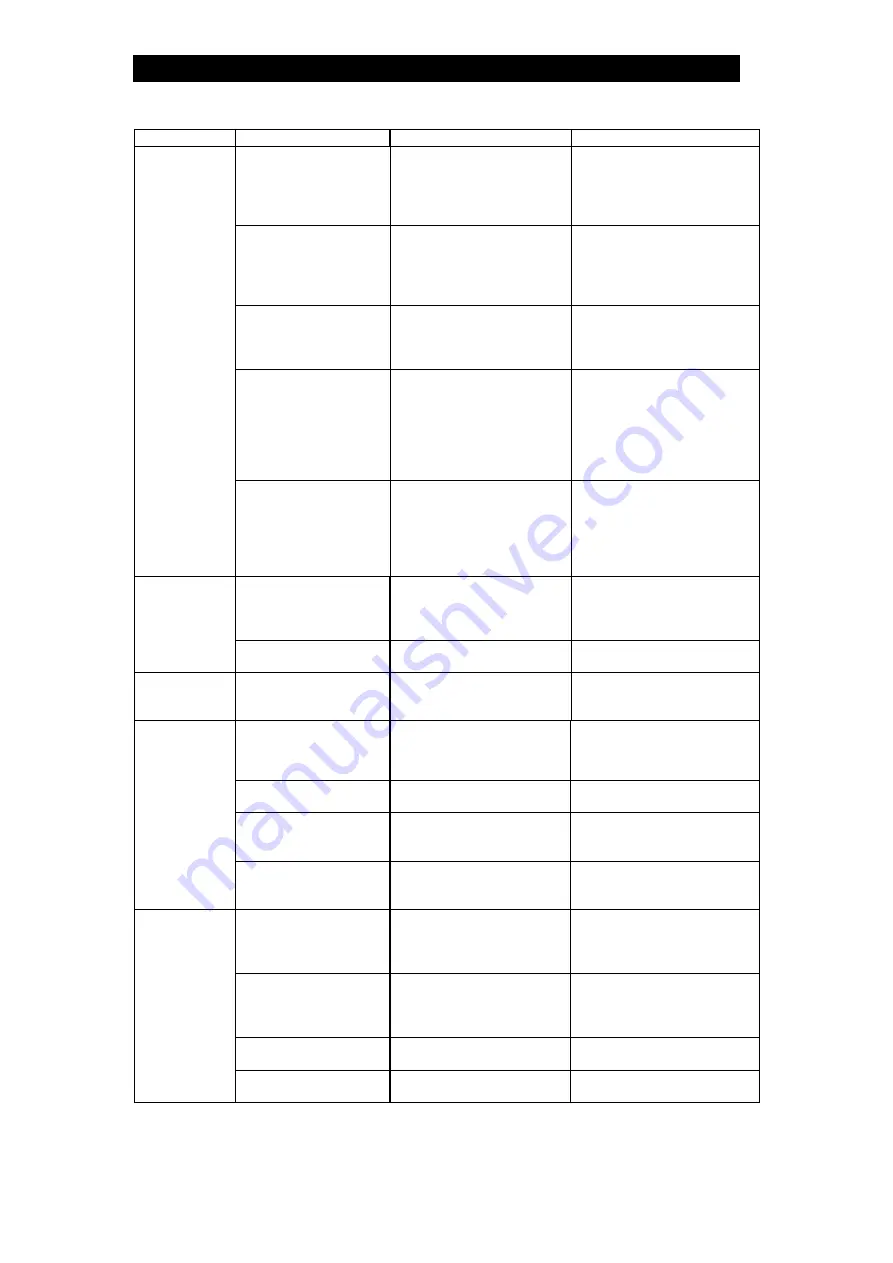
19
172-65443A-01 (CV-COS) 17 Nov 2014
Problem Cause
Diagnosis
Remedy
(Countermeasure)
Air is not being
supplied to the
positioner
Make sure that the
compressor is operating as
it should; make sure that
the regulator connected to
the positioner inlet is set
Initiate the supply of the
designated air supply
pressure to the positioner
(Confirm product
specifications)
The input signal wiring
is incorrectly
connected
Check to make sure the
wiring is connected to the
correct terminals and that
the + and - polarity is not
reversed
Correct the connections
The input signal is not
being input
Check that 4 to 20 mA is
being input by the
positioner connection
terminals
Repair the operation signal
origin or repair the signal
wiring
Positioner’s internal
parts are broken
(the diaphragm is
cracked, etc.)
Check to see if any
unusual noise is coming
from the positioner
Replace with a new
positioner/actuator unit
[Check to make sure that
the valve is not operating
(traveling) too often and
that the ambient
temperature is not too high]
No movement
at all
There is water or oil
inside the positioner
Check to see if there is
water or oil entrained in the
supply air; check to see if
the humidity at the control
valve piping location is too
high
Replace with a new
positioner/actuator unit and
improve the quality of the
air supply
There is water or oil
inside the positioner
Check to see if there is
water or oil entrained in the
air supply
Replace with a new
positioner/actuator unit and
improve the quality of the
air supply
Valve opens
and closes too
slowly
The filter regulator is
clogged
Check the filter
Clean the filter or replace
with a new filter
Valve travel is
unstable
The setting of the
controller is faulty
Check the set value based
on the controller’s PID
parameters
Adjust the controller's
setting values
There is a build-up of
dirt on the trap valve
seat or on the float
Check the trap valve seat
and the float
Clean or replace with a new
trap valve seat or float
The body is installed
tilted
Check the installation
conditions
Correct the installation
The float is deformed
Check the float
Replace with a new float
(Inspect for water hammer
or freezing)
Steam is
blowing
There is vibration in
the piping
Check the piping
conditions
Remove the source of the
vibration or reinforce the
piping supports
The primary pressure
exceeds the trap valve
seat maximum
working pressure
Check the primary
pressure
Change to a suitable
pressure
Water is inside the
float
Check the float
Replace with a new float
(Investigate to see if the
flow medium contains
corrosive substances)
Output piping is
clogged
Check the outlet piping
Clean or modify the piping
No condensate
is discharged
The trap valve seat is
clogged
Check the trap valve seat
Clean or replace with a new
trap valve seat