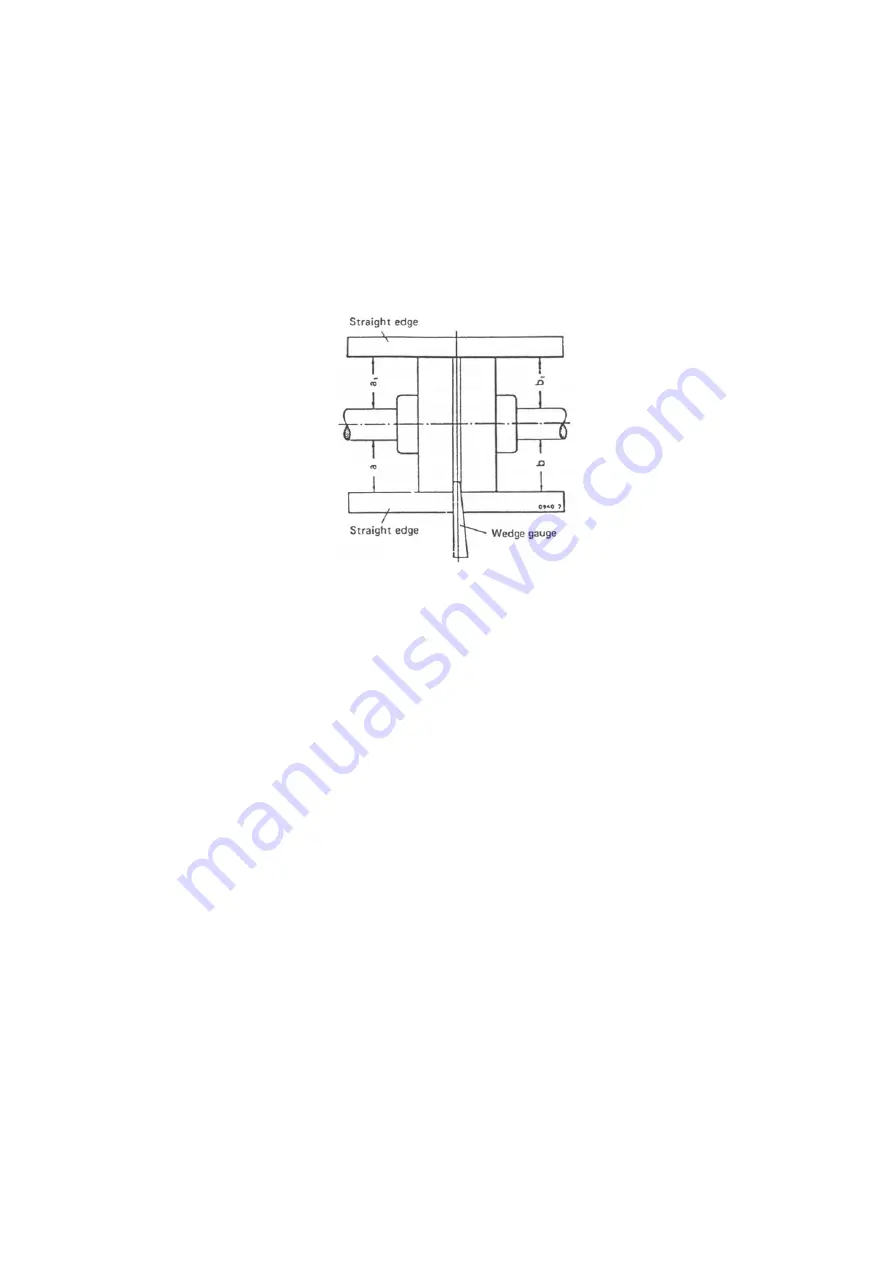
1. 2. Alignment of pump and driver
The pump shaft and the driver shaft ( motor shaft ) must be centered in line.
Follow the sequence given below for the leveling and centering work.
(1) Centering and leveling can be performed easily by holding a straightedge on the flange top of the coupling
set and inserting a wedge gauge between two coupling halves, as illustrated in Fig. 3.
In this case, a=ai, and b=bi, must be satisfied for the complete leveling and centering. Accordingly, equal
clearance between two coupling halves along its entire periphery will show that the both shafts are
completely centered and levelled.
As alternative method, a clearance gauge can be used for the checking.
Fig. 3
(2) Furthermore, a dial gauge is used for easier and more precise centering and leveling. In this case, the
clearance is measured at four points spaced with 90° while turning the coupling set, and the alignment is
perfect provided that the measured deviation in clearance is within 5/100 mm in both axial and radial
directions.
(3) Be sure to check the motor rotational direction before connecting the coupling halves. The correct
rotational direction of the pump is arrow-marked on the both suction and delivery casings. Namely, it is
clockwise viewing from the motor side.
(4) After the above check, connect the coupling halves.
1. 3. Connecting the piping
After completion of the direct coupling work, the suction and discharge pipes must be connected to the respective
flanges of the pump. Perform the piping connection with good care for the following items.
(1) When connecting the suction and discharge pipes, take proper measure to prevent piping load from
directly acting on the pump. Direct load to the pump by piping would cause trouble.
(2) The suction line must be installed in upward slope (about 1/50) toward the pump to prevent air pocket in
the case of suction lift. And it must be installed in downward slope reversely in the case of forced suction.
(3) Take care to minimize various losses of the suction pipe and avoid sudden changes of cross-section and
use of abrupt bends in the suction piping. Select the suction pipe such that the size is same or bigger than
the pump suction nozzle size.
(4) When the suction pipe size is different from the pump suction nozzle size, use an eccentric tapered pipe to
connect the suction pipe and pump suction nozzle and to prevent air pocket.
(5) After completion of the piping work, recheck alignment as described in 1.2.
Содержание MMO
Страница 1: ...Operating Instruction MMO PT TORISHIMA GUNA INDONESIA High Pressure Centrifugal Pump...
Страница 15: ...MEMO...