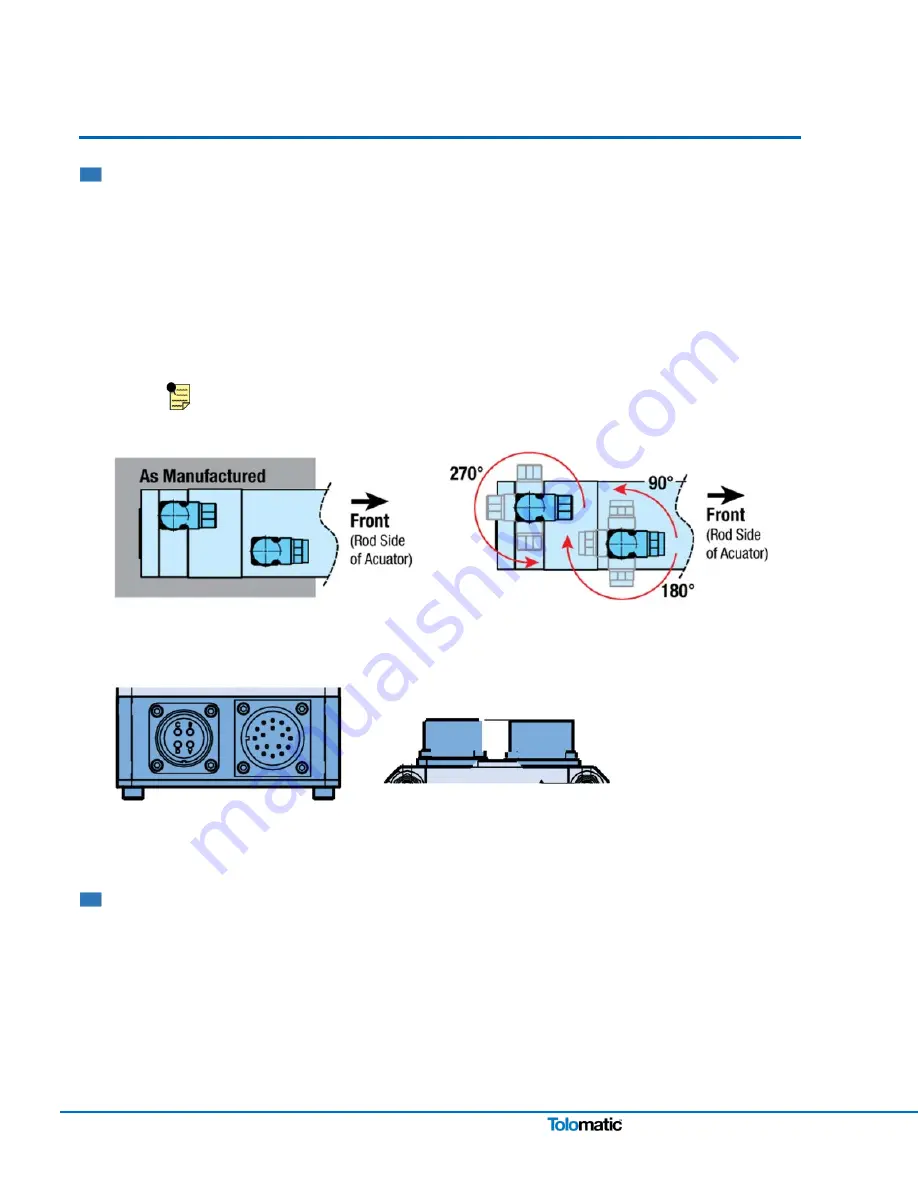
2700-4001_22 IMA Manual
25
Last Revision: 12/14/2021
5:
E
LECTRICAL
I
NSTALLATION
5.1 Connector Orientation
The IMA is manufactured with both the power and feedback connectors facing forward (toward rod end). The
standard Tolomatic connectors are shown in figure 5.2 below. Tolomatic can mount the connectors in the
orientation desired by the customer, or be rotated during installation. The Tolomatic IMA Actuator is manufactured
to fit many different connector configurations. Many drive manufacturers have specific connectors/pinout/wiring for
integrating the Tolomatic IMA Actuator into operation. Reference 5.4 for available configurations. Depending on the
connector choice, some connectors may be rotated from -90° to 180°.
For the Tolomatic standard connectors it is not necessary to loosen the screws retaining the connectors. Just
carefully rotate to the desired orientation.
Do not apply excessive force while rotating connectors.
Figure 5.3: Connector rotation. Note that the Tolomatic standard connectors may be rotated from -90° to +180°
allowing for cables to connect toward the front (rod end, as manufactured), to either side, both sides, or back of
actuator.
Figure 5.4: Drawing of box mount connectors used on some Tolomatic IMA Actuators.
See individual encoder/connector in section 5.4 for details.
5.2 Feedback Information
IMA actuators may use a digital encoder, multi-turn absolute encoder or a single-pole resolver as the rotary
feedback device. The selection of the feedback device is dictated by the drive used to operate the actuator. Each
drive has specific requirements for the feedback on the motor. Not all resolver-based drives can use the same
resolver, resolver alignment, or relative direction of resolver rotation. Not all encoder-based drives can use the
same encoder, encoder alignment or relative direction of encoder rotation. Many drives offer software that allows
the entering of parameters or the downloading of "motor data files" that dictate how the feedback must be set up
on the motor. Tolomatic can provide many of these "data files" or the proper parameters to enter. Entering motor
parameter data to some drives may require assistance from the drive manufacturer.