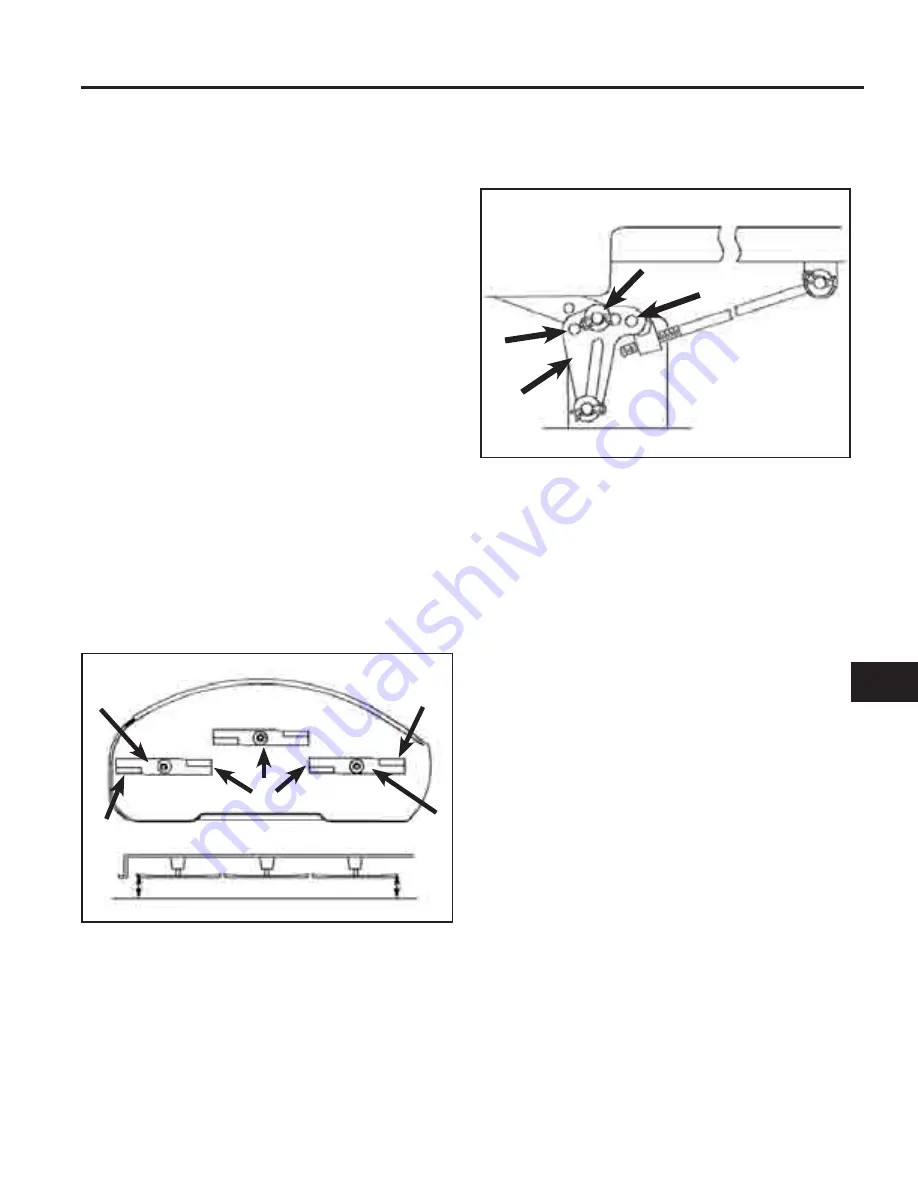
A6-13
TimeCutter Z / Precision Z Service Manual
7. To level the blade(s), reposition the leveling
bracket(s) in a different hole and install the washer
and hairpin cotter (Fig. A6 002). A front hole lowers
the blade height and a rear hole raises its height.
Adjust both sides as required.
8. Check the front-to-rear blade slope; refer to
Adjusting the Front-to-Rear Blade Slope.
Fig A6 002
fi g. 42 G000542
Fig A6 001
fi g. 41 G001774
6. Remove the hairpin cotter and washer from the
leveling bracket (Fig. A6 002).
The mower blades must be level from side to side.
Check the side-to-side level any time you install the
mower or when you see an uneven cut on your lawn.
1. Park the machine on a level surface and disengage
the blade control switch.
2. Move the motion control levers to the brake
position, stop the engine, remove the key, and
wait for all moving parts to stop before leaving the
operating position.
3. Check the air pressure of all four tires. If needed,
adjust to the recommended inflation; refer to
Specifi cations, Section 2.
4. Set the height-of-cut lever to position 4
[4”
(108mm)].
5. Carefully rotate the blade(s) side to side. Measure
between the outside cutting edges and the flat
surface. If both measurements are not within 3/16”
(5mm), an adjustment is required; continue with this
procedure (Fig. A6 001).
Leveling the Mower from
Side-to-Side
48” MOWER DECKS
6
A. Blades side to side
C. Measure here
B. Outside cutting edges
A
B
B
C
C
A. Hairpin cotter and
C. Rear hole
washer
D.
Leveling
bracket
B. Front
hole
A
B
C
D
Содержание Lawn-Boy Precision Z320H
Страница 1: ...TimeCutter Z Precision Z Zero Radius Turn Riding Mower Service Manual Consumer Products...
Страница 6: ...iv TimeCutter Z Precision Z Service Manual THIS PAGE INTENTIONALLY LEFT BLANK TABLE OF CONTENTS...
Страница 48: ...ELECTRICAL SYSTEM 5 6 TimeCutter Z Service Manual Figure 86 2 24 5...
Страница 52: ...5 10 TimeCutter Z Service Manual THIS PAGE INTENTIONALLY LEFT BLANK...
Страница 71: ...TimeCutter Z Service Manual 6 13...
Страница 72: ...TimeCutter Z Precision Z Service Manual Form No 492 4780 Revised 4 07...