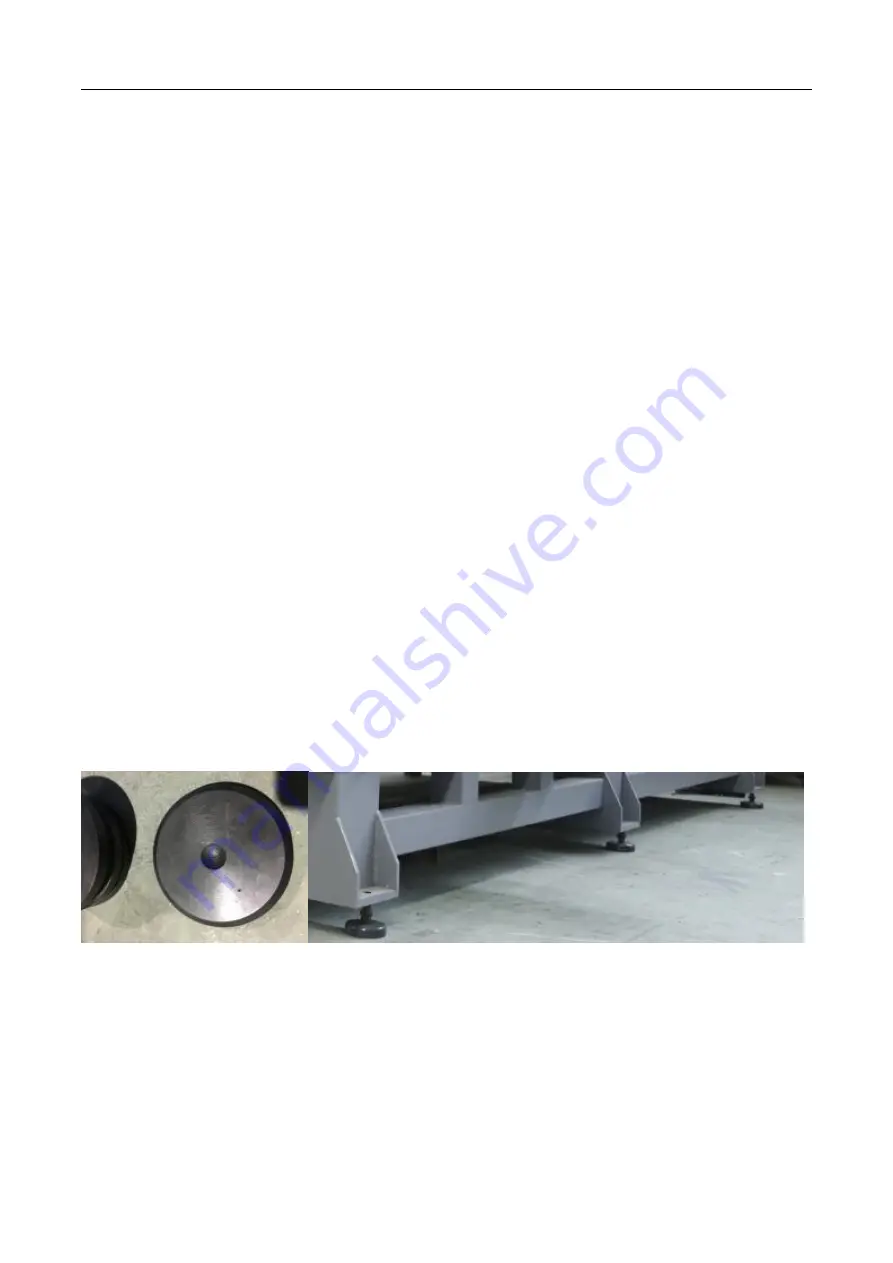
TOP CNC
Machine No: DB1802020101
Machine Model: TC-1631A
4
I. Product Inspection
The machine is strictly inspected and packaged before leaving the factory. Please check before use. Please contact your
local dealer if there are any problems.
Please verify the
following
1. No machine damage.
2. All machine accessories are included.
3. Machine model.
II. Machine installation
Installation environment
1. Utilize a dry environment.
2. Finished level surface.
3. No electromagnetic interference.
4. Ambient temperature of 10 °C ~ 40 °C. If the ambient temperature is more than 40 °C above, please place
in a well-ventilated place;
5. Verify Input voltage is 220V 3ph along with proper grounding.
6. If voltage is not stable a voltage regulator may be required.
Machine installation steps
1. Remove the machine from its pallet and place in the desired working position. Install the base plates on
the machine feet and level the machine using the adjustable feet. Then place the electrical control box on
the left side of the machine.
2.
Unbox Y1 & Y2 servo motors and connect them to their reducers. There are 5 hex bolts that secure the
servo motors to the reducer. The 5
th
bolt can be accessed via the opening seen in the middle picture below.
Once the motors are secured next attach the motor cables and install the metal covers
.