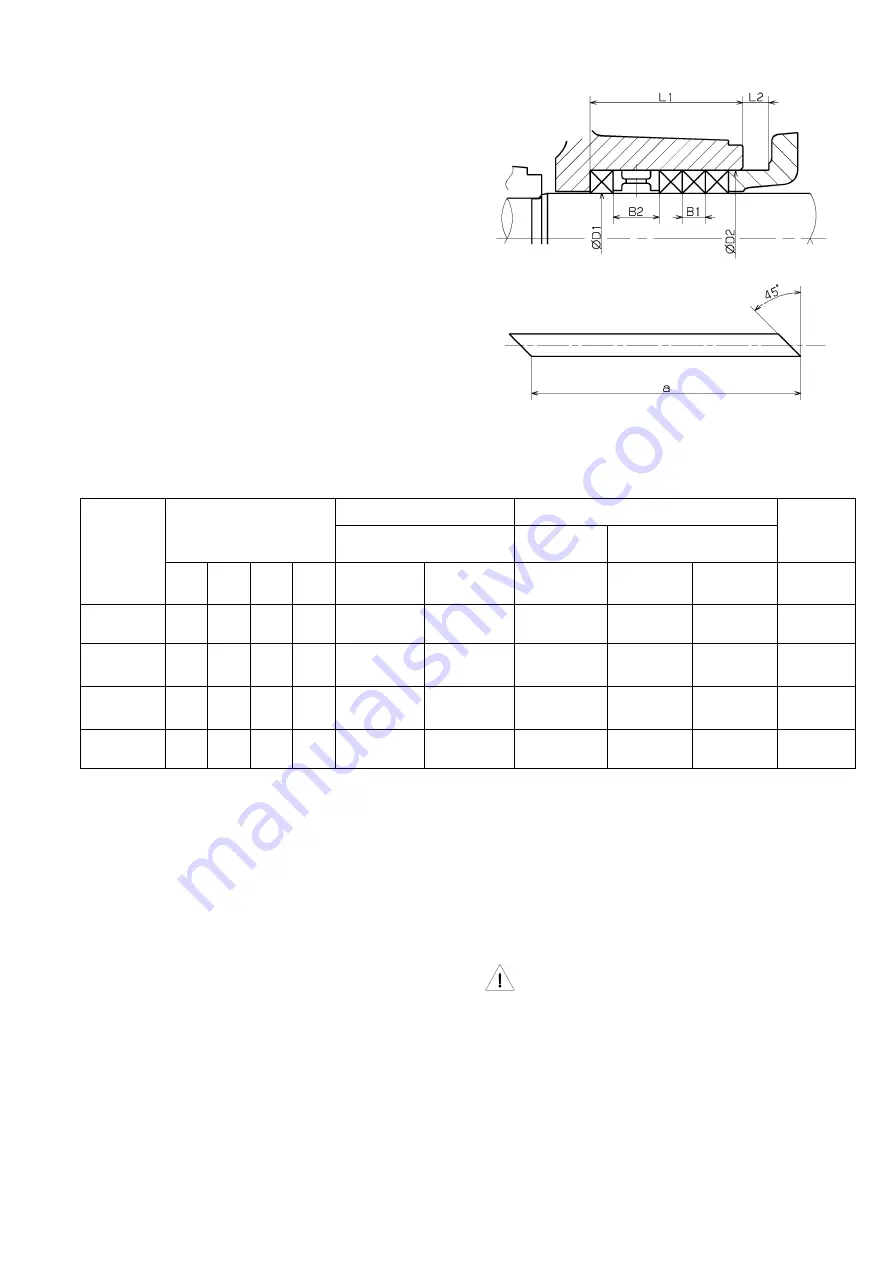
CAL Optional Design
- 8-
The gland should be slightly recessed from the casing cover. The
gland packing should be lightly tightened at the beginning. Then,
re-tighten it after running the pump for a certain period. Adjust the
gland packing so that liquid leakage from the gland is approx. 10 to
20 cc/min.
The dimension of the shaft seal and gland packing are shown in Fig
3.2-2 and Table 3-1.
Fig 3.2-2
Table 3-1 the dimension of the shaft seal and gland packing
Unit: mm
Shaft size
Shaft seal dimensions
Quantity of gland packing
Gland packing dimensions
Lantern
ring
dimensions
Lantern ring
Molded part
String-shaped part
D1
D2
D3
D4
Provided
None
D1×D2×B1
Thickness
Overall
length (a)
B2
25-360
24
40
53
9
4
6
24×40× 8
8
100.5
16
35-470
45-470
32
48
53
9
4
6
32×48× 8
8
125.7
16
45-470A
55-530
45
65
65
12
4
6
45×65×10
10
172.8
20
65-530
55
75
65
12
4
6
55×75×10
10
204.2
20
Use molded ring-shaped gland packing as much as possible.
3.3. Meters and gauge
It is recommended that a pressure gauge or compound pressure
gauge should be mounted to the pump body or the suction piping in
proximity to the pump, and that a pressure gauge should be
mounted to the discharge piping. These pressure gauges must be
provided with gradations capable of covering about 150% of
maximum operating pressure. Also connect a gauge cock to each
gauge. When pumping a corrosive liquid, use an anti-corrosion
gauge cock. When pumping liquid contains free matter or solid
matter, use a proper strainer with the gauge cock. For the long life
of each gauge, keep the gauge cock closed all the times, expect
when it is opened to read the operating pressure.
3.4. Bearings
Maintenance and inspection of the pump bearings are very
important. Maintenance and control of bearings of each lubrication
type are described below.
3.4.1. In the case of grease lubricated bearings
Inspection and control of the bearing temperature and replacement
of the ball bearings (3210) are required at an appropriate timing.
Heat-resistant grease is sealed in the bearing. The
maximum permissible temperature thereof is
90
degrees C max
on the bearing housing (3300) surface
or ambient
temperature plus 55 degrees C max
.
The bearing replacement intervals vary depending on operating
conditions. During continuous operation, the bearings must be
replaced at an interval of approx. 9000 hours, as standard. In the
case of short-time operation, it is recommended that the bearings
should be replaced every two years. Further, it is recommended to